Client: Major Operator
Location: Qatar
Client challenge
Our global partner in Qatar collaborated with a major oil and gas company to address the challenge of providing effective corrosion protection for subsea pipelines. The goal was to apply Technowrap™ 2K as a corrosion protection system, and the trial installation was initially conducted onshore. Subsequently, the protected pipe lengths were transported offshore using a pipe lay barge and installed on the seabed.
What we did
The project covered a range of pipe diameters, including 6”, 8”, 10”, and 12”. After a successful trial, this process was extended to a subsea hydrocarbon and gas pipeline spanning 12 kilometers. Prior to the trial, both our client and contractors conducted extensive testing and inspections to ensure the efficacy of the corrosion protection system. The trial itself took 12-14 weeks to complete, with a crew of six Technowrap™ 2K Installers working on a 24-hour, 12-hour rotation to encapsulate the various welds with layers of Technowrap™ 2K composite repair following hydrotesting of the welded pipe sections.
Results
Our composite repair system demonstrated remarkable success in this application and received approval for corrosion protection applications. In this specific trial, our client requested a longer service life, ranging from 25 to 30 years, exceeding the standard lifetime designs of up to 20 years. Through a meticulously engineered solution, a 25-30 years lifetime could be provided, surpassing the longevity of any other paint and epoxy system available on the market.
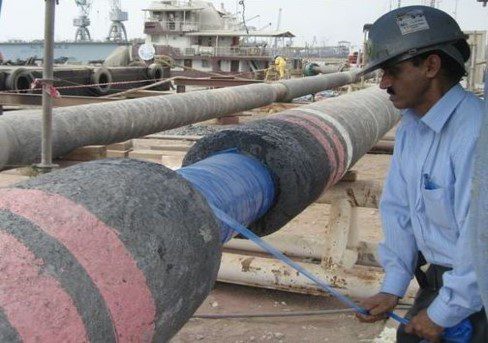
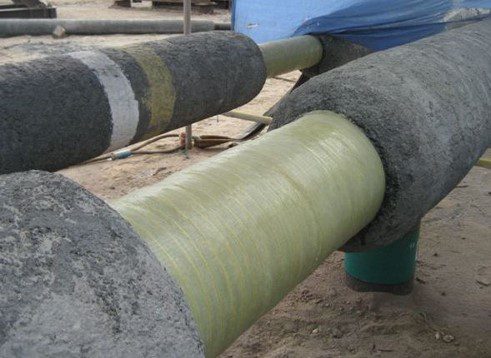
Client challenge
Our client faced a critical challenge when a catastrophic failure occurred in their 56-inch water export line, resulting in a 1.7-meter-long rupture. Concerns arose regarding the possibility of similar defects within the line were compounded by several critical factors, including:
Operating the 56” water export line under a high line pressure of 22 bar, heightened safety concerns regarding the potential for injury resulting from a breach.
The consequential loss of production due to the interruption of the injected water supply.
The catastrophic rupture’s root cause was identified as seam weld root corrosion, compelling the replacement of the damaged section and the launch of a comprehensive preventative maintenance campaign covering the entire pipeline.
What we did
In response to the urgent need for a solution, we provided our client with an engineered design, materials, and skilled labor within a 24-hour timeframe. Our approach focused on designing a seven layer engineered Technowrap™ SRS repair solution specifically aimed at structurally restoring the integrity of the pipework, effectively preventing future seam weld ruptures.
Results
The rapid implementation of our solution yielded significant results and benefits:
The quick restoration of the water export line, with it becoming operational only four days after the initial rupture, played a pivotal role in minimising downtime. This achievement not only eliminated the need for costly and time-consuming pipe replacement but also resulted in substantial cost savings. Additionally, our prompt resolution of critical health, safety, and environmental concerns related to the rupture allowed other essential work to continue seamlessly in the area. Moreover, our intervention significantly reduced lost production time, mitigating financial losses, and ensuring the uninterrupted flow of injected water.
This case study underscores our unwavering commitment to delivering timely and effective solutions to clients grappling with catastrophic failures, thereby facilitating the swift restoration of critical infrastructure and minimizing the associated economic and operational disruptions.
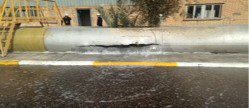
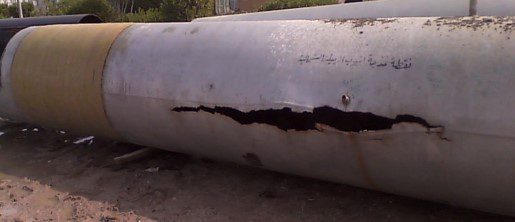
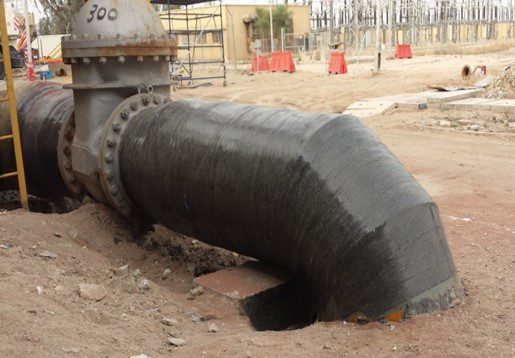
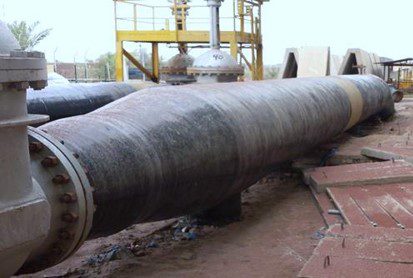
Client challenge
Our client’s 32” produced water line, was exhibiting significant internal erosion and corrosion, leaving a minimum remaining wall thickness of just 4mm. The extensive scope of the repair encompassed approximately 550 meters of pipeline, including various saddle supports, some of which were welded. The client also stipulated the need for a qualification test for the proposed repair solution, to be conducted on-site before the actual repair implementation.
