This integrated approach to implementing composite repair solutions can reduce carbon emissions by 66% compared to traditional methods, says Antonio Caraballo, Inspection & Integrity Management Services Director, ICR, UK
The repair and maintenance of assets has always been an important element in the oil and gas industry and is essential to ensuring the reliability and safety of operations. Continuing to be a priority in today’s energy industry, throughout the transition to explore greener energy alternatives, the importance of corrosion control remains at the forefront of operator’s minds. Inadequate or infrequent inspection and management of assets can lead to a range of risks including production failure and loss of containment, potentially leading to catastrophic impacts on the personnel, plant and environment. As a vital factor in optimising the productivity, production, and downtime of operations whilst mitigating potential risks, corrosion control is essential to minimising operational and repair costs and extending asset life.
With the risk of health and safety issues and disruption to operations, corrosion can also compromise the appearance, performance, strength, and load-bearing ability of assets. Corrosion management will allow the operator to mitigate any safety and environmental hazards, as well as prevent any production and financial losses. As a key challenge facing the industry today, corrosion can lead to production delays, equipment failure, operational expenditure and safety hazards.
ICR Integrity is an industry-leading, technology-enabled provider of specialist repair, inspection and integrity management solutions to a diverse range of industries. The company’s well-established repair and maintenance division offers clients world class repair solutions providing greater asset uptime and reliability while saving time and cost compared to traditional repairs. The newly formed specialist inspection and integrity division reflects the company’s focus on innovation and technology advancements in support of its global clients’ integrity management requirements.
The traditional oil and gas industry, which ICR has a strong presence in, requires solutions that provide validation and assurance on the condition of their assets, as well as any repairs that have been undertaken. With a strong focus on the environment when carrying out testing, avoiding carbon intensive techniques is essential to the sector. Many ageing assets have composite repairs reaching the end of their design life, meaning there is an increased requirement to revalidate or extend the life of the repairs, allowing operators to avoid costly replacement options that may require a full shutdown of the asset. Regulatory bodies, have a strong focus on the integrity management and condition monitoring of repairs. Being able to inspect the defined life repairs is therefore a key enabler in ensuring safe and reliable operations for extended time periods.
Based on the principles of acoustic inspection methods with pitch and catch, ICR Integrity’s innovative new Non-Destructive Testing (NDT) technique, called INSONO. It provides resonance and mechanical impedance analysis to detect and size any flaws in the inspection of engineered composite repairs. The technology has been validated by The Welding Institute (TWI) and has patent and UKAS accreditation pending. A hand-held scanner creates 3D models and visual representation of the composite repair, allowing for precise dimensions to be used in the assessment. Any defects in three main areas of concern can then be detected – in the bond line, the interlaminar and the steel substrate.
With over 30 years’ experience, ICR is internationally recognised as a service-leader and a key-player in the ongoing development and adoption of composite technology. INSONO complements its industry renowned Technowrap™ range of engineered composite repairs and assures operators that their composite repairs are fit for purpose, satisfying regulatory body guidelines regarding inspection criteria. It also allows for the extension of defined life repairs reducing waste whilst avoiding high-carbon emissions from traditional steel replacement alternatives.
Inspection techniques currently available are not practical to deploy in the field and many are unable to access complex geometries with a single technique or product. INSONO is hand-carried and requires only one Technician, meaning inspections can be carried out in higher risk areas where they may not have been previously considered.
ICR is internationally recognised as a service-leader and a key player in the ongoing development and adoption of composite technology. The versatile product range offers practical and cost-effective rehabilitation of pressure systems and structural components with minimal disruption to operations, typically delivering valuable cost savings. The repair systems can not only be applied to live systems with no impact on production, but also offer a low greenhouse gas (GHG) emissions alternative to steel replacement. Replacing large steel equipment is energy intensive and requires the production of a new part. By repairing their equipment, ICR’s clients avoid the emissions associated with steel production and transportation as well as the energy required to perform the replacement.
