Challenges
- Urgent leak seal
- Through-wall defect
Benefits
- Cost-effective and timely repair
- No hot work or shutdown required
Scope
One of the world’s leading energy trading and shipping companies contacted ICR to complete an urgent leak seal, and subsequent engineered composite repair, aboard its liquefied natural gas (LNG) tanker located off the coast of Africa.
The vessel, one of the world’s largest LNG tankers, had suffered a through-wall defect caused by external corrosion on a 24-inch carbon steel tee section in a seawater line. The affected area was identified at a suction point in a deep ballast tank, located on the starboard side towards the aft section of the vessel.
The project scope included performing an urgent leak seal, delivering an engineering design calculation complete with design sketch, and providing the materials and personnel to install the Technowrap™ repair.
Solution
ICR mobilised trained UK technicians and materials to the vessel at the onboarding port. By working closely with the onboard crew and onshore support, ICR maintained effective communication throughout the successful repair process. While the technicians were onboard, ICR also supported the vessel crew by demonstrating the live leak seal procedure in case any initial repairs were required while awaiting an LR-approved repair.
The live leak seal was completed using Technoseal Epoxy Putty. Once the live leak seal was complete, the client mechanically prepped the affected surface area achieving a cleanliness of ST3, and a minimum surface roughness of 40 microns.
ICR’s technician then applied the composite repair which used a combination of Technowrap 2K™, a multi-directional glass cloth, and a high ambient (HA) resin. A successful leak seal test was completed after the first two layers were applied, before the subsequent 10 layers were installed.
Result
The project was successfully completed within five day shifts. ICR was able to quickly mobilise materials and personnel to the vessel and meet the urgent repair needs within the desired timeframe and budget.
Completed while avoiding any hot work or shutdown, this project showcased the advantages of using ICR and Technowrap™ for live leak seal and composite repairs.
Please click here for more on our Technowrap™ composite repairs or to get in touch with our team.
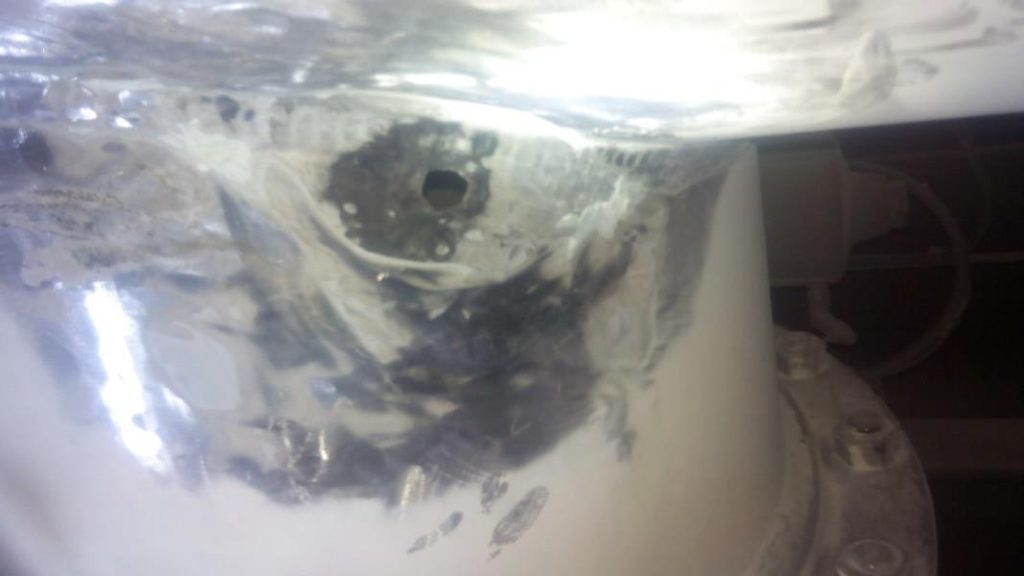
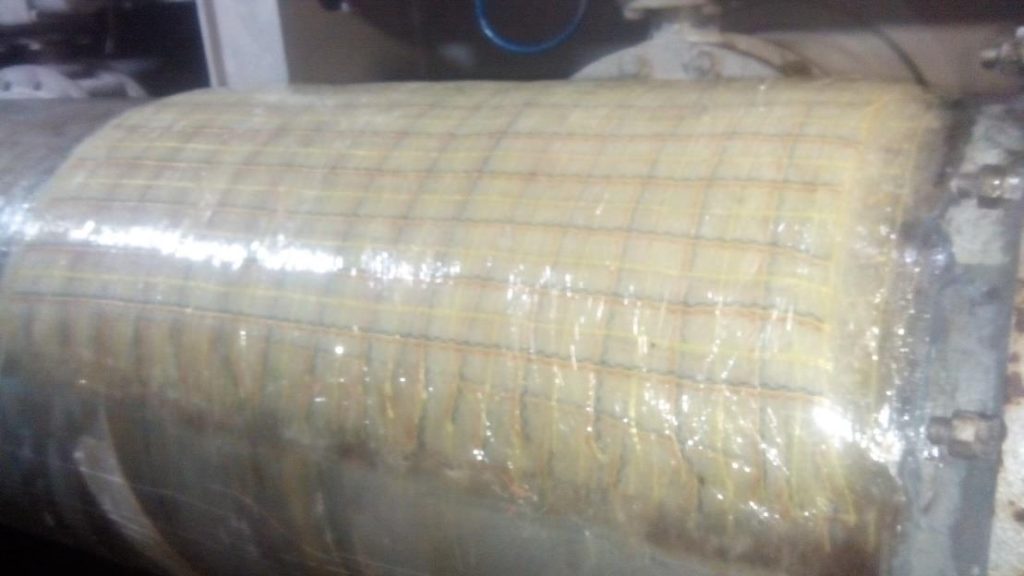
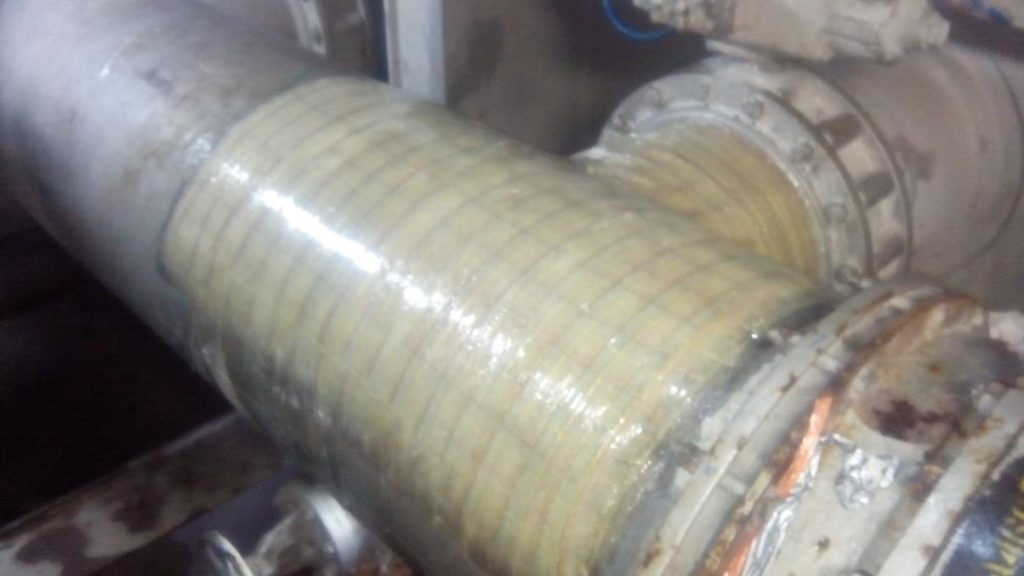
Challenges
- Multiple repairs
- Offshore platform
Benefits
- Quick and cost-effective repair
- No shutdown required
