Date | Client | Location |
---|---|---|
January 2021 | Major O&G Company | UAE |
Scope
As part of a line rerouting project, a safe, reliable and fast cold work solution was required due to the complexities of the hydrocarbon condensate running through the line with 2.5 mole % of H2S (no hot work permitted). ICR were approached for the installation of a 3” 300# Quickflange™ on that line.
Cold line isolation and cold line cutting were performed successfully in conjunction with a 3rd party contractor and a localised hydro test for the Quickflange™ joint was completed successfully to the client’s specified testing pressure.
Significant HSE risks were a major consideration due to the line media and ensuring personnel working in the vicinity during project execution remained safe.
Solution
After thorough engineering evaluation ICR confirmed a 3” Sch40 Carbon Steel RF 300# installation could be installed by a specialist weldless connection technician.
After client approval, a locally based ICR technician and respective equipment was immediately mobilised to site from our local base in UAE to safely install the 3” cold connection. In conjunction with a 3rd party contractor a hydro test was successfully completed post installation.
Results & Benefits
- 100% Cold work installation process completed safely in less than 30 minutes by one certified local technician and one simple installation tool for that specific job
- ICR were able to react quickly and mobilise the Quickflange™ equipment and the manpower from its local base in UAE
- This subsequently allowed the operator to bring operations back on-line in short period
- Safety, time, production & cost savings were identified as significant benefits when compared to the conventional method of hot work and welding
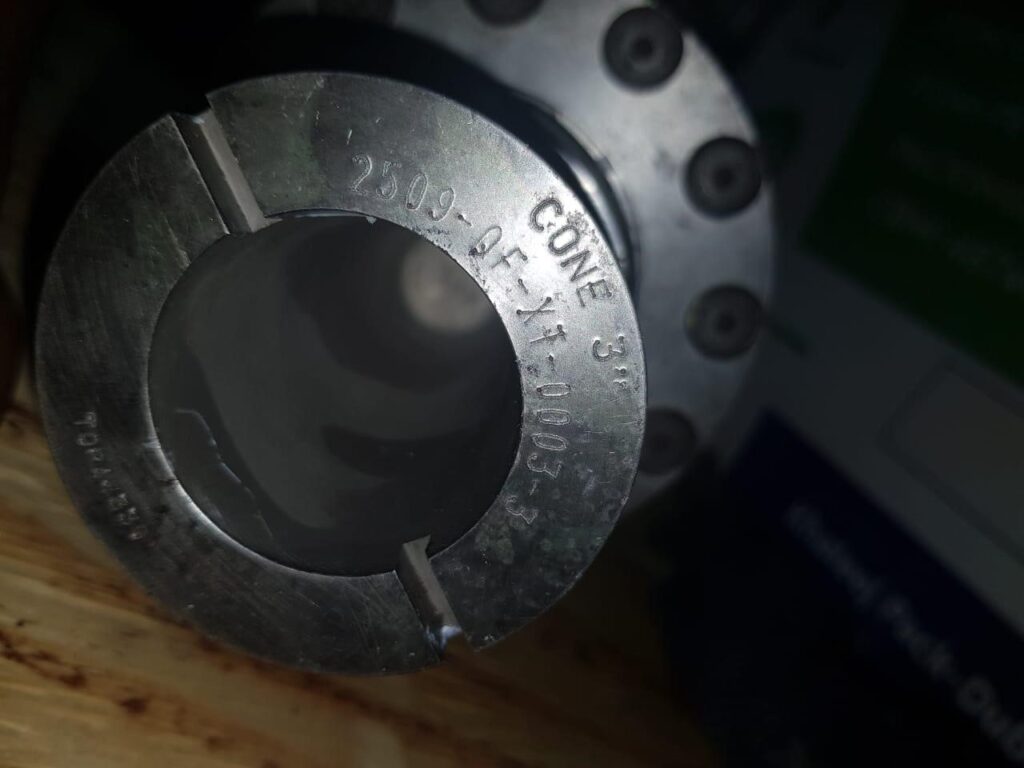
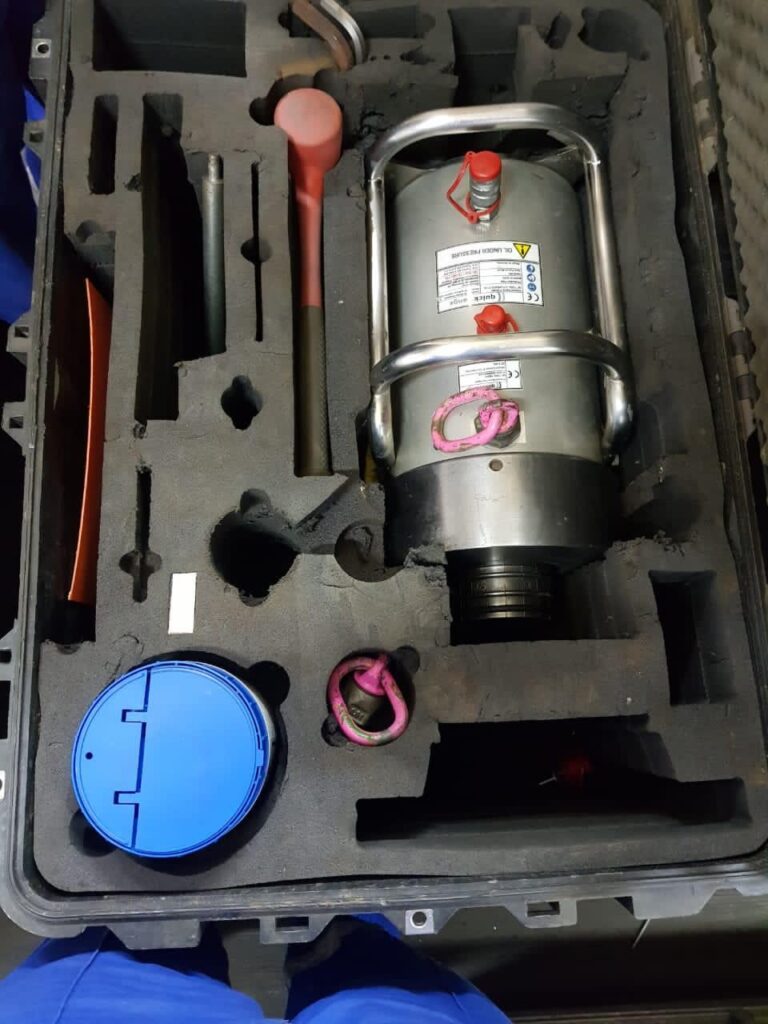
Client: Major Global Operator
Location: Gulf of Mexico
Scope
The Client wanted to use the Quickflange™ solution to complete an extension to a 12” hydrocarbon vent line on their installation in the Gulf of Mexico.
The scope involved the installation of a 12” schedule STD 150# RF A350LF2 CS Quickflange™ onto the vent line on the platform utilising ICR’s patented Quickflange™ solution.
Solution
ICR had a qualified 12” schedule STD 150# A350LF2 CS solution within the Quickflange™ product range for the customer’s application and had the Quickflange™ & Installation tooling available to mobilise.
The work site was situated at the top of the installation which made access to the site and the movement of the equipment to site awkward, this also meant that the available space at the worksite was limited.
