Client Challenge
Our team was tasked with addressing the severely corroded outer cladding of an accommodation module, with various areas identified as needing repair. The challenge included the need for both strengthening the cladding and creating a seal to prevent external environmental ingress.
What We Did
Our scope of work involved the application of a composite repair solution to meet the dual requirements of strengthening and sealing. The chosen design incorporated one layer of Technowrap™ SRS for strength, complemented by a layer of Technocoat for sealing. The application process began with the preparation of the cladding’s outer surface to ST3 standards using grinding discs. The single layer of Technowrap™ SRS was then applied and compressed using rollers, with many repairs conducted off ropes to access various levels and challenging areas. The strategic scheduling of prep work avoided disturbances to personnel, considering specific time constraints, while safety concerns related to high winds and rain during rope access work were diligently managed.
Results and Benefits
The finalised repair, as seen in figure 3, delivered a durable solution for the severely corroded accommodation cladding, ensuring a design lifetime of 20 years. The strategic incorporation of rope access work led to substantial cost savings by obviating the necessity for extensive scaffolding. Beyond fortifying the overall structural integrity, the implemented solution revitalised water-damaged accommodation, contributing to an augmented Platform On Board (P.O.B) capacity. This not only addressed immediate concerns but also relieved pressure on bed space, exemplifying the successful execution of a comprehensive repair that underscored the efficiency of the approved design and application procedure.
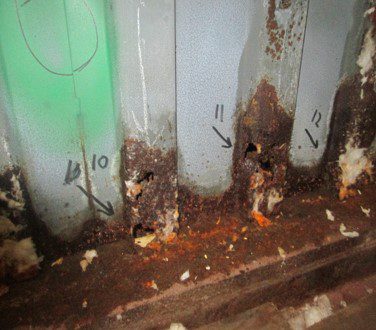
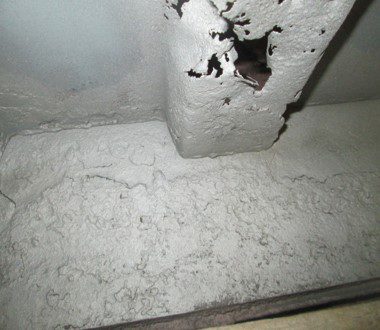
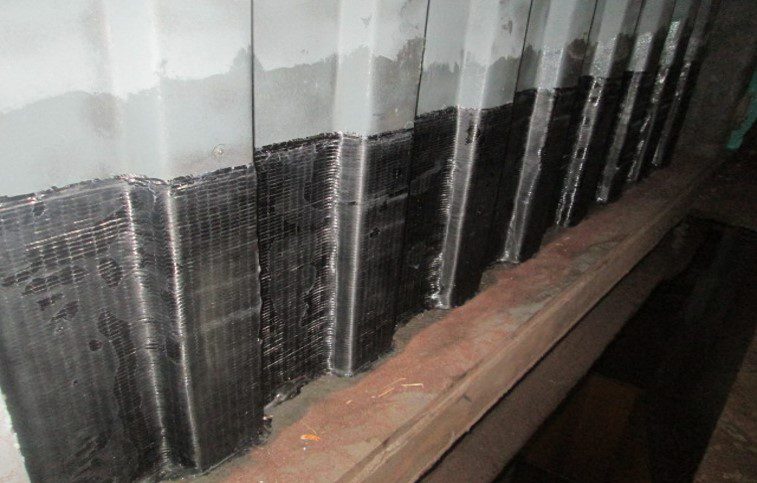
Client Challenge
Sections of a blast wall aboard a North Sea Platform were identified with severe wall loss and through-wall defects attributed to external corrosion. The structural integrity of the blast wall was compromised, necessitating a solution to address the corrosion-related challenges and reinstate its robustness.
What We Did
We provided an engineered design calculation, Technowrap™ SRS materials, and deployed Rope Access trained technicians. The goal was to deliver a fully engineered repair that would effectively restore the integrity of the blast wall. The on-site construction of compression boards was crucial to achieving the required compression levels during the curing process. Following grit blasting, 15 bays, each measuring approximately 2 meters, were profiled using Technowrap™ FP. Subsequently, two layers of Technowrap™ SRS were applied, utilising the Technowrap™ DRS resin system to enhance impact resistance.
Results
The repair of the blast wall on the North Sea Platform yielded significant results and benefits. The application of Technowrap™ SRS not only provided excellent corrosion resistance but also showcased its high strength capabilities, reinforcing the structural integrity of the blast wall. Despite the challenges, including severe wall loss and through-wall defects caused by external corrosion, the engineered design, in accordance with the original parameters, successfully reinstated the wall for an extended 20-year lifespan. The utilisation of Technowrap™ FP for profiling and the application of two layers of Technowrap™ SRS with the Technowrap™ DRS resin system ensured enhanced impact resistance. This comprehensive repair not only addressed immediate concerns but also positioned the blast wall to withstand future challenges, offering long-lasting structural resilience to the North Sea Platform.
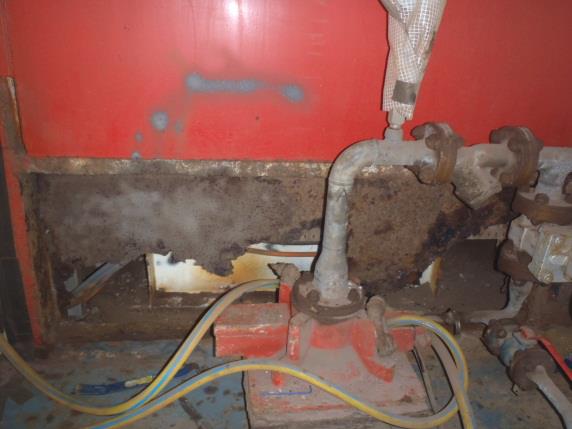
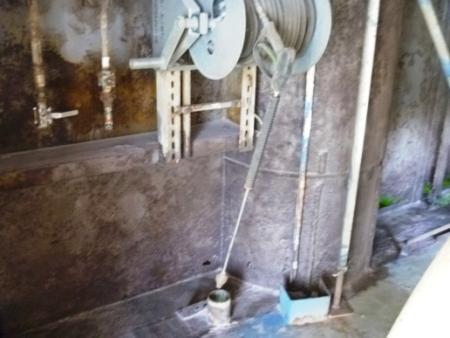
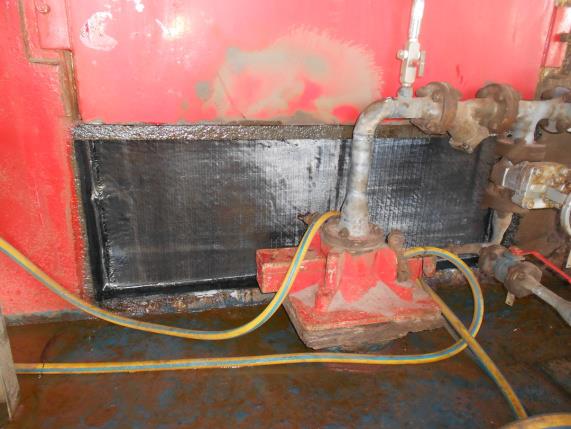
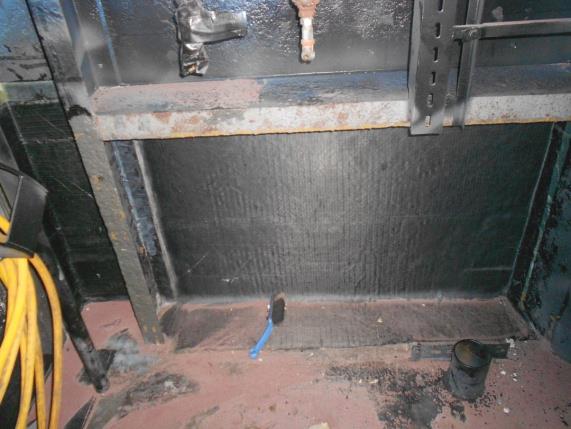
Client Challenge
The Valiant platform faced a critical structural issue as a tubular brace on the cellar deck suffered wall loss due to external corrosion, particularly at the intersection with a vertical column member. The integrity of the brace was compromised, necessitating a permanent repair to ensure its stability and functionality.
What We Did
We undertook a comprehensive scope of work to address the client’s challenge. Our approach involved providing an engineered design calculation for a composite repair capable of withstanding the required loads. Additionally, Technowrap™ trained personnel were deployed to install the engineered repair, utilising the Technowrap™ PRS HP and Technowrap™ SRS composite repair system. The goal was to reinstate the integrity of the affected members.
The repair strategy focused on addressing not only stress levels in the corroded section but also the potential instability of the brace under compressive loads due to reduced stiffness in the corroded area. External factors, such as humidity from GMS Endurance, posed challenges during the repair installation, causing intermittent delays. The design for the 20-year lifetime repair was divided into two parts: Technowrap™ PRS HP applied axially on the diagonal brace and Technowrap Structural™ over the connection between the diagonal brace and the vertical cylindrical member.
Results & Benefits
Despite challenges posed by high humidity, our technicians efficiently utilised downtime by prepping required materials and, with OIM permission, worked overtime to ensure timely completion. The Technowrap™ composite repair was successfully installed, restoring the integrity of the tubular brace with a design lifetime of 20 years. The repair not only addressed the immediate concerns but also provided long-term structural reliability.