Scope
A global oil and gas operator has utilised ICR’s composite repair technology, Technowrap™, to complete multiple repairs on its Utilities and Quarters (UQ) platform in the North Sea.
During a routine assessment, the operator identified several areas of corrosion on the accommodation roof and approached ICR for a quick, cost-effective, and long-term solution with a 20-year design life. The repair needed to reinforce the remaining carbon steel, which averaged 1mm in thickness, with a design load of 0.005/mm².
The project scope included working with the onboard inspection and FM team to ensure that the Technowrap™ application ran smoothly and was within the design requirements for ISO 24817. Following the inspection, the FM team were instructed to cold bond carbon steel plates to which the Technowrap™ SRS/DRS was then applied to bring the wall thickness to the operational requirements.
Solution
ICR collaborated with Stork, a global provider of integrated operations, maintenance, modification and asset integrity solutions, to deliver a suitable adhesion level through surface preparation as well as the use of various compression aids to allow for an even surface.
When engineering the design for this project, our experts considered the client’s specific requirements while ensuring compliance with industry standards. After design calculations were complete, our team determined an optimal solution compromising Technowrap™ SRS (Structural Rehabilitation System) – a carbon fibre cloth – and DRS (Deck Rehabilitation System), a rubber toughened epoxy resin.
Three layers of this solution, resulting in a repair thickness of 2.70mm, would restore the integrity of the roof areas while ensuring a 20-year design life.
Result
Requiring just one technician and one supervisor to complete the multiple repairs within the desired timeframe, this proved to be a very cost-effective and efficient project for our client.
Pleased with the results, the operator has requested our continued support for additional composite repairs in other areas of the asset.
For more on our Technowrap™ composite repairs or to get in touch with our team, please click here.
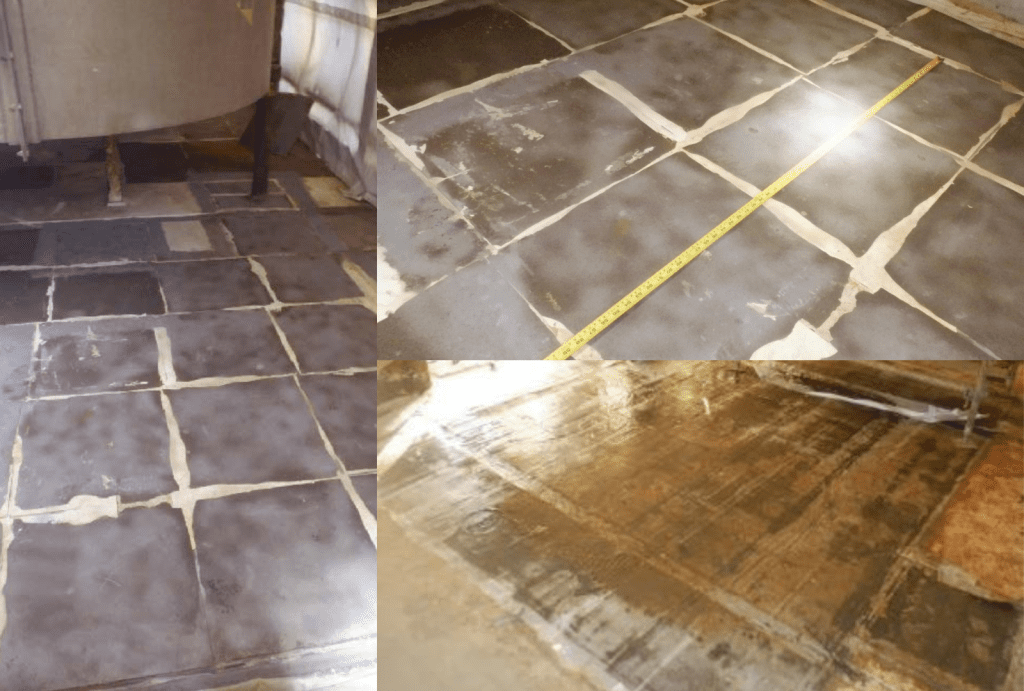
Challenges
- Significant wall loss
Benefits
- Collaboration with Ghana-based partner
- Quick and cost-effective repair
- No shutdown required
Scope
ICR has collaborated with its Ghana-based partner, Gecric Asset Integrity Management Limited, to restore the integrity of an air buffer bottle aboard a customer’s floating production storage and offloading (FPSO) vessel.