What we did
Our solution began by defining a comprehensive scope of work, which included engineering an innovative design to ensure a 20-year repair lifetime. This encompassed providing trained personnel and the necessary materials, specifically Technowrap™ 2K with Technowrap™ HP PRS, to execute the repair. The line’s design parameters included a pressure of 47 bar g and a temperature of 82ºC. We meticulously developed an installation procedure for the composite repair, which was thoroughly tested and approved by the client before on-site installation. To ensure complete encapsulation of the pipeline, we also devised a detailed lifting plan for the pipeline over the supports. This plan addressed additional requirements, including applying the repair in areas where the pipework rested on the pipe supports.
Results
The execution of the qualification test was a resounding success, meeting the client’s approval and verifying the effectiveness of the repair solution. The repair was installed, confidently meeting the design pressure of 47 bar g and operating within the specified temperature range of 82ºC. Our detailed lifting plan was meticulously executed, ensuring the complete encapsulation of the pipeline. This case study showcases our dedication to delivering reliable and enduring solutions, providing clients with the confidence to address complex challenges in maintaining critical infrastructure.
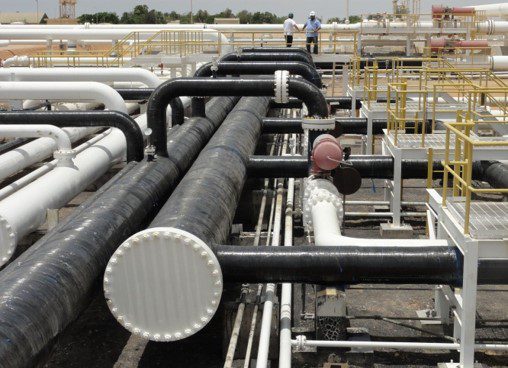
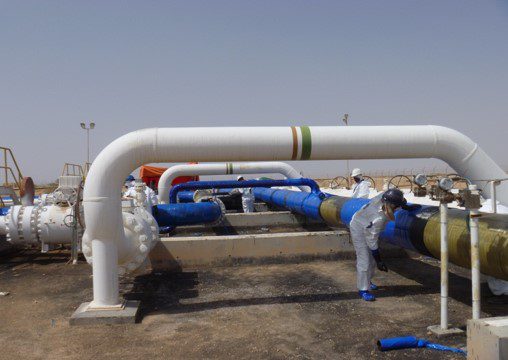
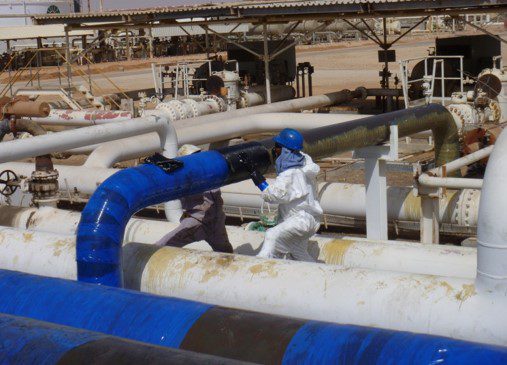
Client challenge
Our client faced a challenge involving their filter house which had multiple defects, causing water loss and impacting production. To address this issue, a four day shutdown was planned to execute repairs. The primary objectives were to restore the full integrity of the pipework and prevent further water loss, and maximise production efficiency.
What we did
During the four day shutdown, we executed a series of fully engineered Technowrap™ 2K rehabilitation system repairs to address the identified defects. These repairs encompassed a variety of diameters (24” and 40”) and geometries (straight, bend, tee-piece), with design parameters including a design pressure of 2.5 bar and a design temperature of 500ºC. The selected resin system was High Ambient 2-part Epoxy Resin, offering a repair lifetime of five years.
Results
The shutdown proved highly productive and resulted in several key benefits including;
During the allocated four day timeframe, a total of 15 severe leaks were expertly sealed and repaired, eliminating the need for costly line replacement and providing a highly cost-effective solution. We played a pivotal role in ensuring the success of this project by offering comprehensive support, including pre-shutdown site surveys, task-based risk assessments, design calculations, and surface preparations to guarantee the safety and accessibility of all repair areas.
The execution of the shutdown scope proceeded flawlessly in accordance with the agreed plan and all through-wall defects were effectively sealed using Technowrap™ 2K plates, with repairs skillfully installed to encapsulate the plates for the required minimum length. Rigorous QA/QC checks were diligently completed before station start-up, ensuring the highest standards of quality. Importantly, the entire scope was executed without any incidents, underscoring our unwavering commitment to safety and efficiency. This case study serves as a testament to our remarkable ability to swiftly and effectively address complex repair challenges during critical shutdowns, ultimately enhancing production and minimizing operational disruptions.
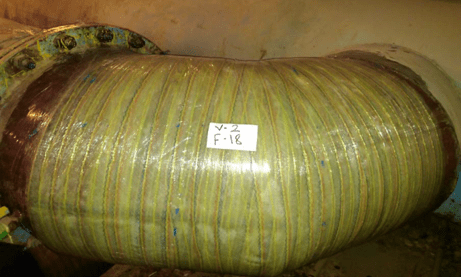
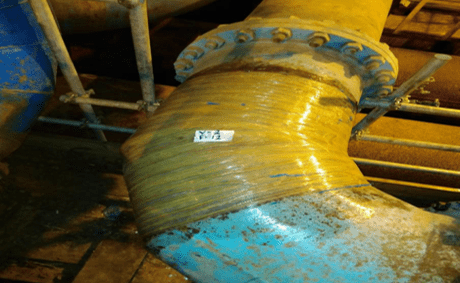
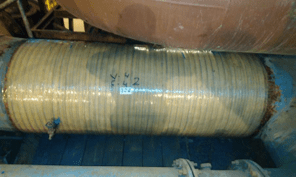
Date: May 2023
Client: International independent E&P company
Location: Dutch North Sea
Client challenge
Our client is an international independent exploration and production (E&P) company operating in the Dutch North Sea. They approached our team with a critical structural repair project involving the repair of ten beams with complex geometries and required a solution that could achieve compression on corroded beams. The objective was to provide a long-term, cost-effective repair solution while ensuring the safe operation of the bridge link. The structural repair of the bridge link beams presented several challenges that needed to be addressed.