Technowrap™ repair solutions can be engineered for anywhere between 2 and 20 years, which can be equal to the lifetime of a traditional replacement and as such are directly comparable to a replacement solution, depending on the anomaly type. ICR compared the carbon impact of using its repair system technology for the repair of a 2-metre section of 8” carbon steel pipework (85.1 kg) located 225 miles offshore from Aberdeen. The findings established that the repair system reduced emissions by 66% compared to the traditional replacement method.
On a recent project in the Northern North Sea, an operator client asked ICR to review various sections of pipework that had sustained severe corrosion resulting in wall thinning below the minimum allowable wall thickness of the pipework. Due to the location of the pipework being underneath the helideck, the client required minimal impact on production and an engineered Technowrap™ composite solution was chosen as the most efficient, engineered solution. The scope of work saw the delivery of the repair with a 20 year repair lifetime. Technowrap™ trained personnel installed the 2K materials, completing the repair with a design temperature of the line of 90ºC.
As there was no shutdown required, the solution offered was extremely cost effective. Due to the complexity of the location (under the helideck), ICR mobilised a multi skilled rope access trained composite repair team who implemented the repairs, removing scaffolding requirements. The appropriate risk assessments were carried out to minimise any potential risks associated with the work. In order to achieve the required adhesion grit blasting to the cleanliness standard of SA 2.5 was completed prior to the application.. As a result, the scope was delivered on time, within budget and with no incidents or accidents. The client was given the further assurance through the bespoke engineering and design calculations for each repair, carried out to code requirements in accordance with ISO 24817 and ASME PCC-2.
With safety, environment, efficiency and reliability as a top priority in the industry, ICR is leading the ongoing development and adoption of composite technology to support operators globally. Actively working in close collaboration with clients to ensure the structural integrity of assets is maintained with minimal disruption to operations, ICR is able to support clients on their journey to sustainability.