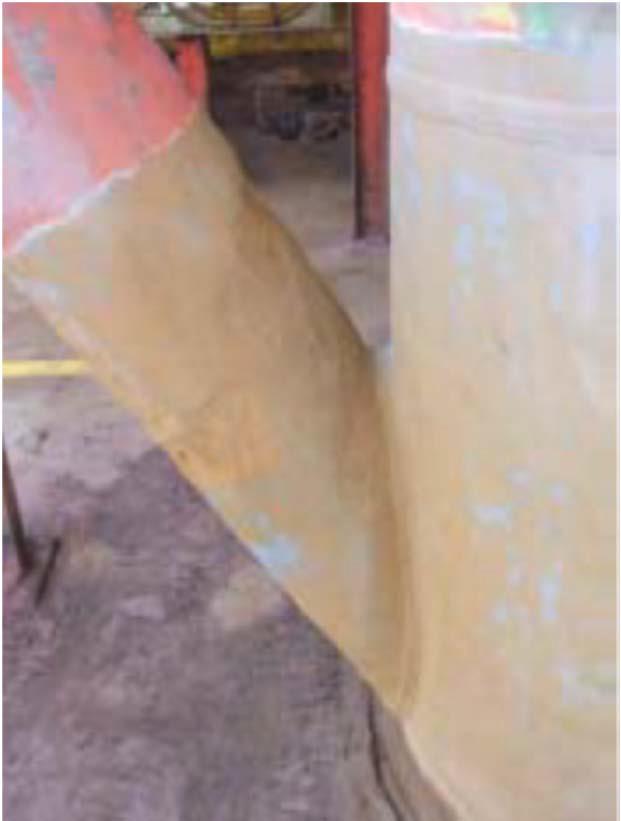
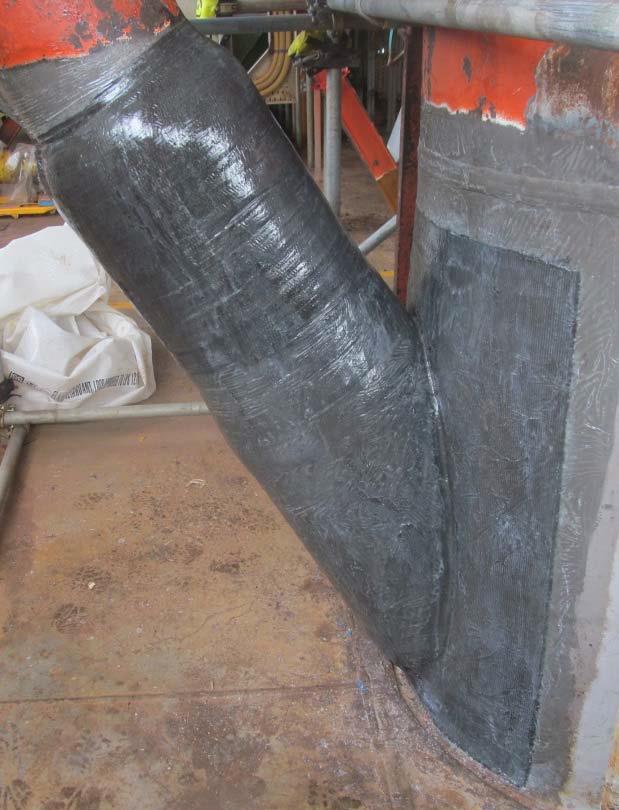
Client Challenge
A North Sea platform faced a challenge requiring the upgrade of their GRP pipework sea water system. The project involved the replacement and installation of multiple GRP pipe spools, each with varying design conditions, including pressures up to 16 bar and temperatures up to 93ºC. In addition, our client required a 20-year lifetime design.
What We Did
Our team carried out a comprehensive scope of work which included providing the necessary materials and deploying trained personnel for the fabrication and installation of the GRP pipework. Recognising the unique challenges posed by the project, we organised a specialised team capable of working on-site to fabricate and bond the pipe spools with minimal disruption to the platform.
The planning, fabrication, and installation phases were executed seamlessly, thanks to daily coordination and a dedicated team committed to meeting our client’s expectations.
The GRP pipe spools underwent construction, inspection, and release by a third party at ICR’s premises. Subsequently, the spools were transported offshore and installed by ICR technicians, who performed butt and wrap joints in situ. The establishment of a dedicated team and ongoing communication with the client played pivotal roles in the successful completion of this unique scope.
Results & Benefits
The project demonstrated remarkable success on multiple fronts. Firstly, the completion of the project without the requirement for hot work stands as a significant achievement, effectively minimising safety risks associated with such activities. Additionally, the implemented solution proved to be not only efficient but also highly cost-effective. Meeting the stringent criteria set by the client, the project successfully attained the 20-year design life requirement, ensuring long-term reliability. The undeniable success of the endeavor has not only met but exceeded client expectations, leading to an increased interest in ICR’s services, as evidenced by additional inquiries for broader scopes of work. This positive outcome underscores the client’s satisfaction and trust in ICR’s capabilities.
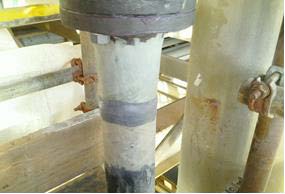
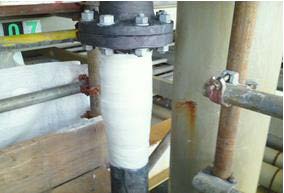
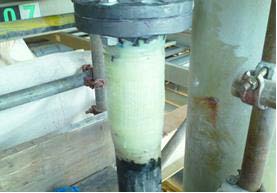
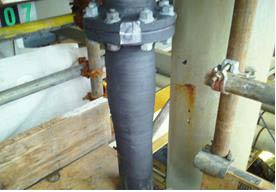
Client Challenge
A North Sea platform faced a critical issue with its turbine hall roof, as water ingress was reported due to the corrosion of a previously fitted and edge-welded steel plate. This corrosion allowed water to penetrate, posing a threat to the turbine hall below.
What We Did
We were tasked with providing a comprehensive solution to seal the roof and prevent further fluid ingress. The scope of our work involved devising an engineered design system utilising Technowrap™ DRS. This encompassed design calculations, selection of materials, and the installation process conducted by our trained personnel. The primary goal was to reinstate the integrity of the turbine hall roof.
Results and Benefits
Despite challenging weather conditions, successful weatherproofing enabled us to achieve the desired repair properties.
Overcoming the obstacle of turbines running below the repair area with a steel temperature of 65ºC was addressed by implementing a temporary shutdown.
Thorough surface preparation to Sa2.5, including grit blasting, ensured optimal adhesion for the two-layer Technowrap™ DRS repair system. To enhance safety, an orange nonslip paint was applied to the turbine roof post-repair.
The Technowrap™ DRS installation successfully restored the turbine roof’s integrity, ensuring a projected lifetime of 20 years.
The entire scope was delivered without any incidents, meeting and exceeding client expectations.
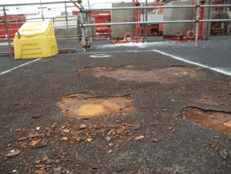
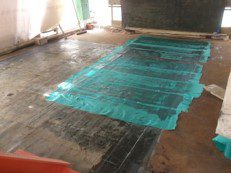
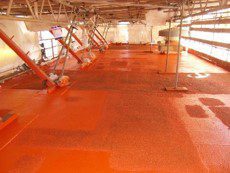
Client Challenge
Our client, a global mining company based in Western Australia, faced a significant challenge with their coastal jetty piles. The structural steel piles exhibited extensive corrosion which drastically reduced their capacity and rendered the coastal jetty unusable for shipping mined products. In addition, the piles were coated with asbestos-containing material which required safe removal in order for adequate surface preparation for composite repairs. Furthermore, because of the coastal location, this presented significant challenges in terms of negotiating the tides and safely accessing the site.
What We Did
To effectively address our client’s challenges, we implemented a comprehensive strategy which involved carrying out the following processes:
Safe Asbestos Coating Removal
We prioritised the safe removal of the asbestos-containing coating to ensure a secure environment for subsequent repairs.
Advanced Engineering Calculations
Utilising advanced engineering calculations, we minimised the surface preparation area required for composite repairs, optimising efficiency and reducing risks associated with asbestos exposure.
Rope Access Technicians
Overcoming access challenges posed by the coastal location, we deployed highly skilled rope access technicians working from suspended platforms. This approach ensured precise execution of repairs even in challenging conditions.
Results
Our intervention yielded impressive results for the client by developing an innovative structural pile repair design methodology, specifically tailored to address the challenges posed by corroded piles. By leveraging advanced engineering calculations, we minimised the surface preparation area which reduced the risks associated with asbestos and enhanced overall project efficiency.
Our approach facilitated efficient repairs in areas with complicated geometry, ensuring seamless restoration of structural integrity. Beyond structural rehabilitation, our solution included comprehensive corrosion protection which distinguished it from traditional welded repairs that may remain susceptible to future corrosion. Additionally, our repairs successfully minimised the dead weight on the piles which helps to enhance structural stability and longevity.
In summary, our holistic approach not only addressed immediate structural challenges but also provided a sustainable and robust solution, ensuring the prolonged integrity of the coastal jetty piles.