The complexity of the beams required a solution capable of forming around the unique geometry. Additionally, achieving compression on corroded beams was crucial to ensure adequate adhesion of the repaired elements. The repair was carried out without the need for fabrication, hot work, or heavy lifting to minimise downtime and associated costs. The chosen solution required a design life of 20 years to align with the remaining lifespan of the asset.
What we did
To meet the specific requirements of the structural repair, our team employed a combination of two advanced fabric systems:
- Technowrap™ SRS (Structural Repair System)
- Technowrap™ HPPRS (High-Pressure Pipe Repair System)
By combining these fabrics, we created a bespoke laminate solution tailored to the unique repair scenario of the bridge link beams.
The repair process involved the following steps:
Assessment and preparation: The bridge link beams were thoroughly assessed to identify the extent of corrosion and damage. The corroded areas were cleaned and prepared for the application of the composite repair system.
Fabric selection and laminate formation: Technowrap™ SRS and Technowrap™ HPPRS fabrics were selected based on their individual strengths and characteristics. A customised laminate was created, leveraging the unique properties of each fabric to achieve optimal strength in the correct load path.
Application: A supervisor and two technicians were deployed to carry out the repair. The laminate system was applied to the bridge link beams, ensuring full coverage and conformity to the complex geometries of the structures. The installation process required no fabrication, hot work, or heavy lifting, streamlining the repair and minimising downtime.
Quality assurance and longevity: Rigorous quality assurance measures were implemented to verify the effectiveness of the repair. The composite laminate solution was designed to provide a 20-year design life, aligning with the remaining asset life.
Results
The successful implementation of the composite repair solution for the bridge link beams provided several outcomes and benefits, providing a long-term solution designed to last the remaining 20-year life of the asset. This ensured the continued safe operation of the bridge link and minimised the need for future repairs or replacements. Additionally, the repair solution required no fabrication, hot work, or heavy lifting. This streamlined the installation process, reducing downtime and associated costs. In terms of cost, the composite repair solution offered a cost-effective alternative to full beam replacement, saving the client significant expenses while maintaining structural integrity.
The quick application of the repair solution ensured the safe future operation of the bridge link and the repaired beams were capable of withstanding the operational loads and environmental conditions in the Dutch North Sea.
The structural repair project for the bridge link beams showcased our team’s expertise in developing and implementing advanced composite solutions for complex geometries. By combining Technowrap™ SRS and Technowrap™ HPPRS fabrics, we successfully addressed the challenges posed by the client. The efficient, cost-effective, and reliable repair solution enabled the client to continue safe operations and provided longevity of the asset in the Dutch North Sea.
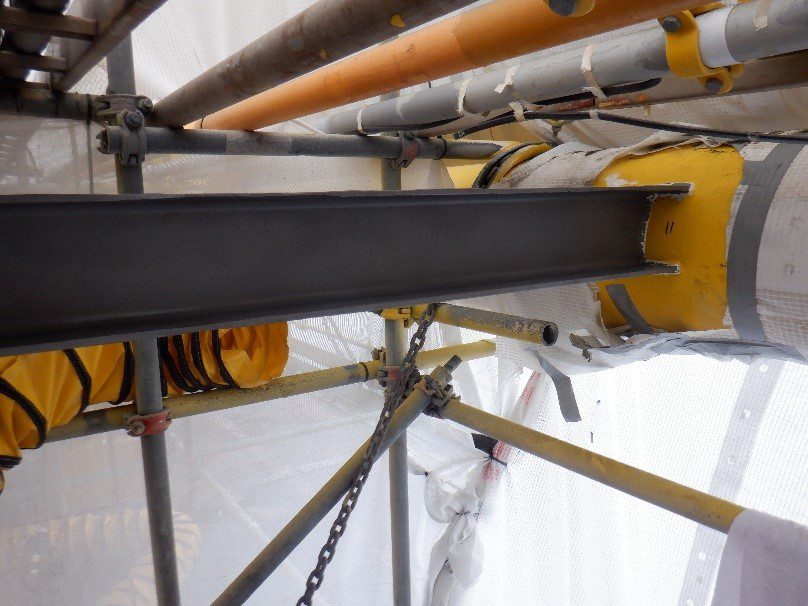
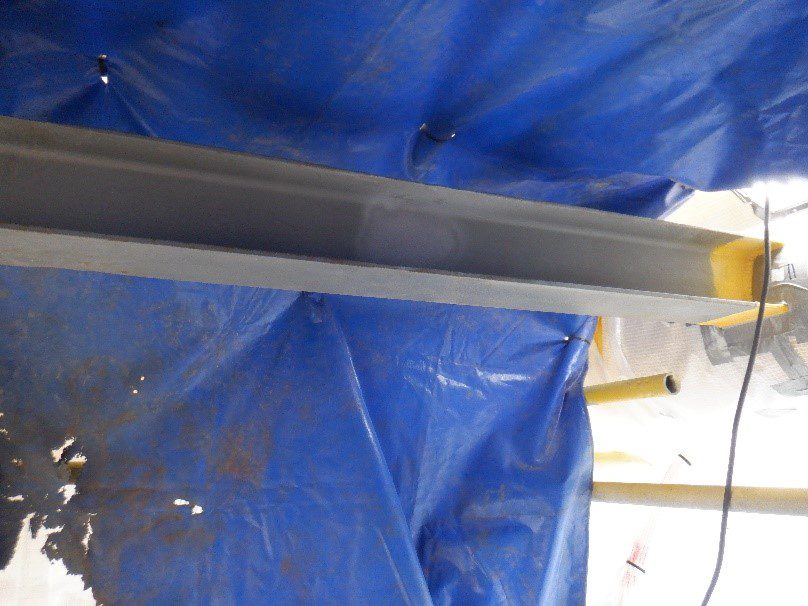
Date: April 2023
Client: National Oil and Gas producer
Location: UAE
Client challenge
Our client is a prominent energy operator based in the Middle East and approached our team with a critical repair project involving a de-ethaniser column. The objective was to address specific problem locations within the column, spread across six different vertical positions. The project required a reliable and efficient solution to mitigate the risk of further damage, while ensuring minimal revenue loss during the repair process.