Located off the coast of Ghana, the customer identified significant wall loss on the asset due to external corrosion. Seeking a quick and effective solution, the customer requested the design and installation of an engineered composite repair solution with a 10-year design life.
Solution
The Technowrap™ composite repair solution was expertly designed for installation on the remaining 1.8mm wall thickness and to meet the required 10-year design life. The wall loss was quickly restored using ICR’s Technowrap™ 2K cloth type and high-temperature (HT) resin.
Surface preparation was completed to a cleanliness level of ST3 and a minimum surface roughness of 54 microns before 15 layers of the Technowrap™ engineered solution were installed, ensuring the air buffer bottle’s integrity was restored and the 10-year design life was achieved.
Extensive quality checks were completed throughout the project to verify the repair’s effectiveness.
Result
By partnering with Gecric Asset Integrity Management, we quickly mobilised Ghana-based technicians and materials to the FPSO before completing the repair within five-day shifts.
The project was safely executed without shutdown, further ensuring the repair was both cost-effective and timely.
Click here to learn more about Technowrap™, or here to get in touch with our team.
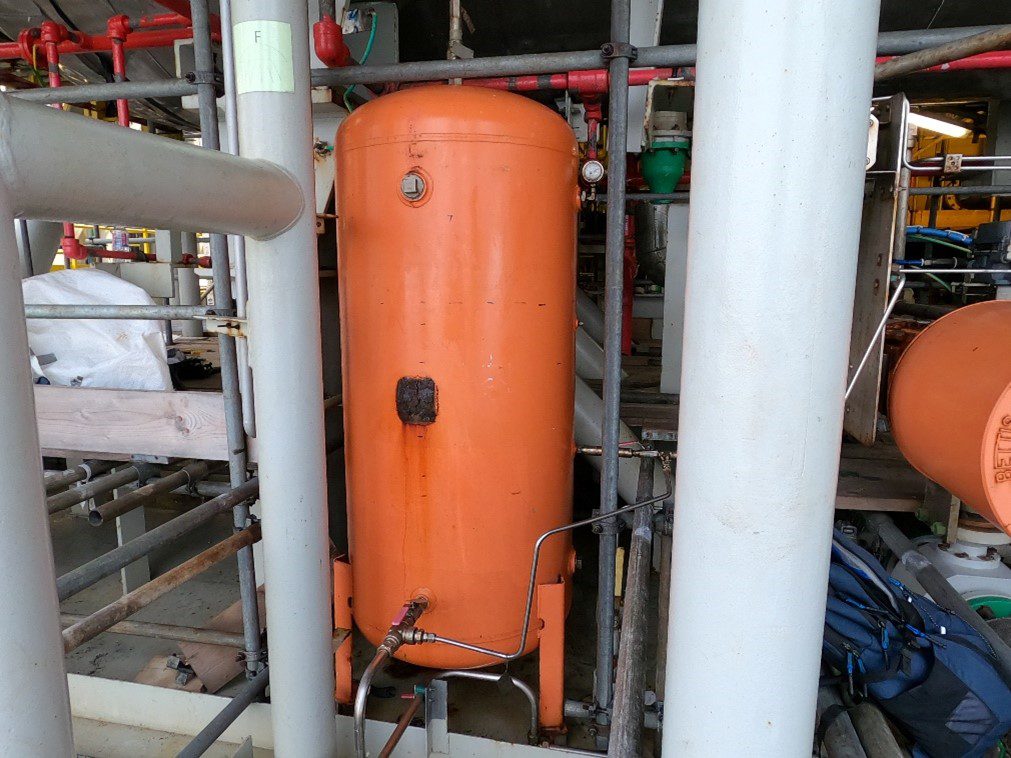
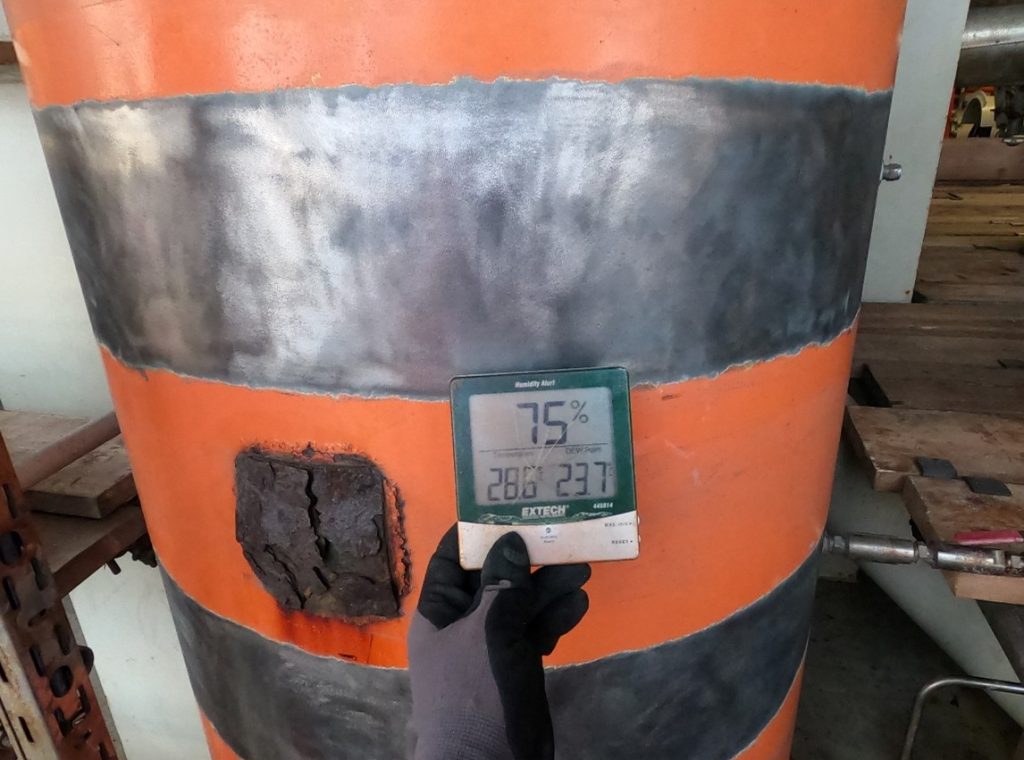
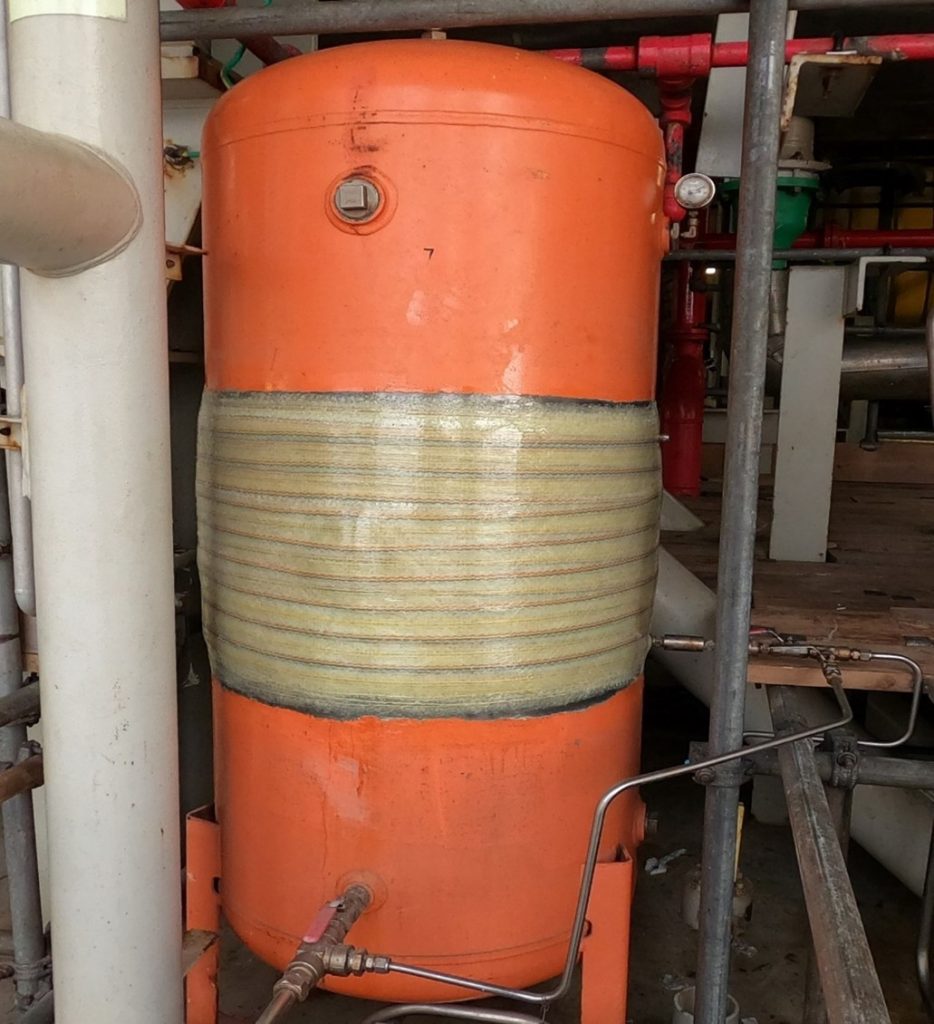
Challenges
- Live leak seal repair
Benefits
- Cost-effective
- Quick repair
- No shutdown required
Scope
A full-service terminal and processing facility requested ICR to perform a live leak seal at its multi-modal transfer facility in Galveston, Texas, USA. The repair was required on a 3” carbon steel tee on a wastewater line that had suffered a through-wall defect caused by internal and external corrosion.
Following the live leak seal, ICR was requested to complete an engineered composite repair solution with a design life of 10 years to restore the integrity of the line. The scope included an engineered design calculation, complete with a design sketch, materials, and personnel to execute the repair.
Solution
After ensuring the leak was effectively sealed, the piping was surface prepped for the Technowrap™ application using a bristle blasting method, which ensured a cleanliness level of ST3 and a minimum surface roughness of 40 microns.
Following surface preparation, ICR personnel applied two of the 10 required layers before conducting a successful leak seal test. The remaining eight layers were then installed using a combination of our 2K cloth type and low-temperature (LT) resin.
Result
The leak seal and Technowrap™ repair successfully restored the line’s integrity, while a 10-year design life was met.
As ICR quickly completed both the live leak seal and the Technowrap™ repair, the project remained cost-effective and timely for our customer. This project further demonstrates the effectiveness of Technowrap™ in supporting urgent repairs.
Click here to learn more about our composite repair technology, or reach out to our team here.