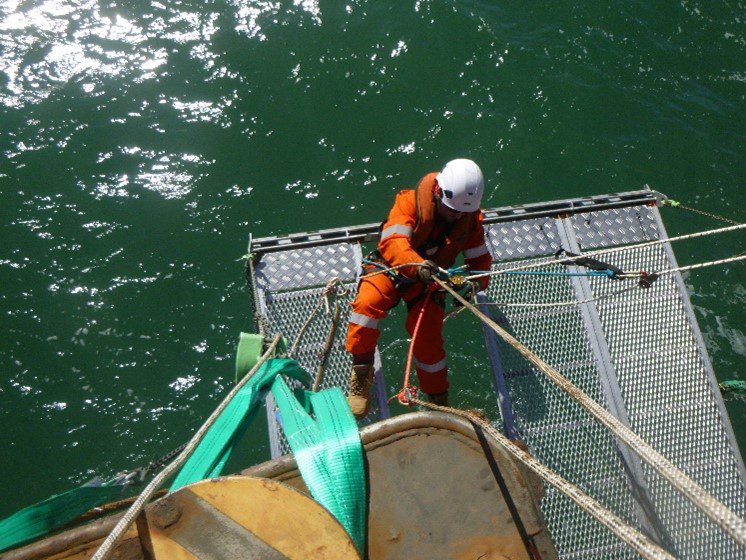
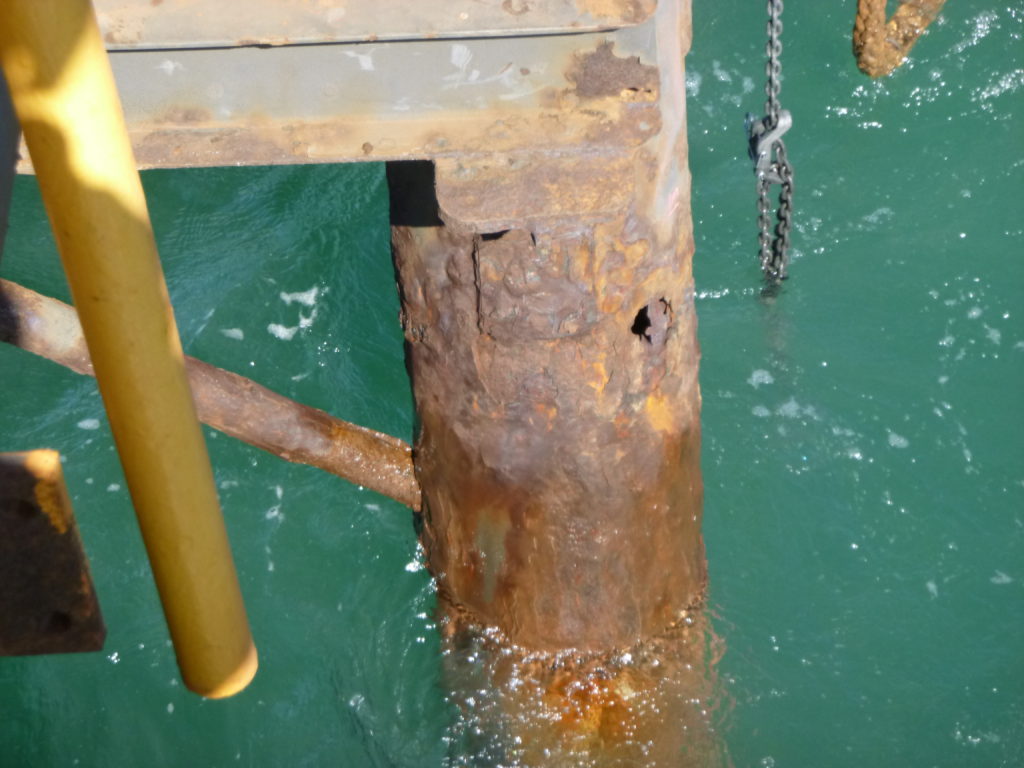
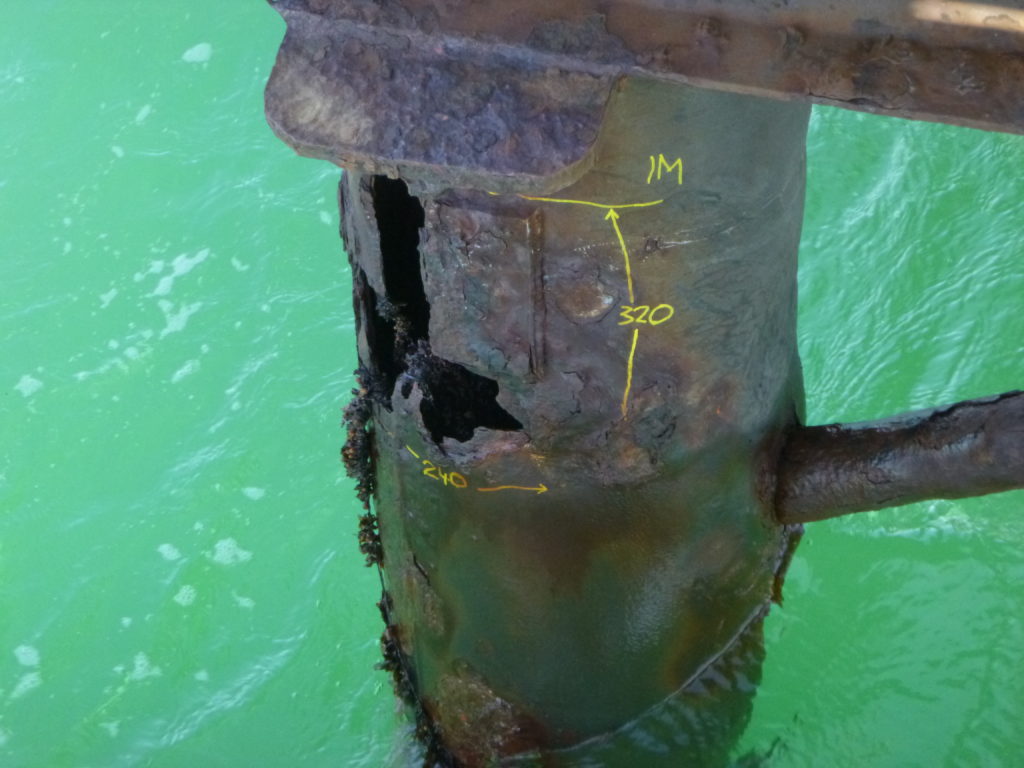
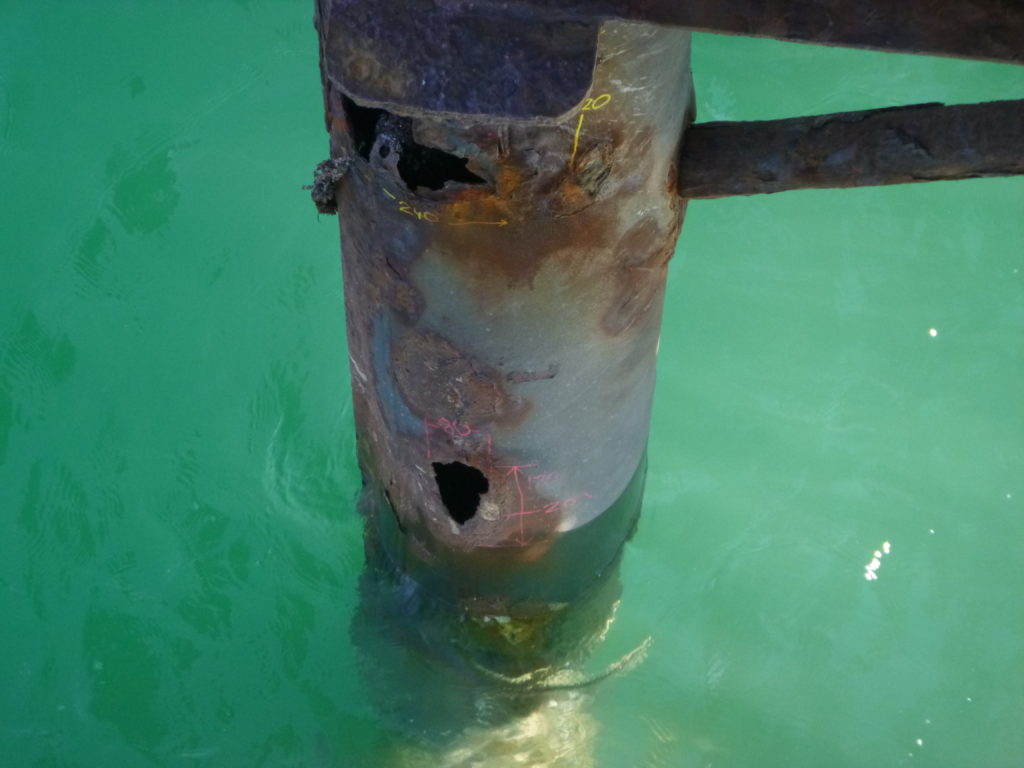
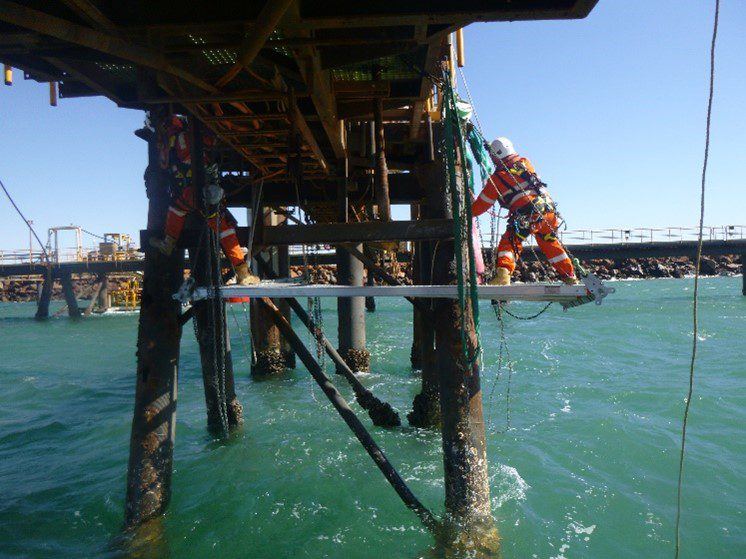
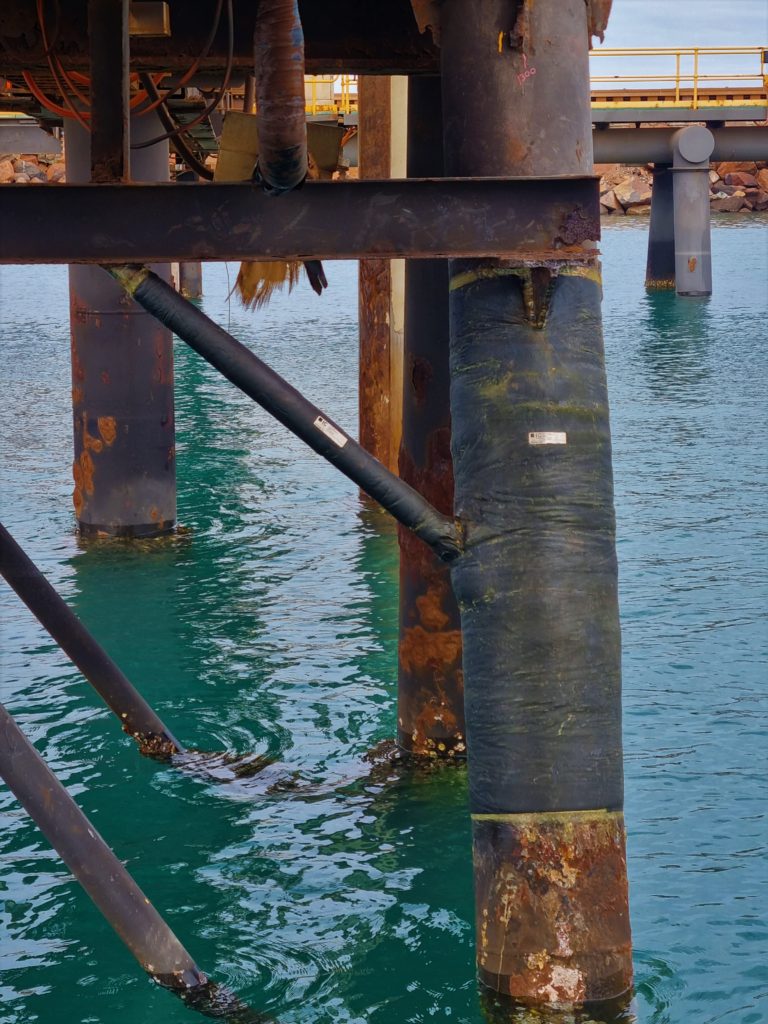
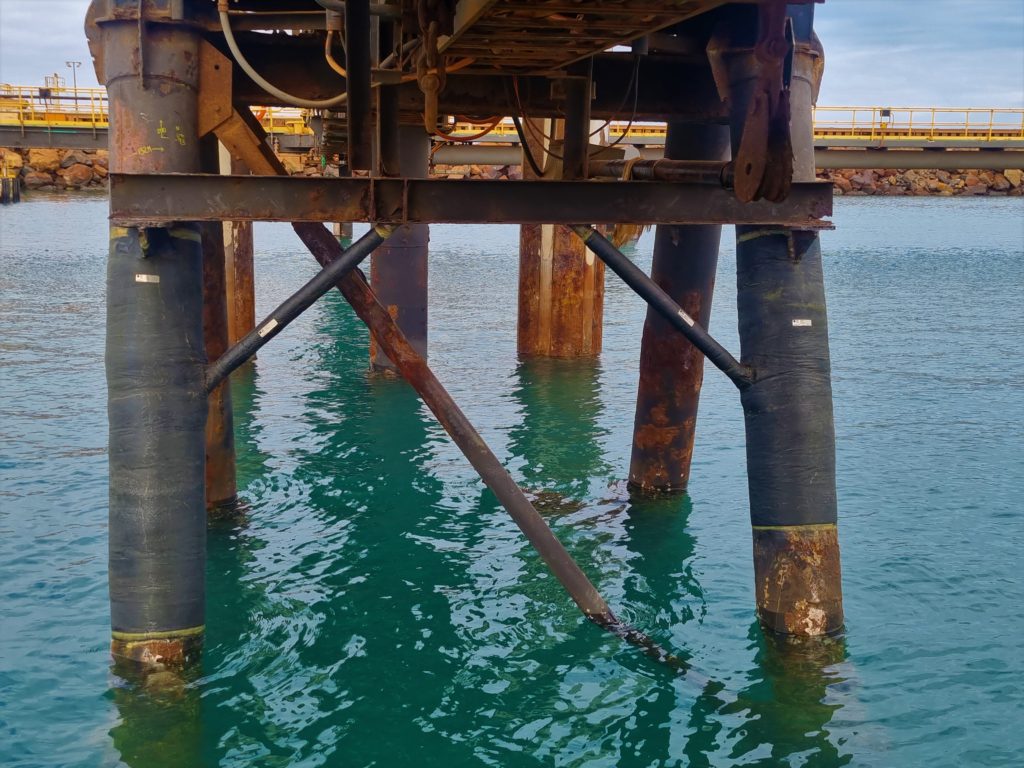
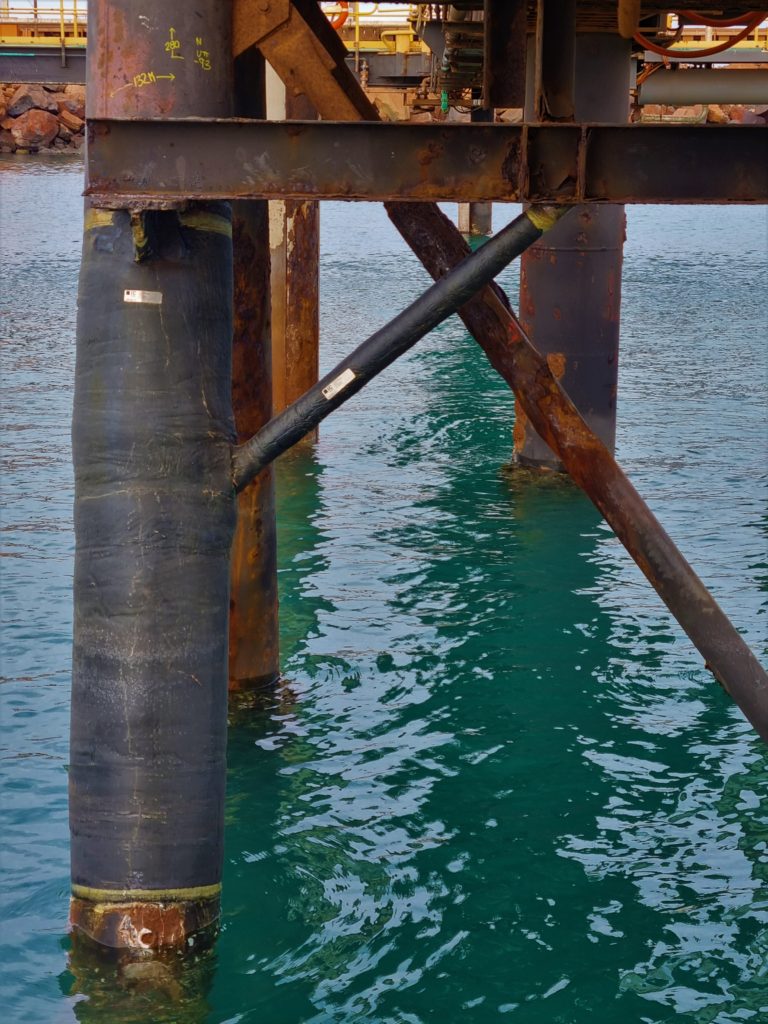
Client Challenge
Our client, a major North Sea operator, faced a critical issue onboard one of their assets: a plenum chamber floor suffering from severe external corrosion. The corrosion buildup posed a threat of plate failure, with numerous areas developing through holes. Urgent action was needed to address the 36m² area requiring repair and prevent further deterioration.
What We Did
To tackle this challenge, we implemented an advanced engineered repair system. This comprehensive solution included precise design calculations and the installation of Technowrap™ DRS repair materials. Our skilled personnel, along with the materials, were deployed to reinstate the integrity of the affected floor areas. To mitigate concerns about potential turbine damage from loose grit, a final protective measure involved applying a thick coat of Technowrap™ DRS resin for a complete seal.
Results & Benefits
The application of Technowrap™ DRS proceeded smoothly, without delays, ensuring a timely repair for our major North Sea operator.
As an additional safety measure, an anti-slip coating was applied across the entire floor area, enhancing workplace safety.
The successful installation of Technowrap™ DRS effectively restored the integrity of the plenum chamber floor, providing long-lasting benefits and preventing further deterioration.
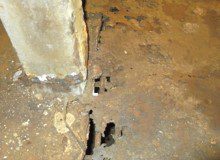


Client Challenge
A major energy operator in the Norway North Sea faced a significant issue with excessive corrosion which had led to several through-wall defects in a crucial 14” helideck drain line on their platform. The client sought a solution to repair and seal these defects, with the primary goal being a durable fix lasting at least 20 years.
What We Did
Our team addressed the challenge by implementing an engineered composite repair using the Technowrap 2K™ resin system. The design of the repair solution adhered to the rigorous standards outlined in ISO 24817.
Results & Benefits
The application of 8 layers of Technowrap 2K™ successfully restored the integrity of the pipework, ensuring a robust repair that is projected to last for an impressive 20 years.
This solution not only resolved the immediate issue but also provided long-term benefits, showcasing the effectiveness and reliability of our engineered composite repair approach.