What we did
The de-ethaniser column, measuring just over 7.5 metres in height with a diameter of 3.05 metres, had encountered structural issues and cracks that needed immediate attention. Traditional repair methods involving hot work were not feasible due to the potential for revenue loss, and safety concerns associated with the presence of flammable substances. In addition, the repair solution needed to consider the prevention of galvanic corrosion and provide pressure containment capabilities while limiting stress on the steel structure to prevent crack propagation.
Our team proposed an innovative repair solution utilising advanced composite materials, specifically glass fibre and carbon fibre, to address the unique challenges faced by our client. By employing this composite approach, we ensured a durable and efficient repair without resorting to hot work, minimising any potential revenue loss.
The repair process involved multiple steps:
Surface Preparation: The affected areas of the de-ethaniser column were thoroughly inspected, cleaned, and prepared for the application of composite materials.
Galvanic Corrosion Prevention: To safeguard against galvanic corrosion, a single layer of glass fibre was applied as a barrier between dissimilar metals present in the column.
Composite Application: A total of 20 layers of carbon fibre, employing various lay-up techniques, were strategically applied to the problem locations within the column. This composite configuration aimed to provide pressure containment, withstand axial loads, and limit stress on the steel structure to prevent further crack propagation.
Curing and Quality Assurance: The composite layers were allowed to cure under controlled conditions to ensure optimal bonding and structural integrity. Rigorous quality assurance tests were conducted to verify the effectiveness of the repair.
Results
The successful implementation of the composite repair solution resulted in several significant outcomes and benefits:
Enhanced structural integrity: The repaired de-ethaniser column demonstrated improved structural integrity, as the composite materials effectively contained pressure and limited stress on the steel structure.
Avoidance of galvanic corrosion: The glass fiber layer acted as an effective barrier, preventing galvanic corrosion and ensuring long-term durability of the repaired column.
Reduced loss of revenue: By avoiding hot work, our repair solution eliminated the need for significant downtime and revenue loss that would have occurred with traditional repair methods.
Extended service life: The repair solution was designed to provide a five-year lifetime, ensuring the longevity and reliability of the de-ethaniser column.
The de-ethaniser column repair project demonstrated our team’s ability to develop innovative solutions tailored to our client’s specific requirements. By leveraging our advanced composite materials, we successfully addressed the structural issues of the column, mitigated the risk of galvanic corrosion, and ensured the safe and efficient operation of the facility. Our client benefited from a cost-effective repair solution, minimal revenue loss, and an extended service life for their critical equipment.
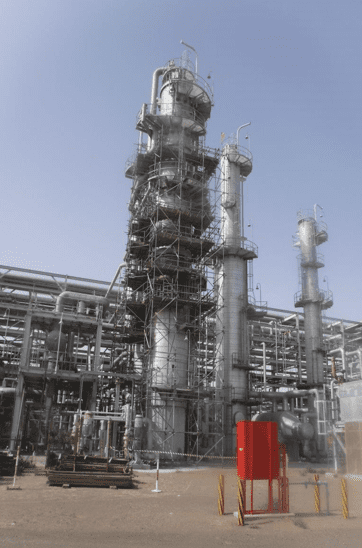
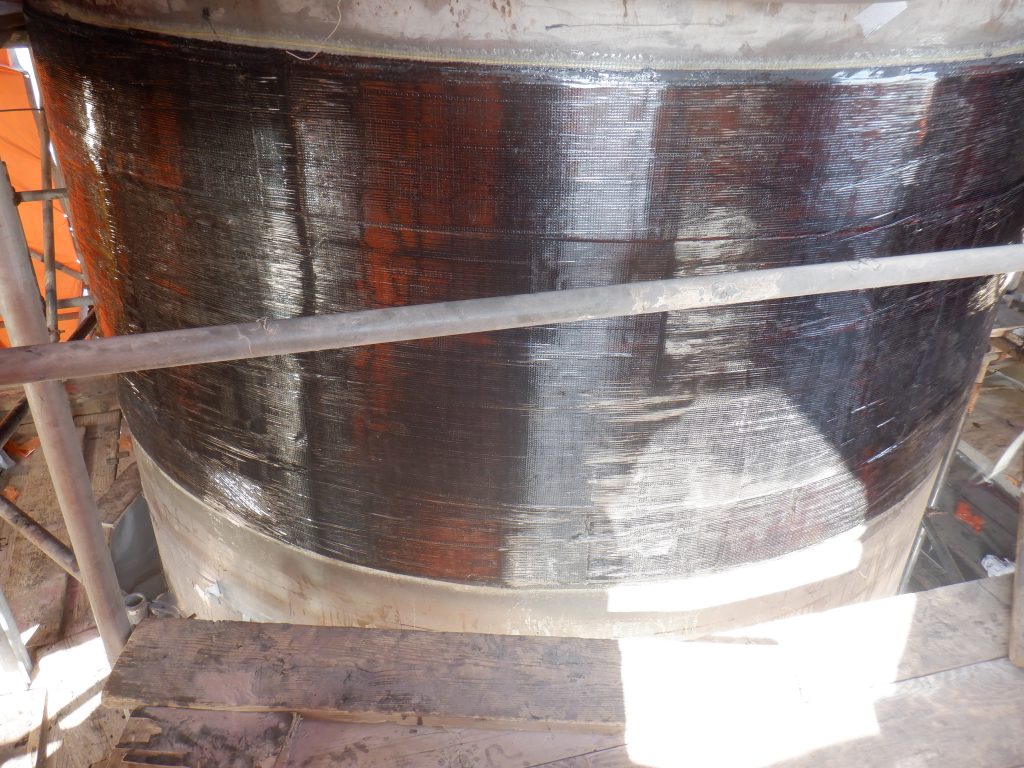
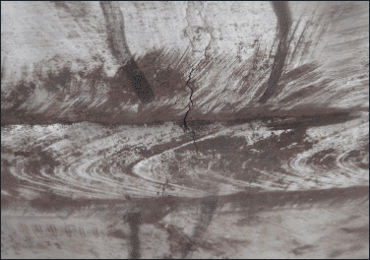
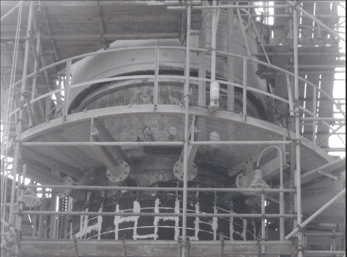
Date: 2017
Client: Major North Sea Operator
Location: UK North Sea
Scope
The stair tower on large North Sea platform was out of use due to heavy corrosion on the structural members. The operator contracted ICR to deliver a cost effective option to re-instate the stairwell to its original design capacity. Phase 1 took place in July 2017 whereby work commenced on the lower section of the stair tower with approx. 80 metres of beams and tubulars being repaired. Phase 2 began in August 2017 to repair the upper section of the stairwell.