Results & Benefits
- ICR mobilised the 12” schedule STD Quickflange™ and installation tooling from its base in Houston to the delivery point in Louisiana
- The ICR technician was mobilised to the platform to conduct the installation, working alongside platform personnel
- Once permits and lift plans were in place the pipe was cut and prepped ready for the installation
- The ICR technician was able to complete the installation within 1 shift and once the work site was made safe, was de-mobbed from the platform the following day
- Scope delivered on time, within budget and with no incidents
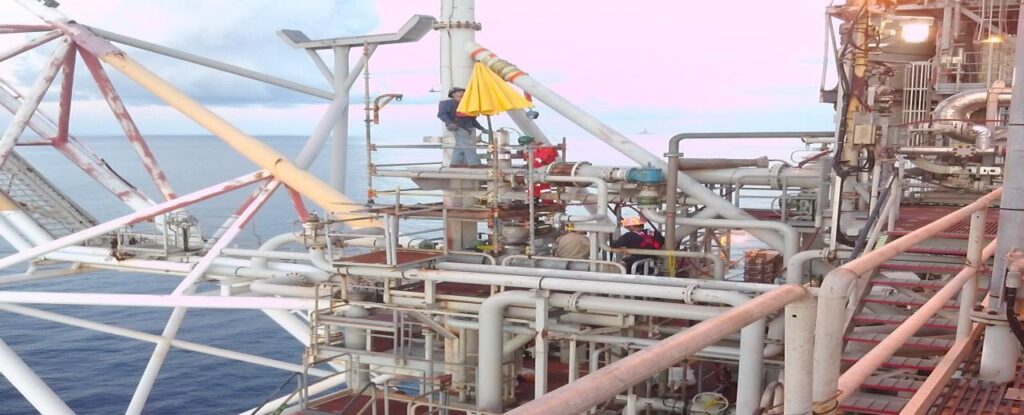
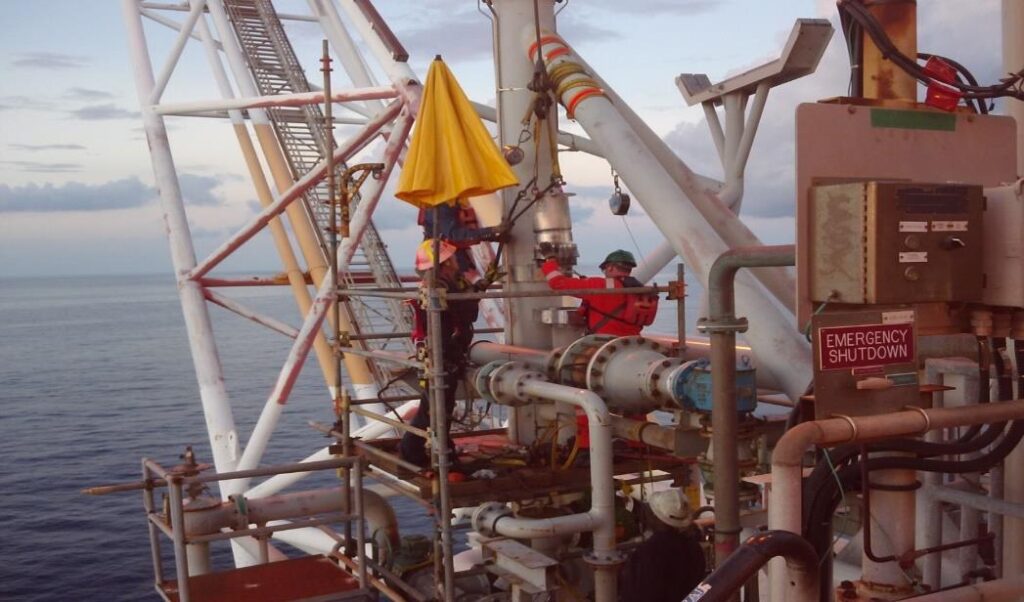
Date | Client | Location |
---|---|---|
May 2021 | BP | Idku, Egypt, West Nile Delta (WND) |
Scope
Due to the nature of the application and high risk associated with hot work, Quickflange™ was selected as an alternative cold work solution to carry out a tie-in for a replacement spool in an onshore refinery.
Solution
Following the award of the scope from the client, ICR developed a virtual/online training course to train Seaharvest’s 2 technicians so they could carry out the repair. The client’s maintenance crew cut the pipe at 11am, and by 12 noon Seaharvest technicians had the flange installed. By 3pm the flange and been hydrotested to 50bar, the crew had completed the scope and left the site.