With extensive experience dealing with some of the most challenging projects in the industry, ICR’s integrated approach to implementing composite repair solutions and specialist engineered clamp designs can reduce emissions by 66% compared to other methods. With sustainable operations at the forefront of the industry’s agenda, this further allows clients to repair and maintain their assets to avoid costly operational disruption and potential safety and environmental hazards.
To view this article in World Pipelines click here
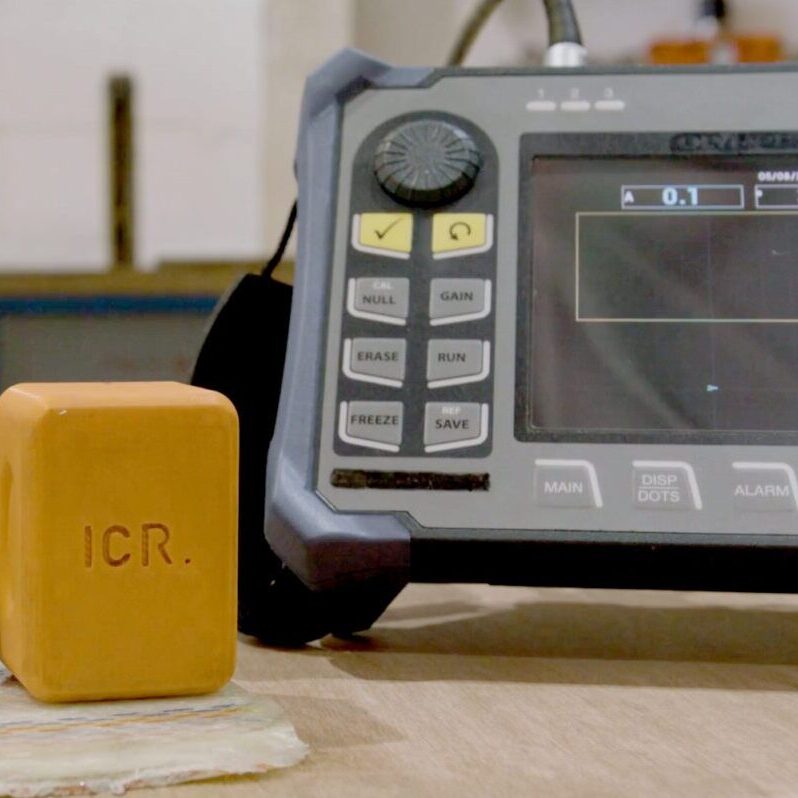
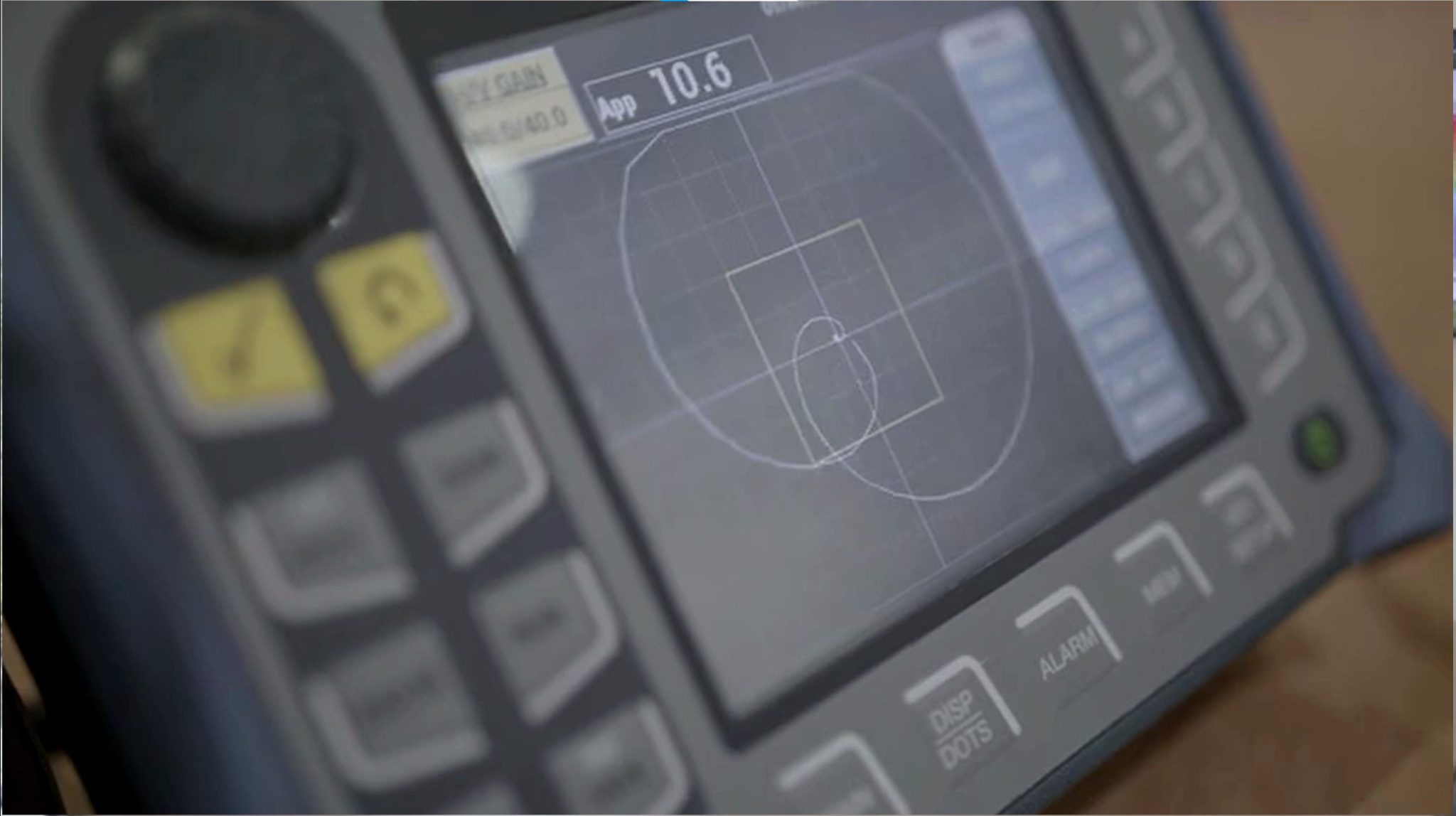
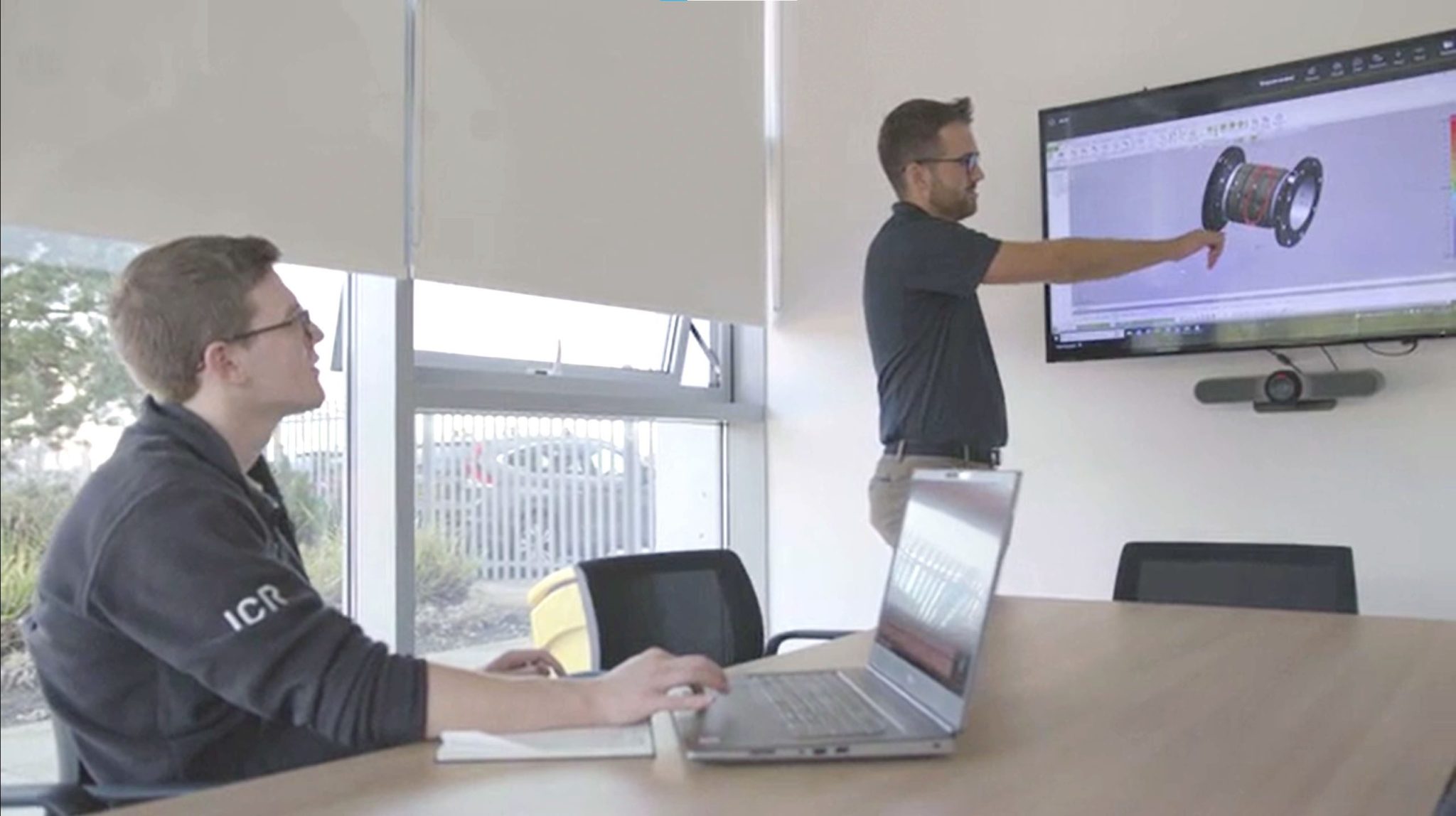
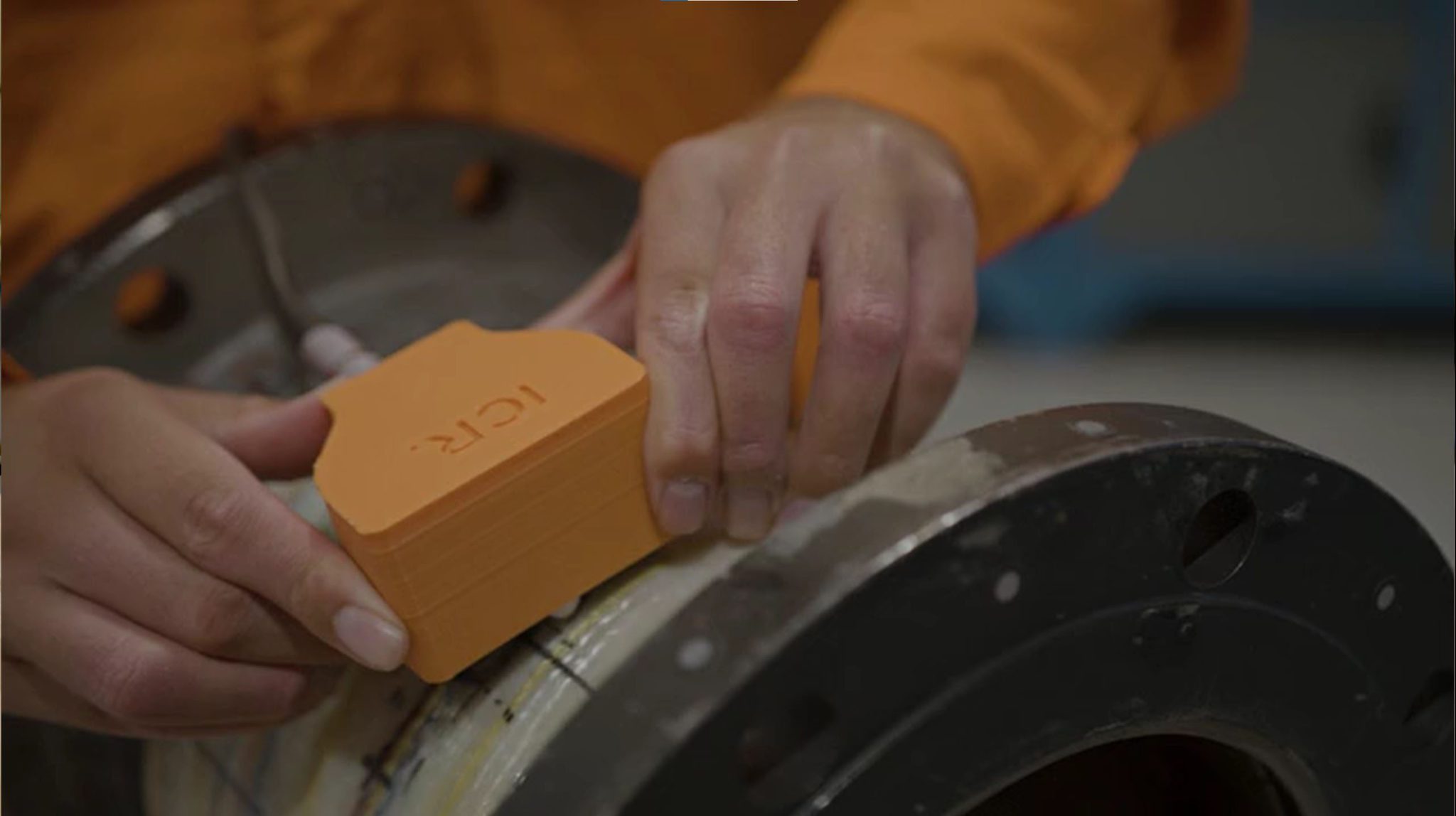