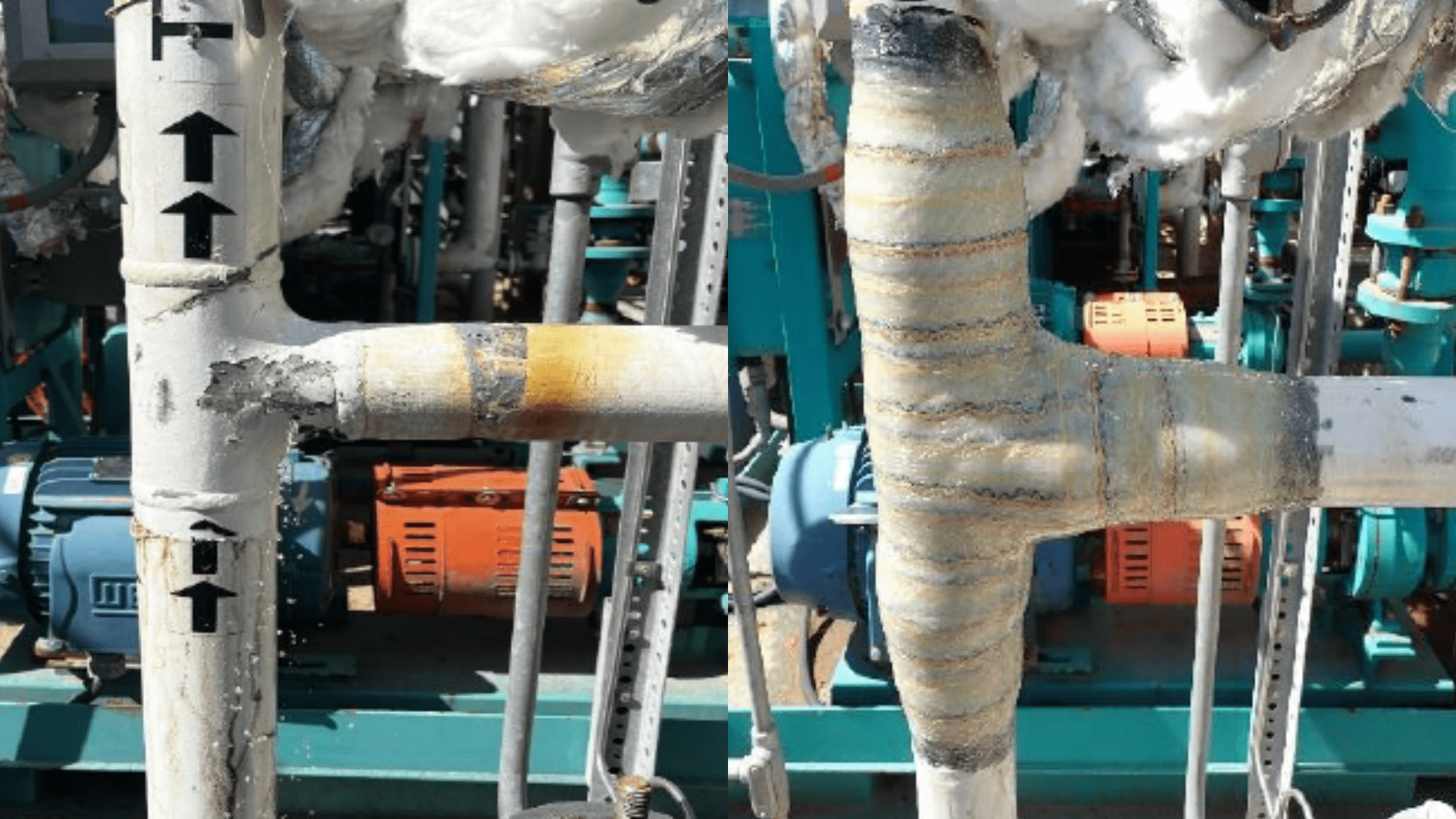
Challenges
- 550 meter repair
- Pipeline lifting
- Welded saddle supports
Benefits
- Cost-effective alternative
- Quick installation
- No shutdown
Scope
A 32” produced water line had significant internal erosion/corrosion at the 6’oclock position with a minimum remaining wall thickness of 4mm. The length of pipeline requiring repair was approximately 550 meters which contained various saddle supports, some of which were welded. The client required a qualification test of the proposed repair solution, on site, prior to installation of the actual repair.
Solution
The scope of work was to provide an engineered design, with 20 year repair lifetime, trained personnel and Technowrap 2K™ with Technowrap HP PRS™ materials to affect repair. Design pressure of the line was 47Barg, with design temperature of 82DegC.
Result
The installation procedure of the composite repair as demonstrated on the test spool, was approved by the client and produced for site installation. To complement the repair application procedure, a detailed lifting plan of the pipeline over the supports was created to ensure complete encapsulation of the pipeline. Additional requirements of applying the repair on all areas of the pipework included where the pipe work rested on the pipe supports.
For more on our Technowrap™ composite repairs, click here.
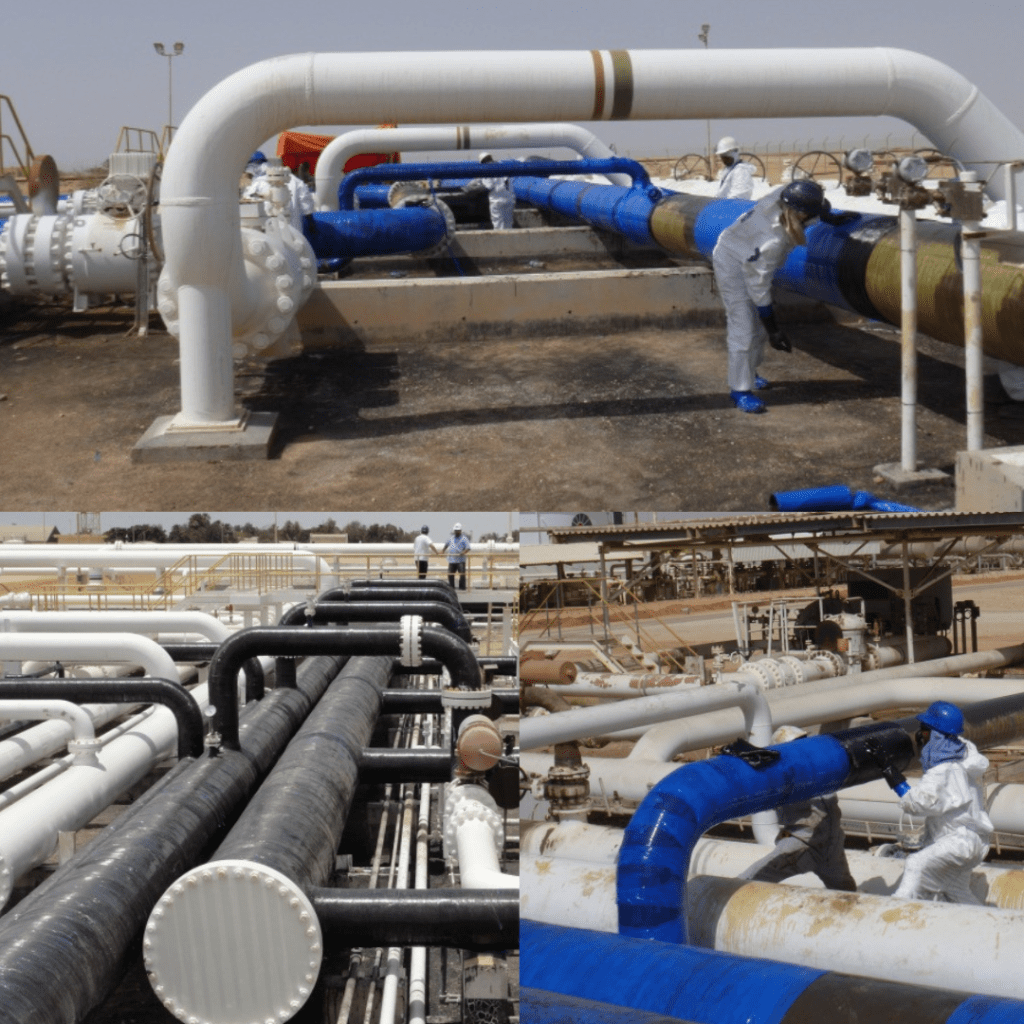
Client: Major operator
Location: Freeport, Texas – USA
Scope
During a routine inspection of pipe systems, a large operator based in Freeport, Texas, identified a localised area of external corrosion under tmin on a six-inch carbon steel pipeline in butane service.