Results & Benefits
- Reduced down time
- Limited footprint of manpower onsite
- Large cost savings compared to the complex requirements that would have been involved with traditional hotwork with the potential for additional manpower, fire watch crews, welding habitats and NDT requirements
- 80% time saving
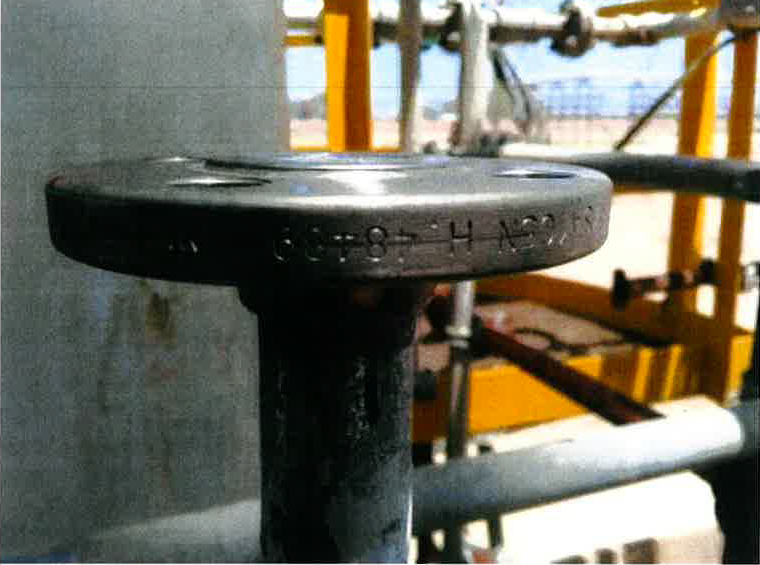
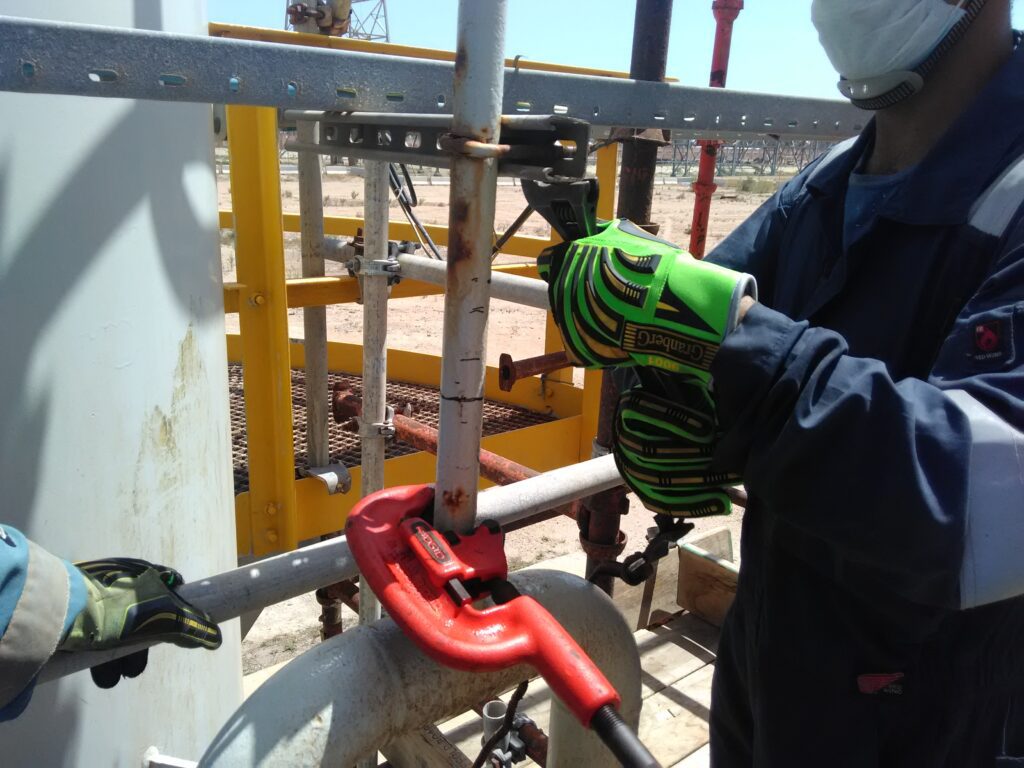
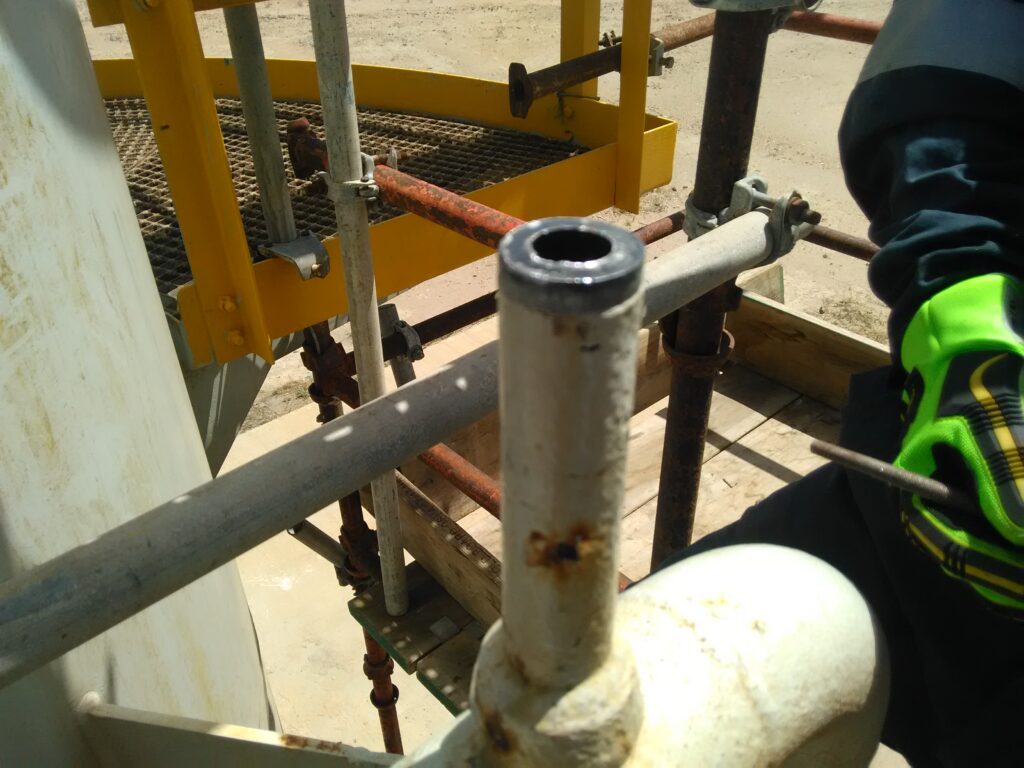
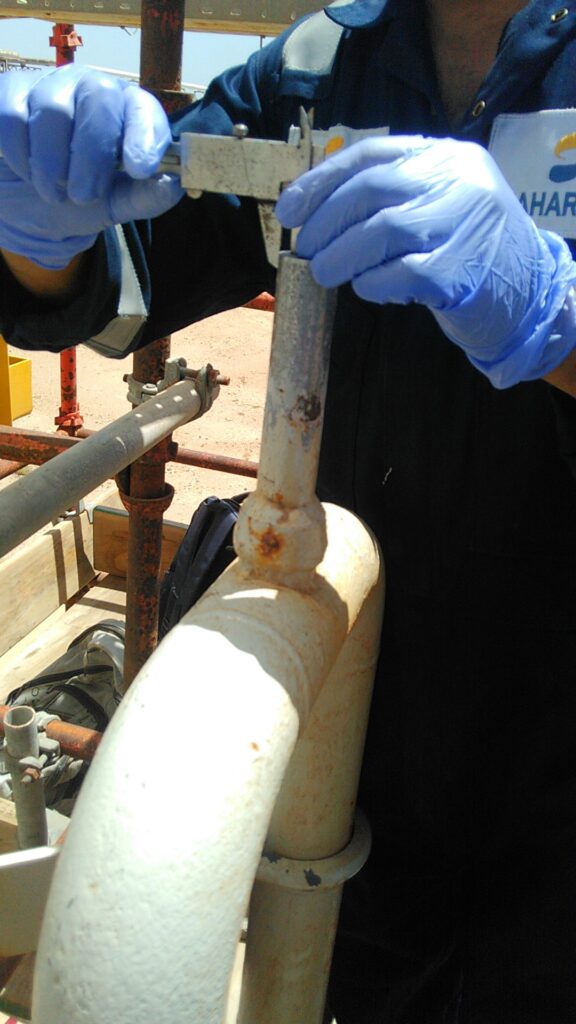