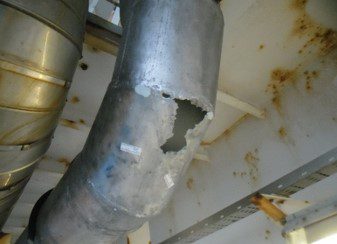
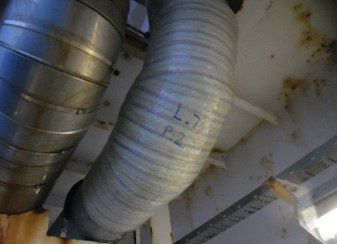
Client Challenge
Three waste heat recovery unit roofs faced extensive external corrosion, leading to through-wall penetration in some areas and wall thinning in others. Our client needed a solution that would effectively reinstate the integrity and reinforce these roof sections, aiming for a 20-year repair lifetime. The challenge was compounded by the operating temperature of 220°C, requiring a repair method that could withstand the relevant loads and operate efficiently at elevated temperatures.
What We Did
We provided an engineered design for a 20-year repair lifetime, deploying Technowrap™ trained personnel, and utilizing Technowrap™ SRS HT carbon fiber materials for the repair. Given the severity of corrosion and the client’s preference to avoid grit blasting, ST3 Mechanical Preparation and ST2 hand preparation were used to achieve suitable surface finishes for bonding without causing further damage. To address the more severe corrosion than