Solution
Technowrap™ SRS – ICR’s structural carbon fibre repair system – was recommended to provide added toughness. A low temperature curing resin was used and designed to suit ambient conditions in the North Sea.
Design Temperature | 30°C |
Design Lifetime | 20 years |
Axial Load | 60kN (compression) |
Bending Moment | 6.0kNm (Mxy) / 2.0kNm (Mxz) |
Surface Preparation | Sa2.5 |
The client provided a surface profile of Sa2.5 (grit blasting). Complexity of the scope required maximum efficiency from the onboard fabric maintenance (FM) team and prior to mobilisation, ICR trained the FM crew on the application of gel coating. This was applied within 4 hours of blasting in order to hold the blast and prevent gingering. A team of four ICR technicians worked back to back within a double skin habitat to maintain a suitable environment. Materials were prepped and ready for the next shift to ensure optimum productivity on the job.
Results & Benefits
- The stairwell composite repair is a long term integrity solution which will avoid corrosion in the future and is designed for the remaining life of the asset
- Cost effective solution compared with stairwell replacement
- A quicker solution delivered by multi-skilled technicians which ensured the stairwell was back in use as safely and timely as possible
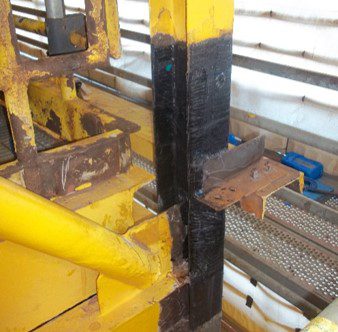
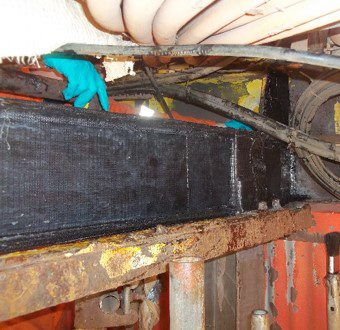
Date: 2015
Client: Major Global Operator
Location: UK North Sea
Scope
A 48” discharge caisson had a large number of through-wall defects over a vertical length of 23 metres that required immediate attention. The scope of the work was to provide an engineered design, with 20 years repair lifetime. This required live leak sealing the numerous through-wall defects and applying both Technowrap™ 2K and Technowrap™ SRS over the defect areas.
Solution
The Technowrap™ 2K and Technowrap™ SRS repair using ICR’s Splashzone™ resin system was installed live.
The combination of the two repair products was a requirement to withstand both the internal pressure plus the axial bending moment resulting from the wave loading. Having successfully overcome all challenges, ICR’s composite engineering team was able to successfully complete the repair of length 23 meters on the 48” caisson. All 40 plus through-wall defects were successfully sealed and the structural integrity of the caisson was reinstated for an extended lifetime of 20 years.
Results & Benefits
- All 40 plus through-wall defects were successfully sealed and the structural integrity of the caisson was reinstated for an extended lifetime of 20 years
- Applying the repair live resulted in zero impact on production and operations to the client and providing an extremely cost effective solution
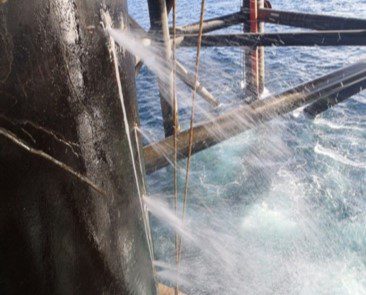
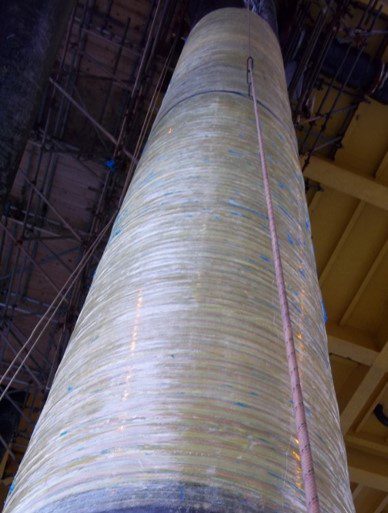
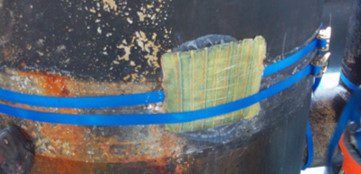
Date: December 2019
Client: Major Operator
Location: North Sea
Scope
Two large laydown areas onboard an operator’s asset offshore in the North Sea were suffering from external corrosion and multiple through wall defects resulting in water ingress. As the roof was classified as a laydown areas and subjected to personnel traffic there was a requirement that the load capacity of the roof was factored into the design. This unique design ensured that the laminate could withstand the applied loads and impacts associated of +5kN/m2.
Solution
ICR provided an engineered design using four layers of Technowrap™ DRS. Combining the properties of the Technowrap™ SRS (Structural Rehabilitation System) carbon fibre and DRS a rubber toughened epoxy resin system. Our integrated approach, providing engineering, materials, technician training and installation, all in-house, has enabled ICR to become an industry specialist. Third party training for the contractor on application and QA/QC procedures was provided and the contractor was subsequently
supervised by a ICR technician.