The operator contacted ICR looking for a long-term, time-sensitive solution to restore the integrity of this straight pipe without shutting down operations. At the customer’s request, the engineered repair solution required a design life of 10 years. The scope of work included engineering design calculations, a design sketch, and materials.
Solution
ICR collaborated with its rope access installation partner, Acuren, to surface prep the repair area using a bristle blasting method to achieve a cleanliness standard of ST-3, with a minimum surface roughness of 65 microns/2.5 mils.
Considering the condition of the asset and its environment, ICR design engineers calculated the required repair compliance with ISO 24817 using Technowrap™ High Ambient (HA) system and 2K cloth to achieve the required 10-year design life requested by the customer.
Results
The piping was restored and corrosion mitigated thanks to the experience of the Acuren rope access team, and the fast-acting performance of Technowrap™ HA and Technowrap 2K™ which required 24 hours to cure.
Completed with minimal disruption and without shutting down operations, this project illustrated the cost and time advantages of utilising ICR’s composite repair technology over standard replacement methods. Tested and qualified to ISO 24817 and ASME PCC-2 Article 401 standards, and supported by a 30-year track record across multiple sectors, Technowrap™ promises a cost-effective, reliable, and long-term solution for repairs.
For more information on this solution, click here.
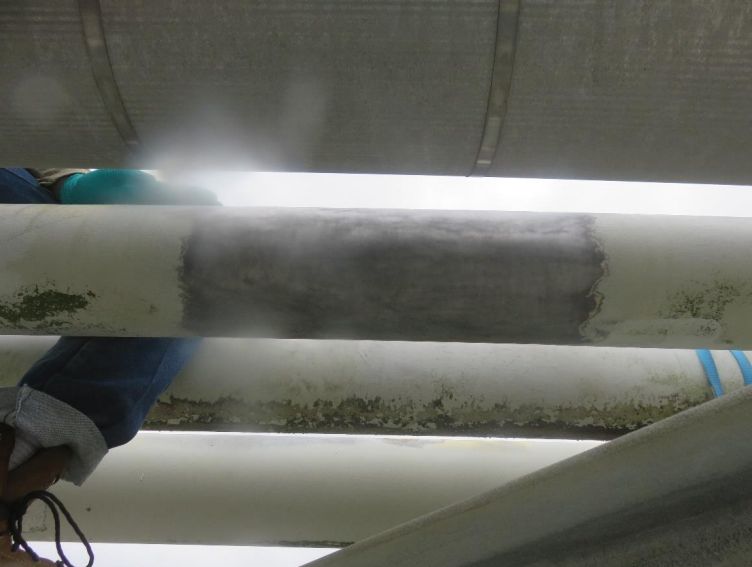
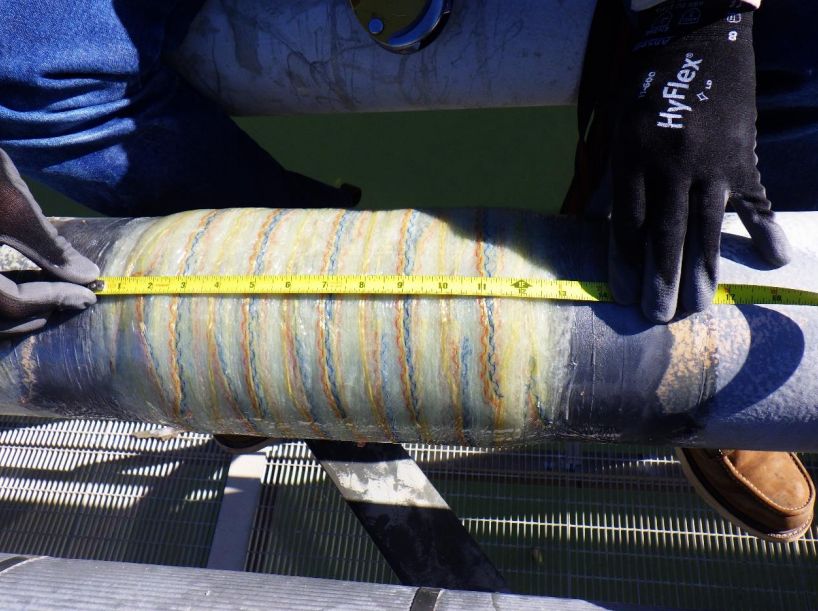
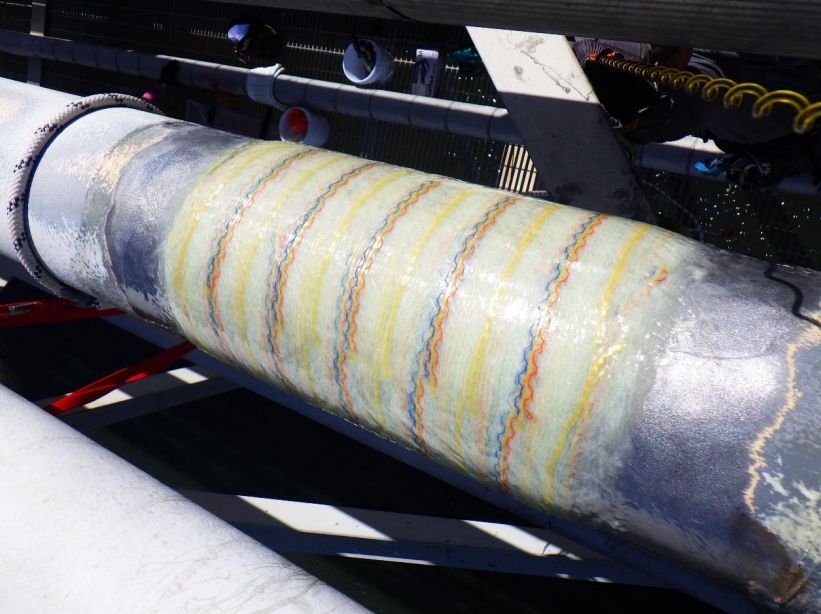
Client challenge
Our client, a major Australian energy operator, was experiencing internal corrosion across multiple welds on an 18″ inert-gas header causing pinhole leaks on the duplex line. Another temporary repair method had failed and the client was keen to address the issue in a timely manner.
What we did
Within the design parameters provided by the client, our technical engineers were able to provide an ISO24817 compliant design with a 20-year design life, utilising 5-layers of the Technowrap 2K High-Ambient system. This addressed multiple pinhole leaks across each of the straight, elbow and reducer geometries.
Results
Our technicians were able to provide the engineered repair on the live-line, thus eliminating any downtime for the client. Our technicians were also able to work on each repair area simultaneously without delay, reducing the required time onboard the asset.
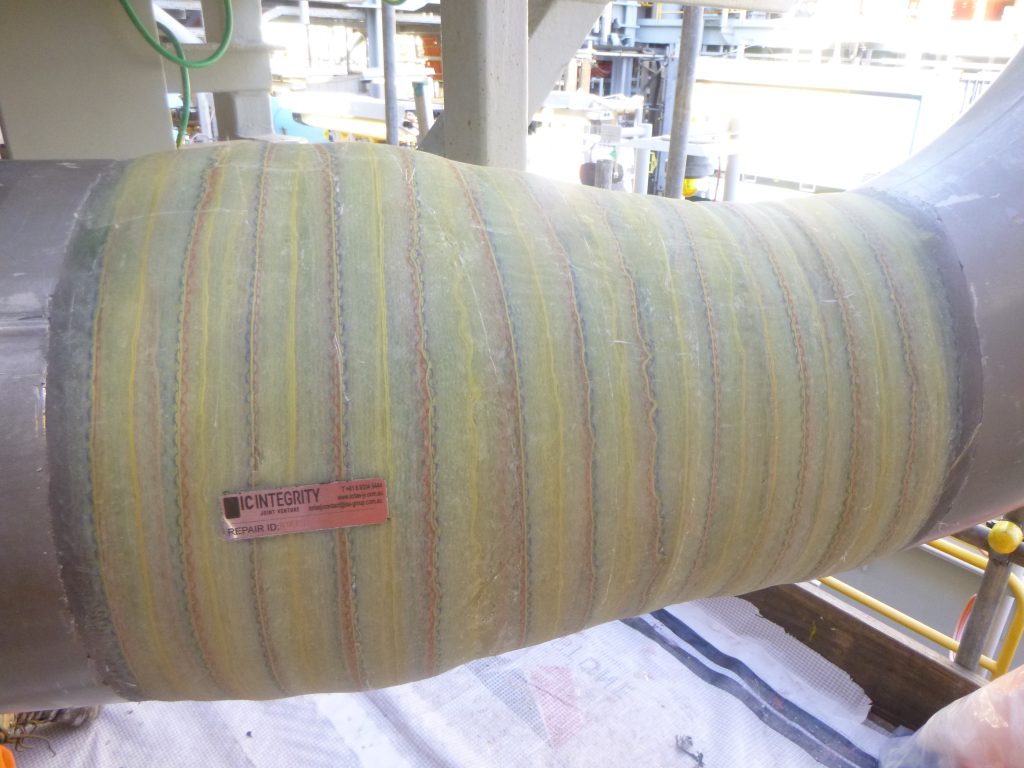
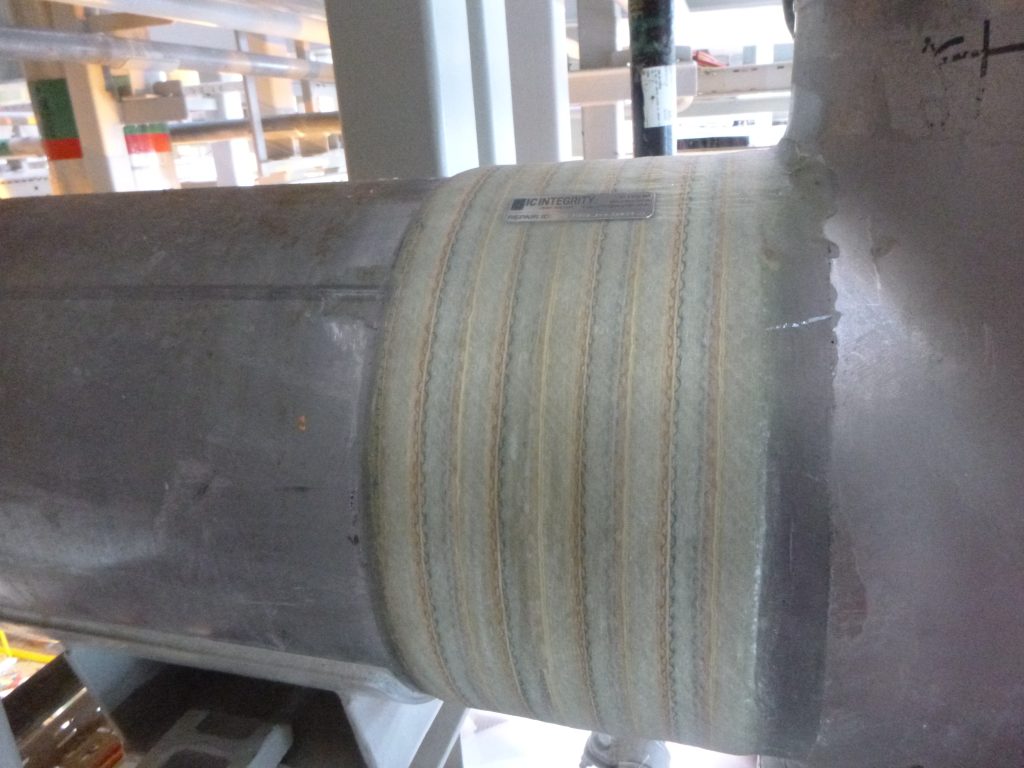
Client challenge