initially anticipated, wire mesh fillers were implemented and cured before the installation of the engineered Technowrap™ repairs. The operating temperature necessitated a temporary reduction to facilitate repair installation, with the heat from the units aiding in the curing process and reducing installation time.
Results & Benefits
Technowrap™ Structural Strengthening carbon fiber was meticulously applied using the hand lay-up technique, ensuring precise sizing of repairs and incorporating a slight taper at the edge of the panels.
The repairs were executed seamlessly while the units remained live, eliminating the need for isolation or shutdown, thereby preventing any loss of operation or production. The successful application of Technowrap™ SRS HT showcased its adaptability to high-temperature environments, offering a durable solution for waste heat recovery unit roofs.
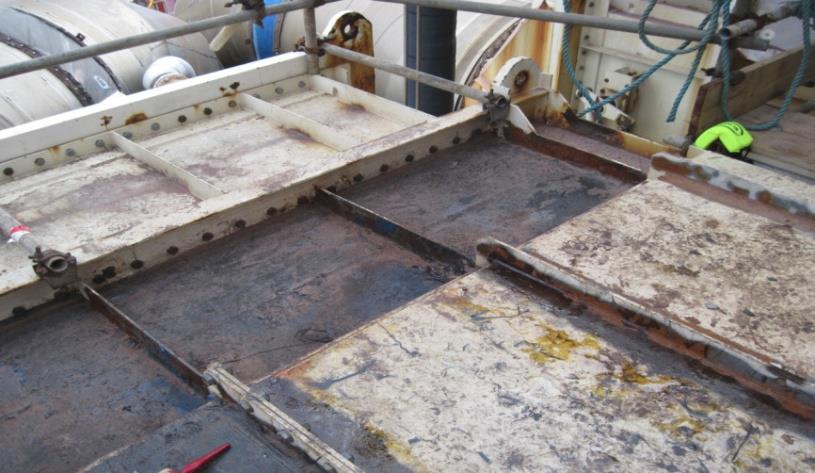
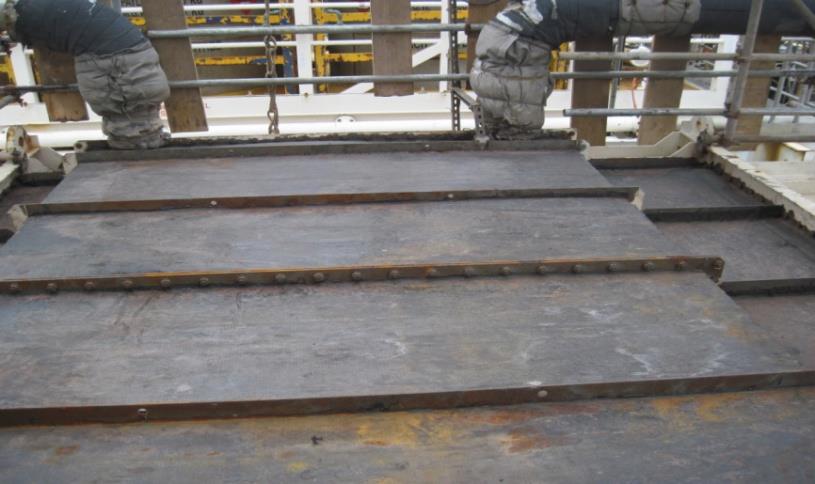
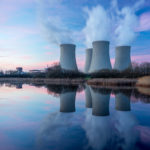
Date: April 2018
Location: Middle East