Results & Benefits
- There were multiple areas with through wall defects and more were to be expected following mechanical surface cleaning preparations
- As a result it was decided that ICR would prefabricate composite plates to cover any through wall defects before the surface preparation commenced
- Following the successful installation of Technowrap™ DRS, the integrity of the roofs was restored for a 10-year defined lifetime
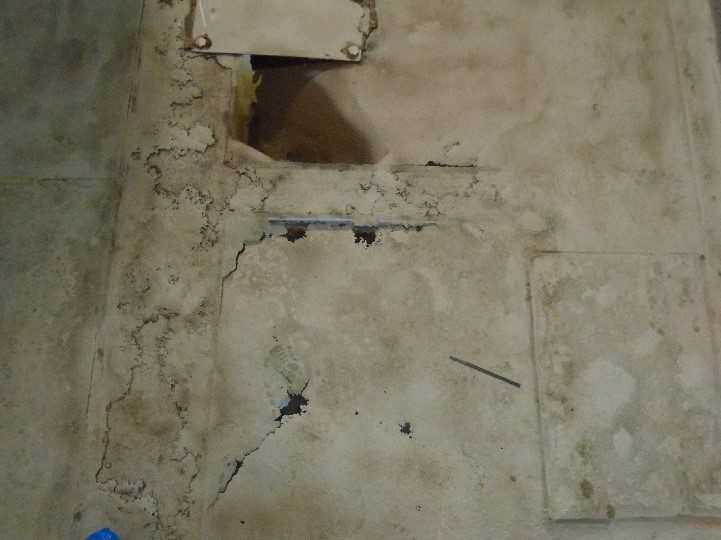
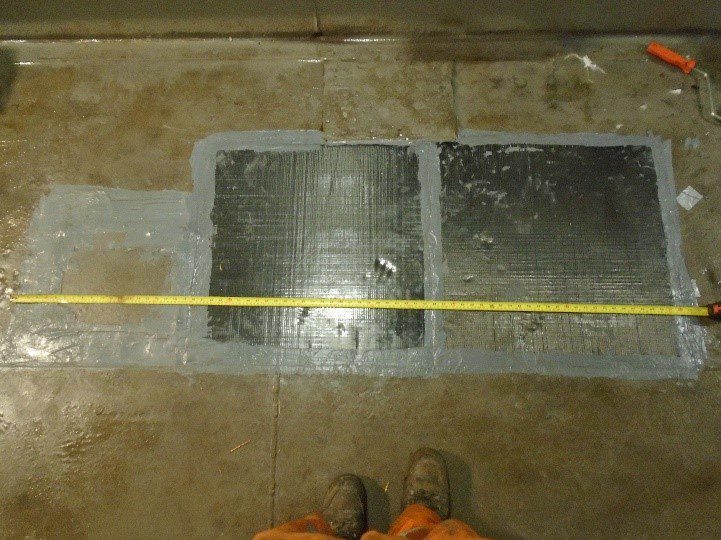
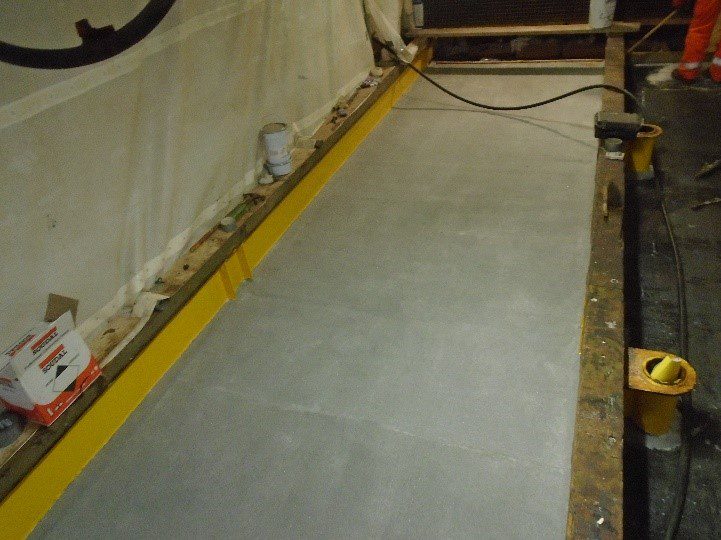
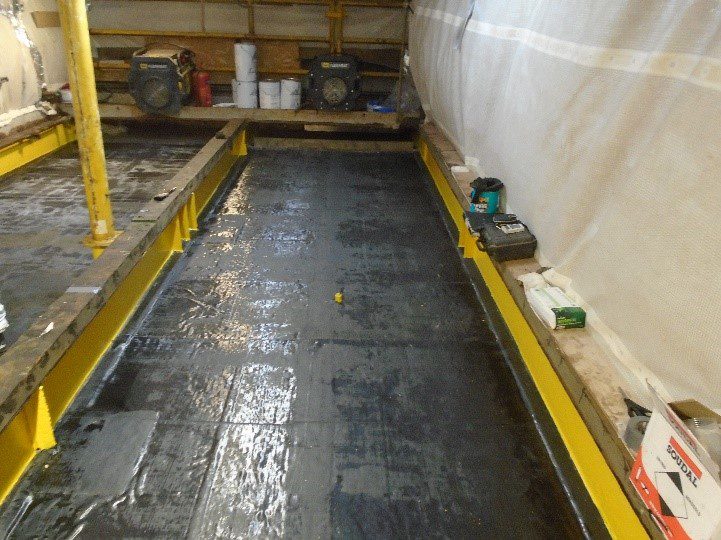
Date: July 2019
Client: Major Operator
Location: Central North Sea
Scope
The pipe deck on the client’s asset had suffered extensive corrosion resulting in severe wall loss and through wall defects. This was the third phase of a 22 bay pipe deck repair. 7 bays measuring 3m x 6m required a repair solution totalling 126m2. Multiple through-wall defects and low wall readings were found.
Solution
The bays were grit blasted to a SA2.5 surface profile. For any areas that were through-wall, 6 layers of our DRS Carbon Fibre solution was utilised. This consisted of a 2 layer composite plate – fully cured – bonded directly over the defects followed by a 4 layer wet lay up. For all non through-wall areas, 4 layers were applied. Fully engineered calculations produced by the ICR technical team.