A global energy operator faced a critical challenge with the heli fuel storage and transfer skid on a platform, a crucial component of their operational needs. The skid, constructed from carbon steel was experiencing significant loss due to external corrosion. Our client urgently required a robust solution to address the corrosion issue and restore the integrity of the skid to ensure continued safe and efficient operations.
What we did
We devised a comprehensive strategy to mitigate the effects of corrosion and prolong the service life of the skid. To achieve the required cleanliness for appropriate adhesion levels, our technicians bristle blasted the landing areas to ST3 giving a minimum surface roughness of 40 microns, this was calculated and designed for within the engineering parameters. Our team formulated an engineered design calculation and sketch tailored to the specific requirements of the repair which was reviewed and approved by our client. Drawing upon our extensive experience in structural integrity, we developed a robust repair plan aimed at addressing 2 main areas of concern. The repair solution involved the application of 1 layer of 2K and 8 layers of SRS using ICRs low temperature resin, meticulously executed by our expert team.
As part of the scope of works, we had to fashion a composite mould to bring elements of the structure together in a suitable manner to apply the composite wrap. Our team used Technowrap 2K cloth to create the mould from an intact part of the skid to have the correct angles and dimensions to apply to the sections of concern. This proved paramount in the success of our Technowrap application and bringing back the structural integrity to the Heli-skid.
Results
This repair, achieved a design life of five years with a design temperature of 50 °C, ensuring prolonged serviceability and reliability. The composite repair is designed to withstand the full applied load and axial bending motions which have been calculated and adhered to ensuring the Technowrap engineered repair is compliance with ISO 24817.
Scope
ICR was asked to offer a solution to reinstate a production chemical injection skid pan experiencing localised pitting, wall loss, and through-wall defects of varying sizes. Structural capacity was a minor consideration as loads were small, and the primary goal was to provide containment of fluids.
Solution
ICR proposed two layers of Technowrap 2K™ substrate with Technowrap HA™ (High Ambient) resin, with localised plates over numerous through-wall defects. The repair would fully cover the skid pan and ensure proper pan gradient for draining fluids. The repair was based on a 10 year design life, load of 20psf fluid loading, and a max temperature of 120ºF. The composite repair was designed to share the load with the steel, where it is assumed that this average remaining wall thickness is 0.125” (3.175mm). One challenge during the application was limited space access. The ICR technician fabricated a custom roller with an extension that enabled the Technowrap 2K™ to be applied between the equipment and skid pan catch basin to overcome the cramped working area.