Client challenge
A 30” Crude Oil Pipeline, located in the Middle East had previously suffered a through-wall defect. Initially, a clamp had been employed as the preferred repair method; however, this approach had proven ineffective and was actively leaking. The urgent task at hand was to provide a solution to repair the leaking clamp while the pipeline remained in operation and the leak persisted.
What we did
We leveraged our innovative composite repair technology, Technowrap™ 2K fibreglass cloth with HA (High Ambient) resins to repair the defect. We began by creating a sump, with a large threaded nut strategically positioned in the center of the cured composite cloth and maneuvered into place beneath the pipework. Ratchet straps were employed to secure the threaded nut in position. Once the initial repair around the nut was fully cured, layers were meticulously applied around the threaded nut, with the leak actively exiting at this point. Subsequently, a bolt was screwed into the thread, and the necessary number of layers was applied over the bolted area of the sump to secure and seal the repair effectively.
Results
The repair solution was successfully applied while the pipeline remained live, resulting in no downtime and zero impact on production and operational activities. This case study underscores our ability to provide swift and effective solutions, even under challenging circumstances, ensuring the seamless restoration of critical infrastructure without interrupting vital operations and production processes.
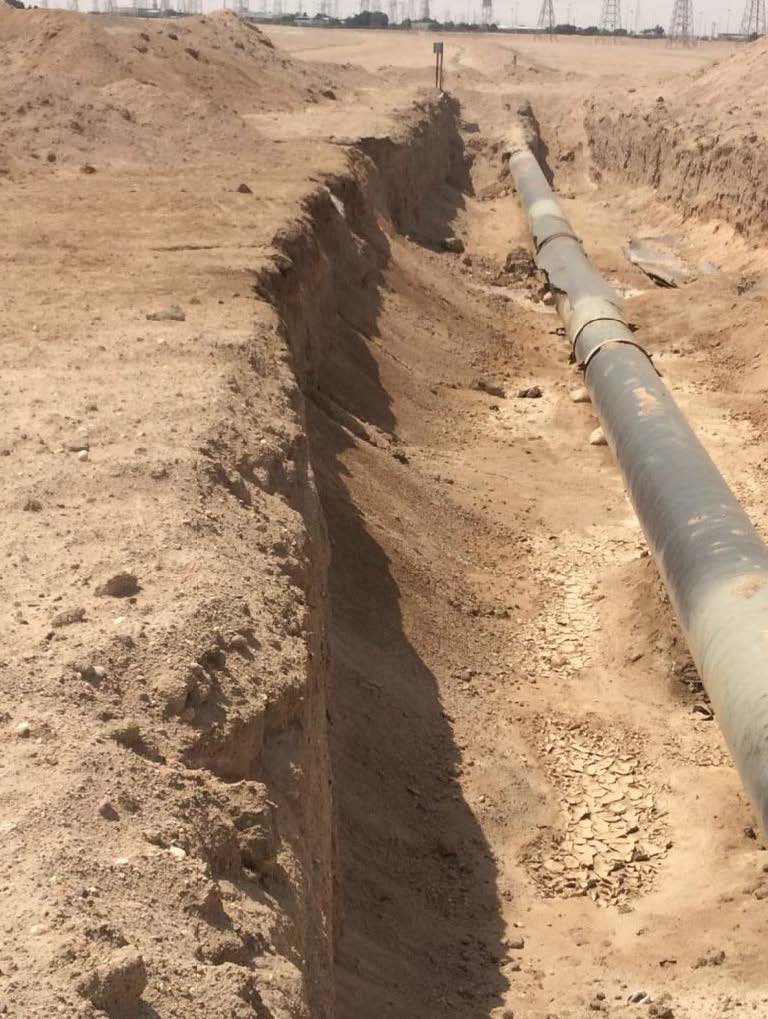
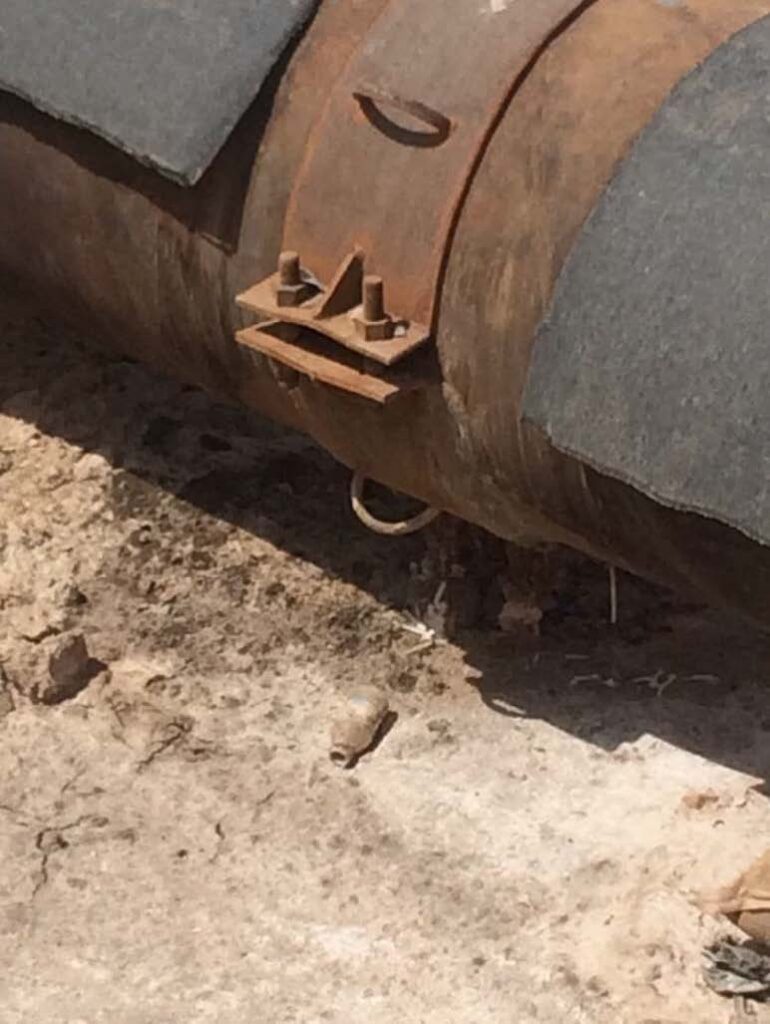
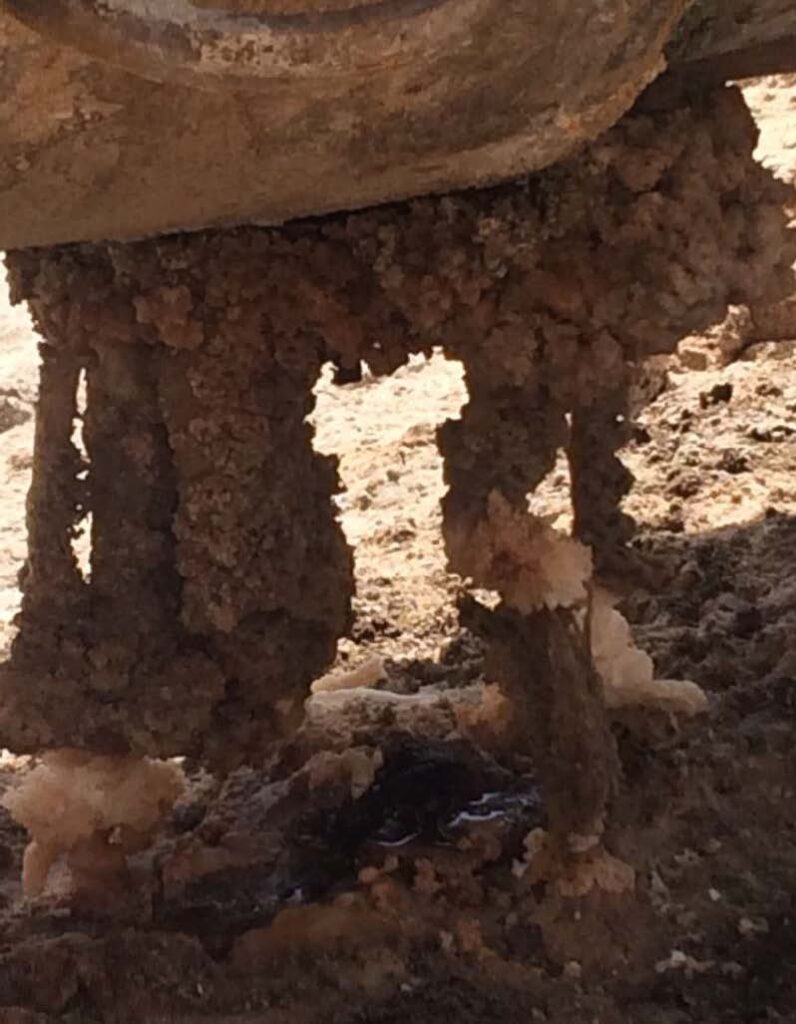
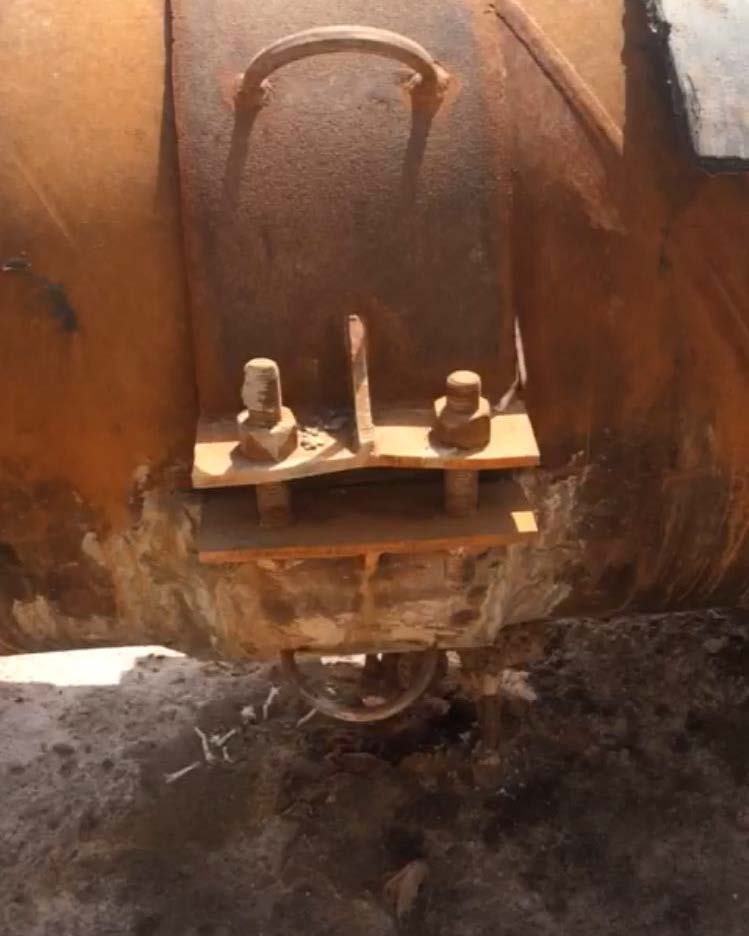
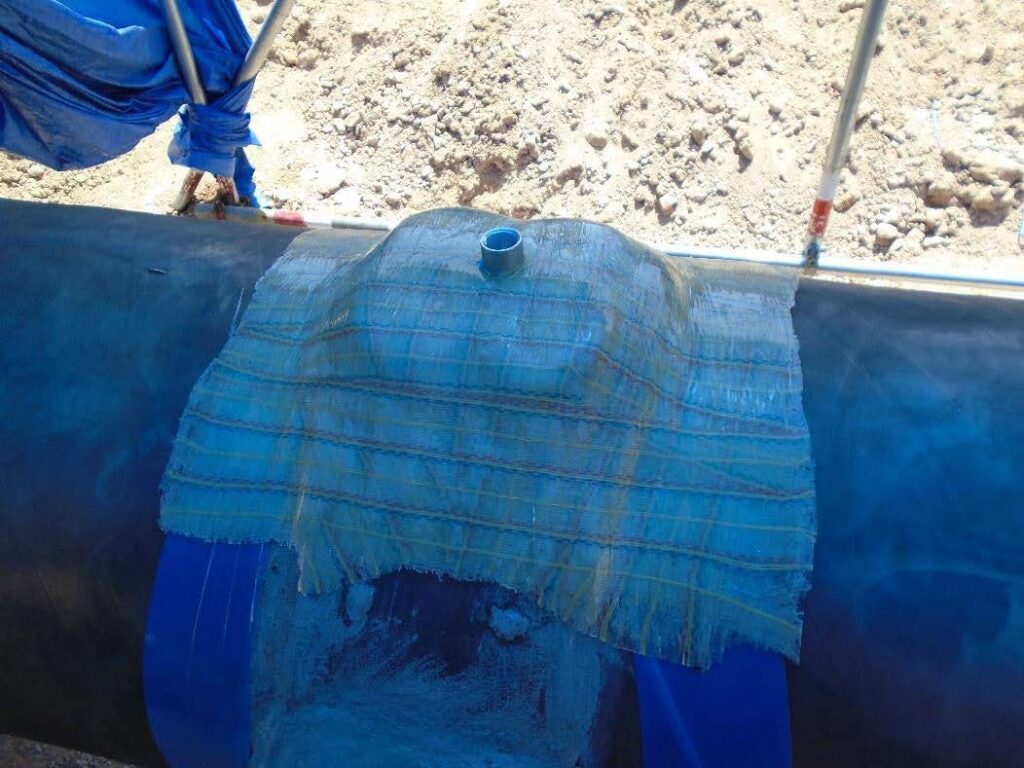
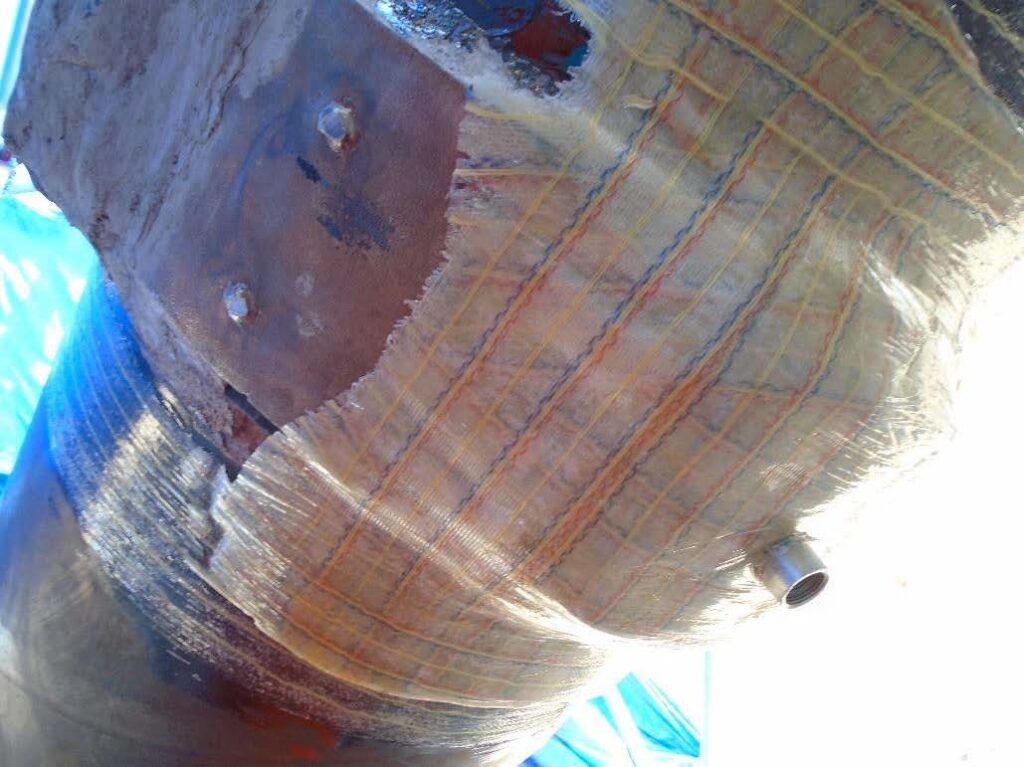
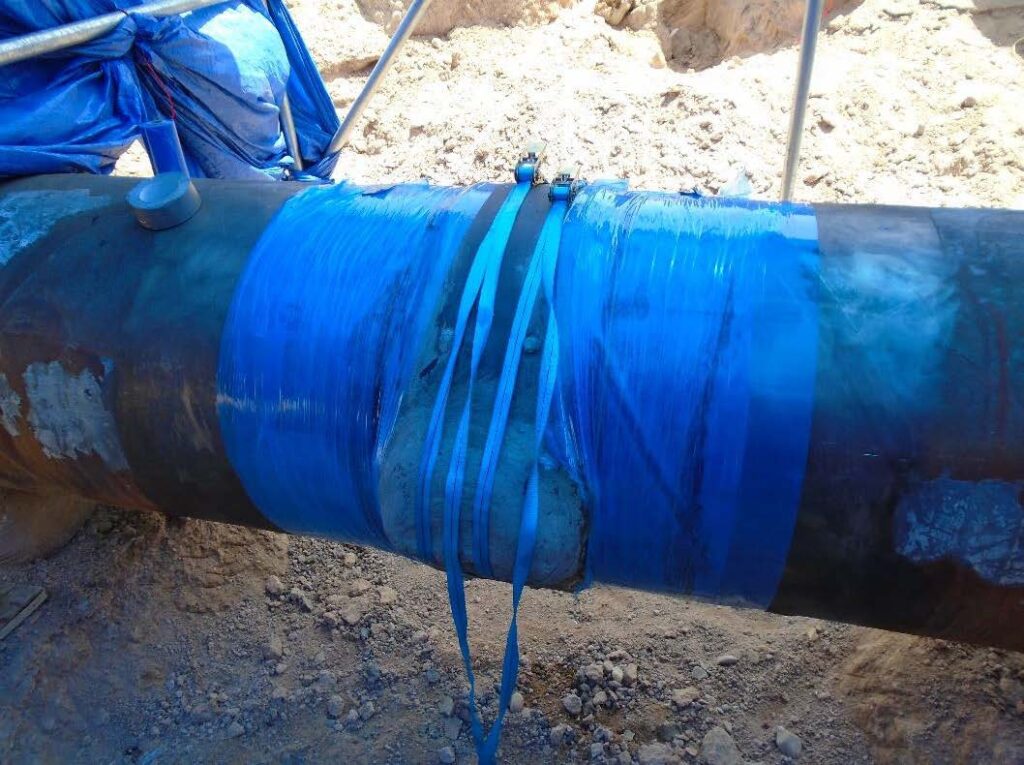
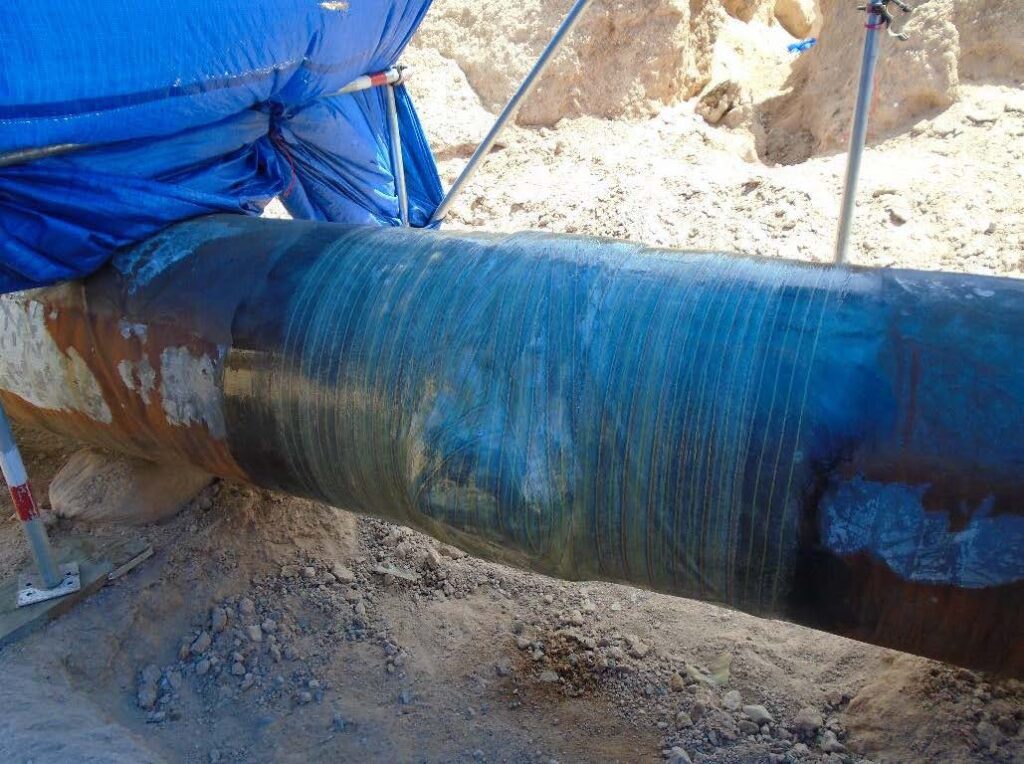
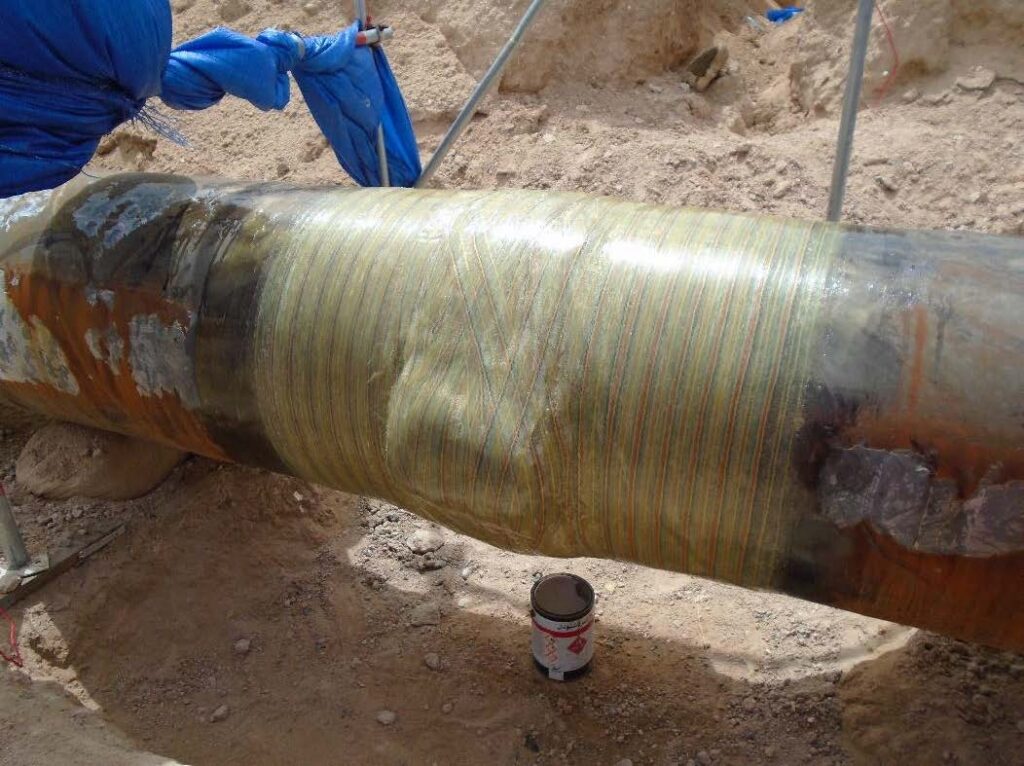
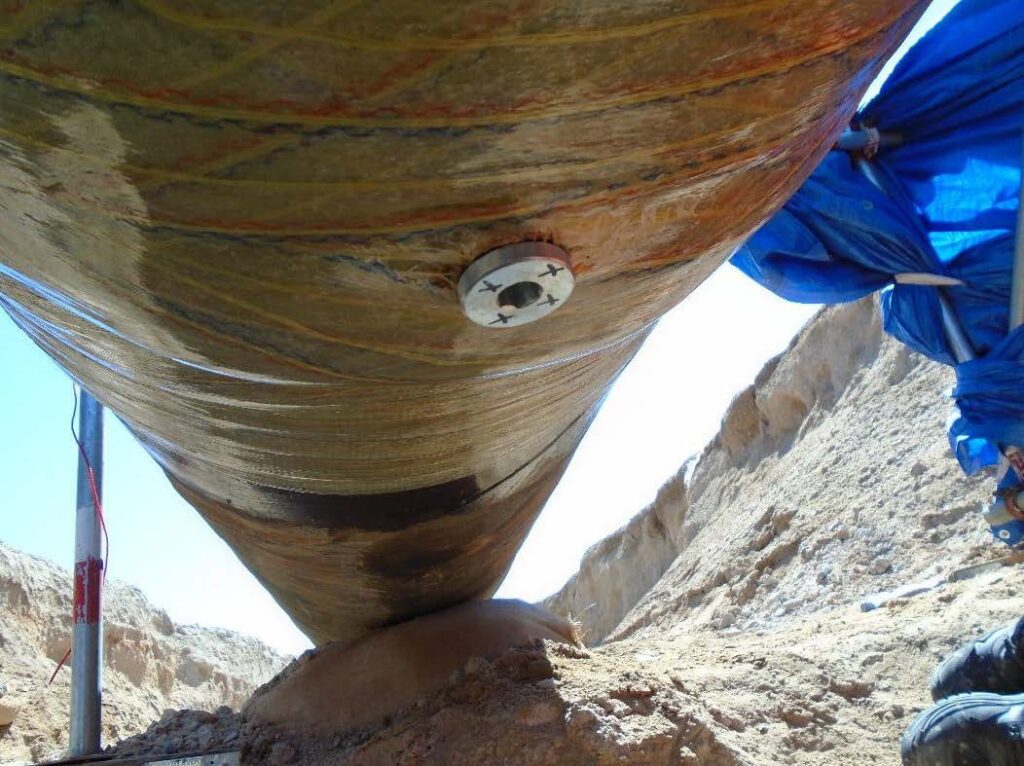
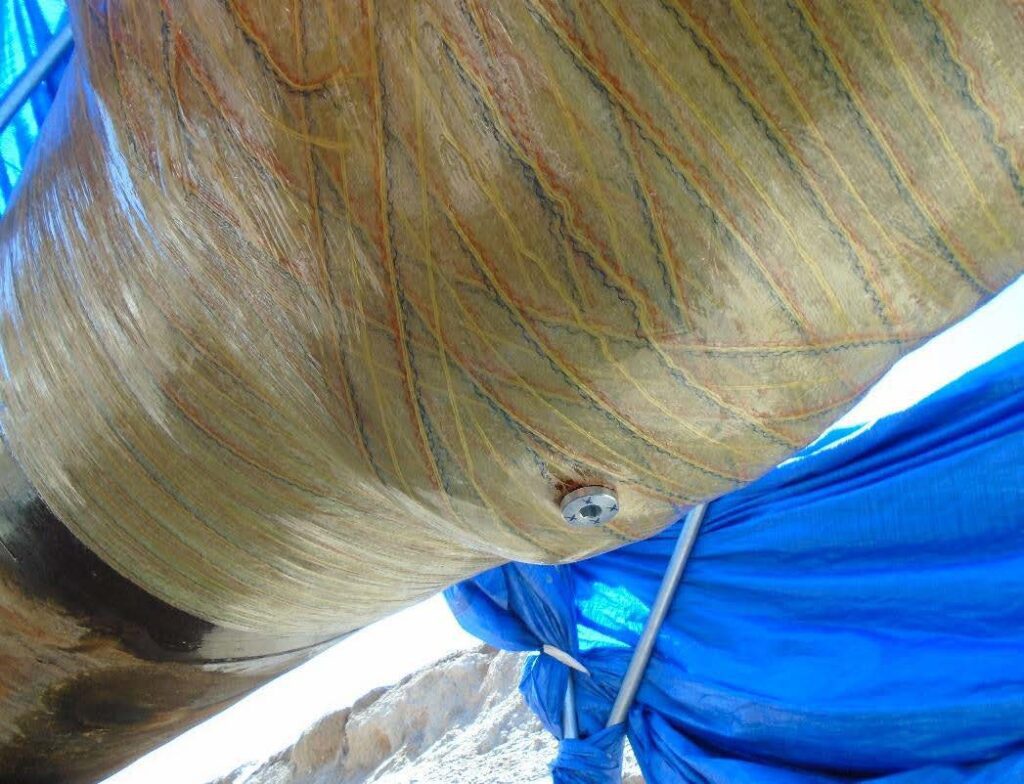
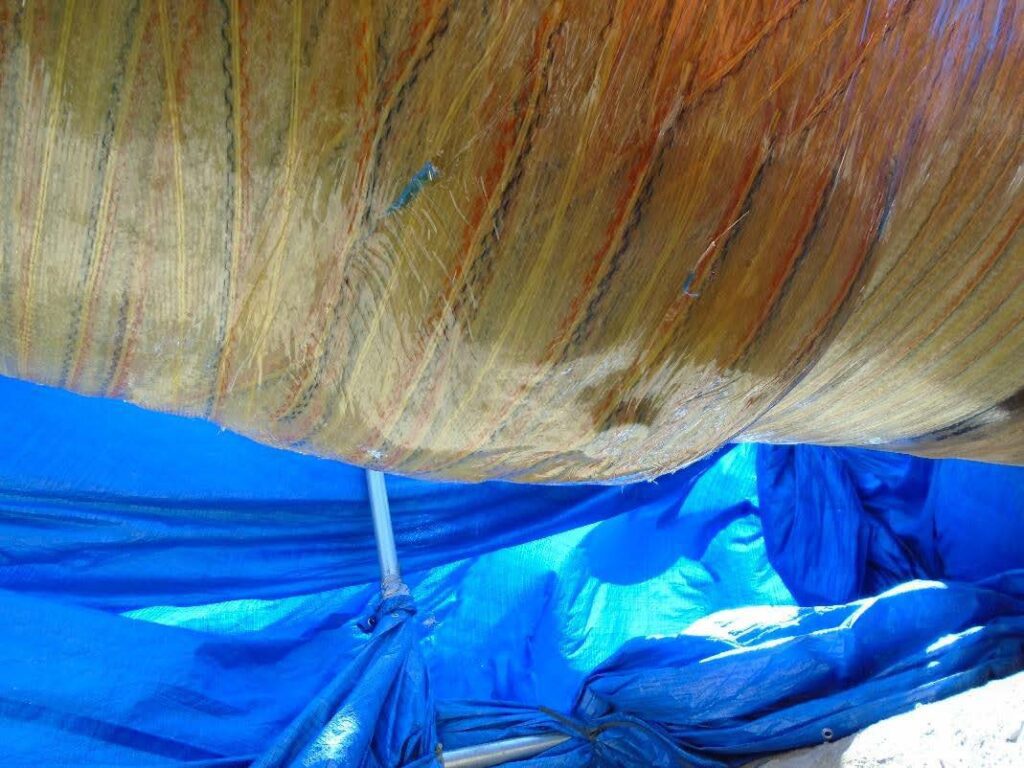
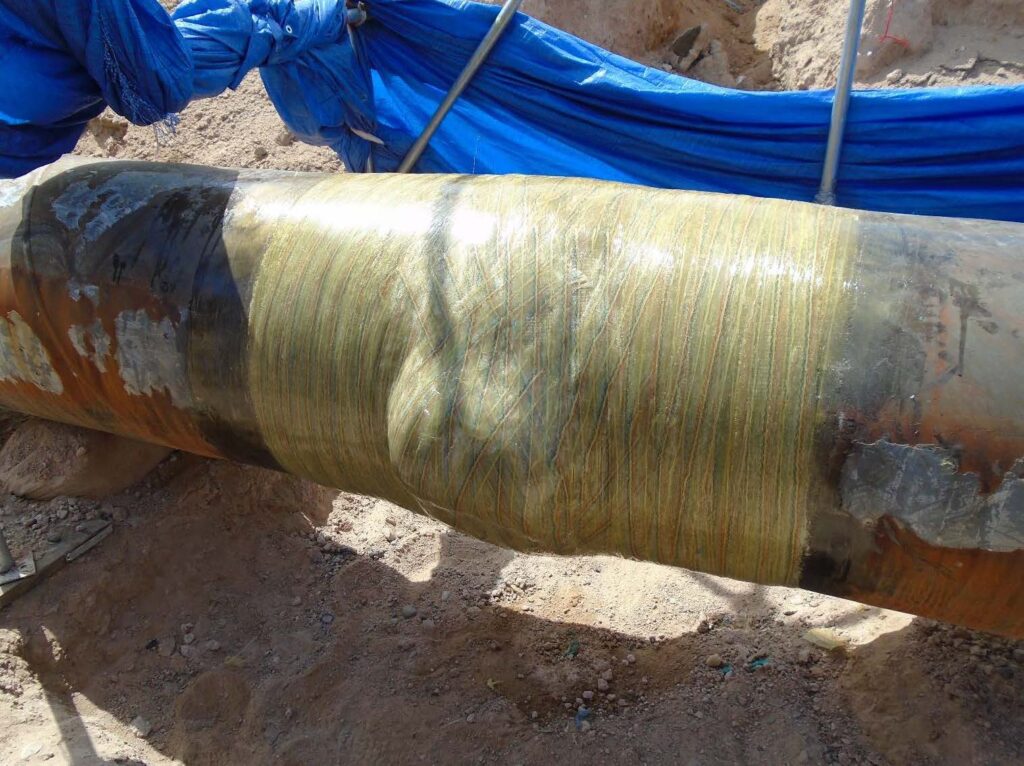