Results & Benefits
- The repairs were designed to seal all through wall defects as well as providing an engineered design lifetime of 20 years
- The DRS resins provide a rubberised molecule resin which absorbs and dissipates impacts from thoroughfare and use as a landing area
- An anti-slip coating was also applied over the completed pipe deck area. Long term corrosion protection
- No hot work required
- No heavy lifting or steel components
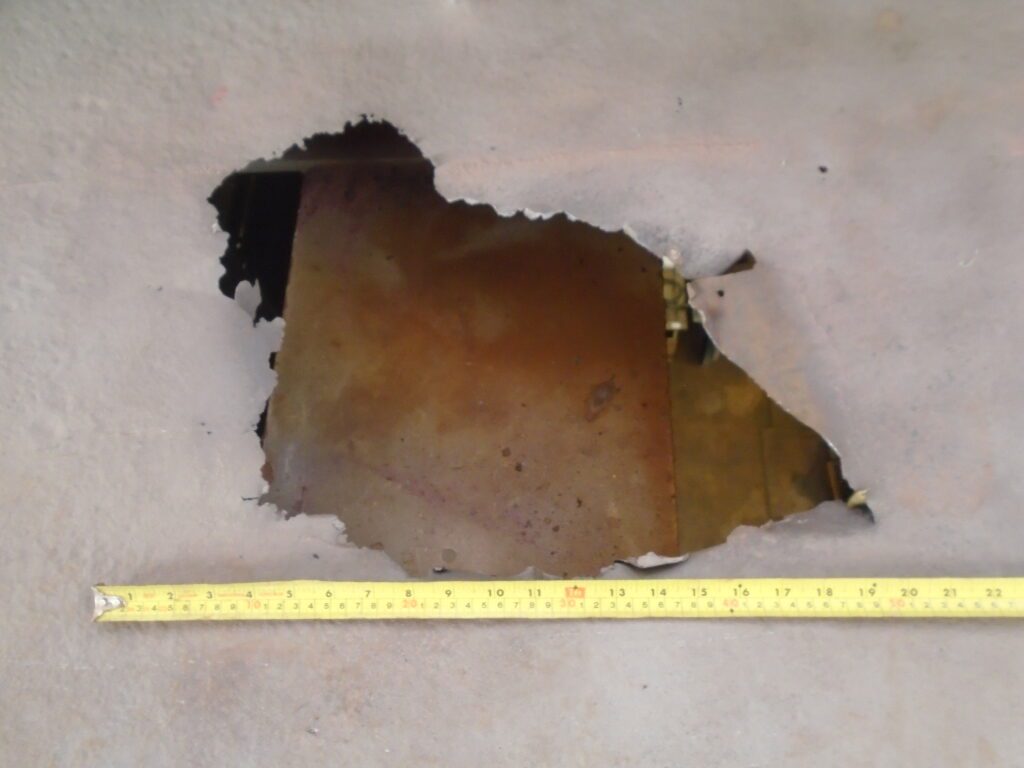
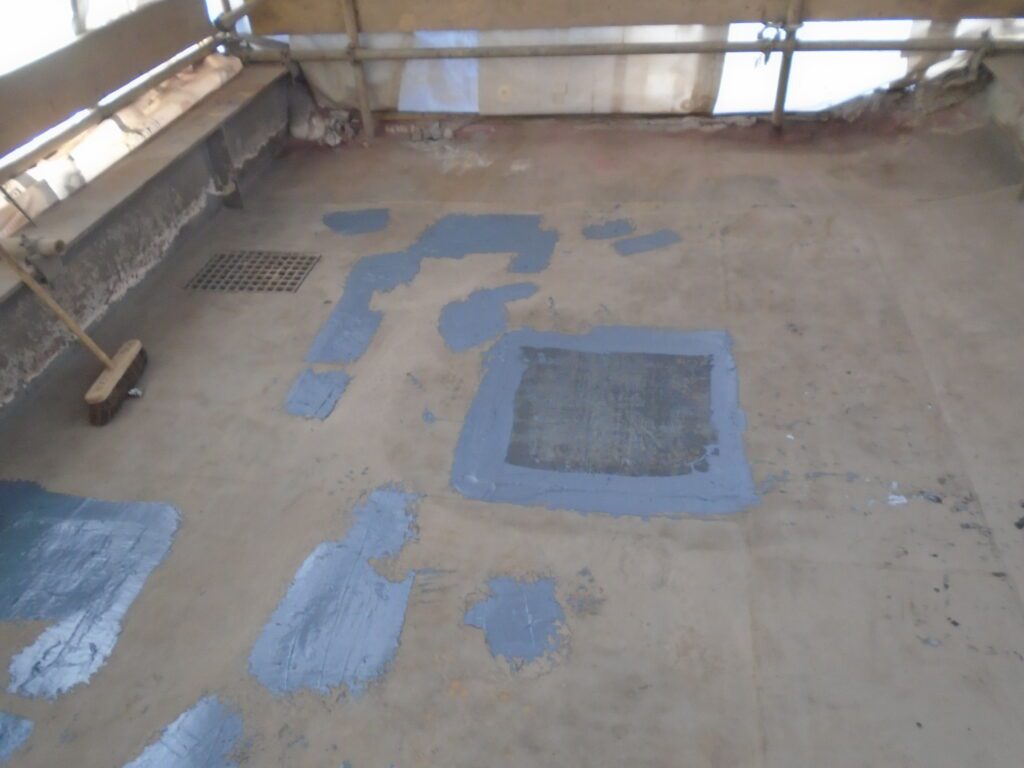
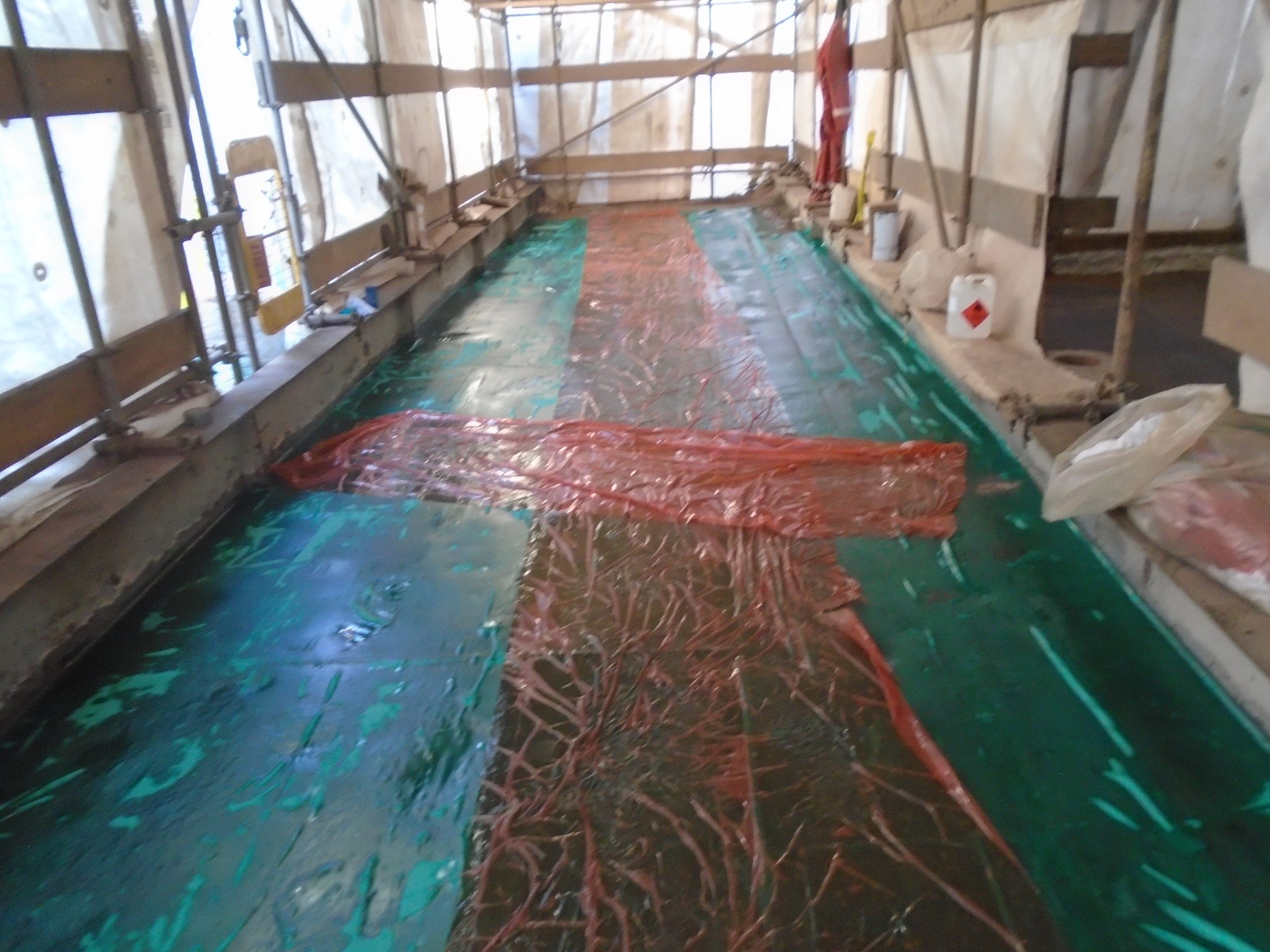
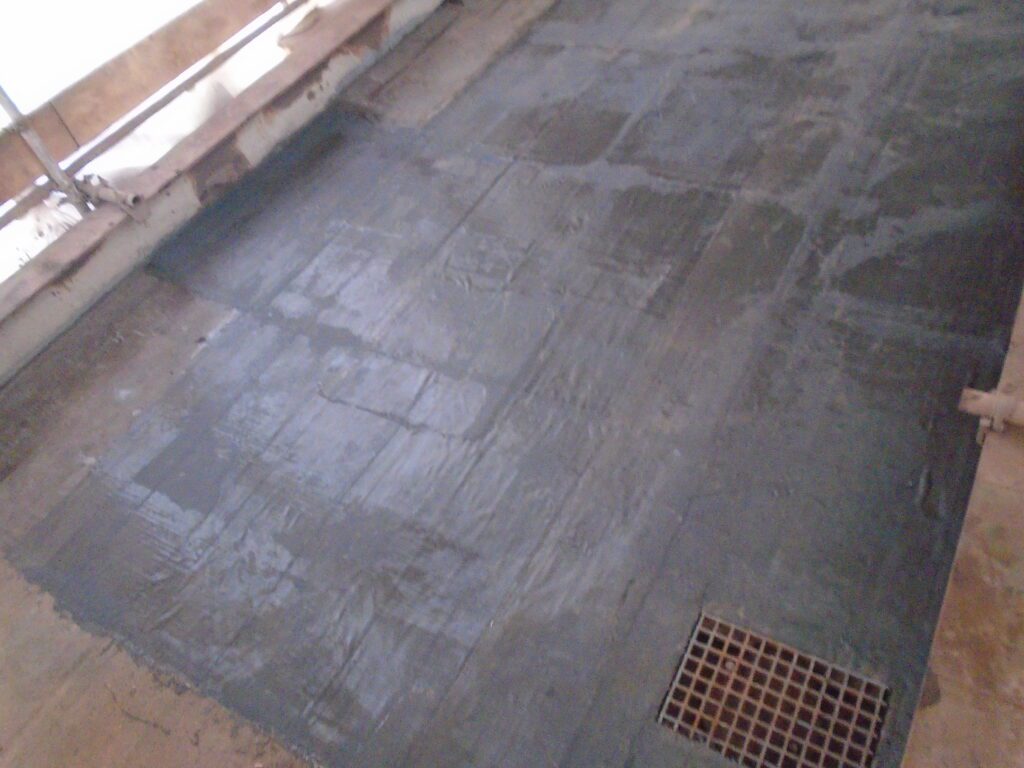