Results
- The repair was engineered with a 10 year defined life
- No hot work required, reducing safety risk
- A cost-effective solution compared with welded replacement
- Carried out with minimal POB requirements
Client challenge
During routine flange maintenance work on a 16” transmission line, our client, a major US operator observed concerning issues with the protective bitumastic wrap. A subsequent inspection revealed the deterioration of the wrap and significant corrosion in the exposed area. Faced with the potential operational and environmental risks, it was essential that this was addressed immediately.
What we did
To mitigate the corrosion risks and extend the life of the affected area, our team implemented an engineered composite repair solution. The pipe underwent meticulous preparation to SP 3 standards, ensuring a clean and suitable surface for the application. Eight layers of Technowrap, designed to provide enhanced protection, were applied to the compromised section of the 16” transmission line.
The decision to opt for an engineered composite wrap aimed to provide a targeted and efficient solution, minimising downtime and avoiding the need for a complete pipeline replacement. This approach also eliminated the necessity for hot works, ensuring a safer and more environmentally friendly execution.
Results
The outcomes of our intervention exceeded expectations, offering several key benefits to our client:
Preservation of the existing line: The implementation of the engineered composite wrap successfully preserved the 16” transmission line, eliminating the need for a costly and time consuming replacement.
Elimination of hot works: The chosen solution avoided the use of hot works, mitigating safety risks and environmental concerns associated with traditional repair methods
Life extension achieved: The application of the engineered composite wrap, comprising eight layers of Tecnhowrap, provided a targeted five-year life extension to the affected area. This ensured the continued reliability and functionality of the transmission line.
This case study underscores the effectiveness of strategic interventions in preserving the integrity of crucial infrastructure.
By choosing an engineered composite wrap solution tailored to the specific challenges faced by the 16” transmission line, we successfully addressed the client’s concerns while delivering long-term benefits in terms of safety, efficiency, and operational continuity.