Client: Major European chemical manufacturer
Asset: Manufacturing plant
Location: UK
Client challenge
A major European chemical manufacturer undertaking plant upgrades in the UK faced the challenge of creating 10” diameter holes in 20” diameter x 1½” wall carbon steel pipes. The program of works was challenging, with a short timeframe required for completion. In addition there were tight access restrictions at some work locations, requiring innovative solutions for efficient execution.
What we did
In response to the client’s challenges, we developed a strategic solution to meet the demanding scope. Instead of the conventional approach of drilling a smaller hole and boring it out to the desired size, we opted for trepanning in a single operation. This decision aimed to streamline the process and adhere to the tight timeframe set by our client.
Leveraging our machining expertise and industry contacts, we commissioned 10” trepanning cutters. These cutters were then paired with our modular drilling equipment. The modular design of the equipment allowed it to fit into spaces with tight access restrictions, ensuring flexibility and adaptability to the challenging work environments.
Results
Our innovative approach and precise execution led to several achievements:
Efficient operation: The trepanning cutters, paired with the modular drilling equipment, proved to be an efficient solution. The decision to trepan in a single operation eliminated the need for additional finishing steps, saving time and resources.
Tolerance compliance: The cutters performed flawlessly, producing holes to the required tolerance without the need for further finishing operations. This precision ensured that the newly created holes met the exact specifications set by the client.
Timely completion: Despite the challenging program of works and tight access restrictions, all holes were successfully completed within the specified timeframe. Our ability to navigate the constraints and deliver on time showcased their commitment to meeting client expectations.
In conclusion, our strategic use of trepanning cutters and modular drilling equipment not only addressed the client’s challenges in creating large-diameter holes but also demonstrated efficiency, precision, and timely completion of the complex work scope. This case study highlights the importance of innovative solutions in overcoming tight timeframes and access restrictions in industrial projects.
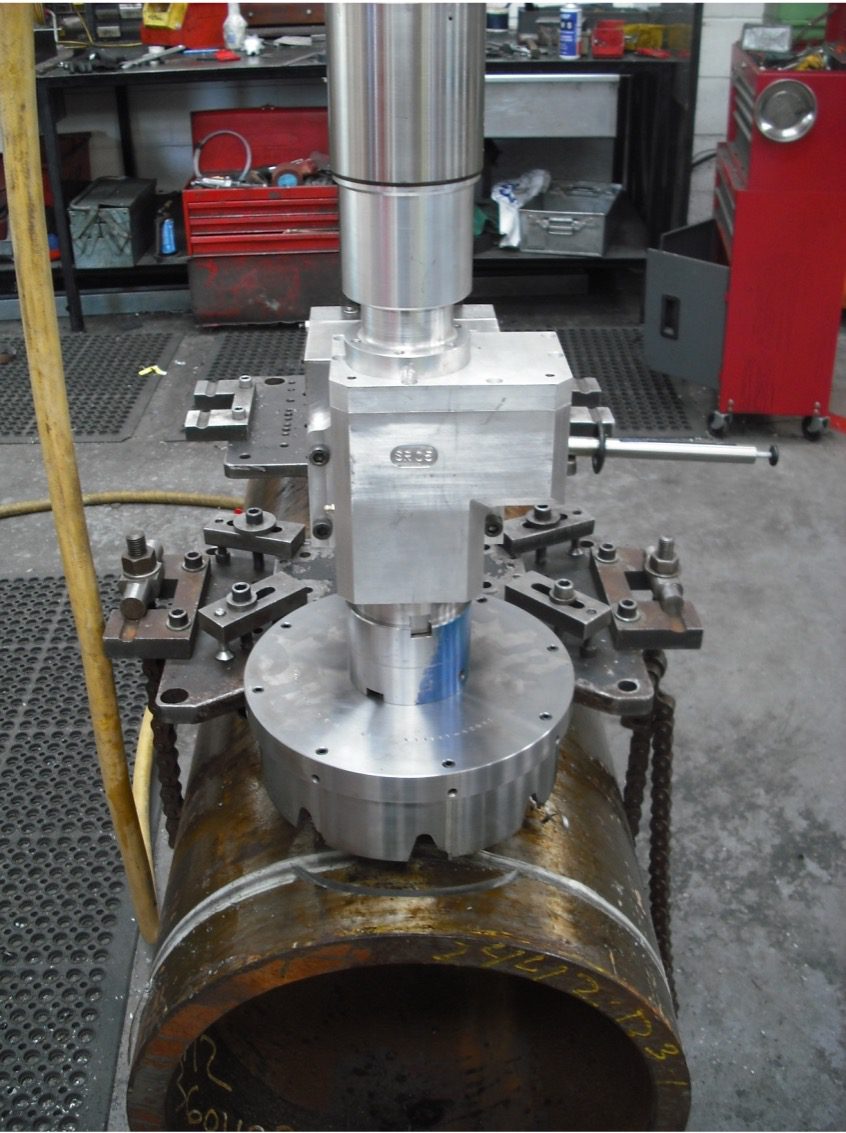
Client: Fabrication company
Asset: Tie-in spool
Location: Aberdeen, UK
Client challenge
A fabrication company in Aberdeen required machining of a subsea tie-in spool which had undergone onshore refurbishment. The spool, having been open to the elements, was deemed unfit for installation due to heavy corrosion on the flange sealing faces. With the imminent need for subsea installation, the challenge was to restore the spool’s integrity within a tight timeframe.
What we did
Both 7.1/6” 5K BX156 seal grooves on the spool required machining to eliminate corrosion and pitting, returning the dimensional sizes back to tolerance. The critical aspect was to achieve this with the minimum amount of metal being removal while ensuring the spool met the stated dimensional tolerances. The task had to be carried out within a tight time frame as subsea installation was only days away.
We deployed technicians along with an external mount flange facing machine for machining the faces and angles of the sealing grooves. The corrosion was expertly removed, and dimensions were meticulously measured using ball trammels to guarantee compliance with the necessary tolerances of +/- 0.05mm (0.002”).
Results
The precision machining carried out resulted in significant results and benefits for the client:
Dimensional reports: Detailed dimensional reports were produced for each flange, outlining both pre and post-machining sizes. This meticulous documentation satisfied the project quality plan, providing transparency and assurance of the work’s precision.
Successful hydrotesting: Following the machining process, the spool was returned to the fabricator. It underwent successful hydrotesting, ensuring that the refurbished spool met the required standards for installation load out.
Timely completion: Despite the tight timeframe, our efficient approach allowed for the refurbishment of the spool within the specified schedule. This timely completion enabled the client to proceed with subsea installation without delays.
Our precision machining solution not only addressed the corrosion challenges of the subsea tie-in spool but also provided the client with accurate dimensional data, successful hydrotesting, and adherence to project timelines. This case study underscores the importance of precision in refurbishment processes for critical subsea components.
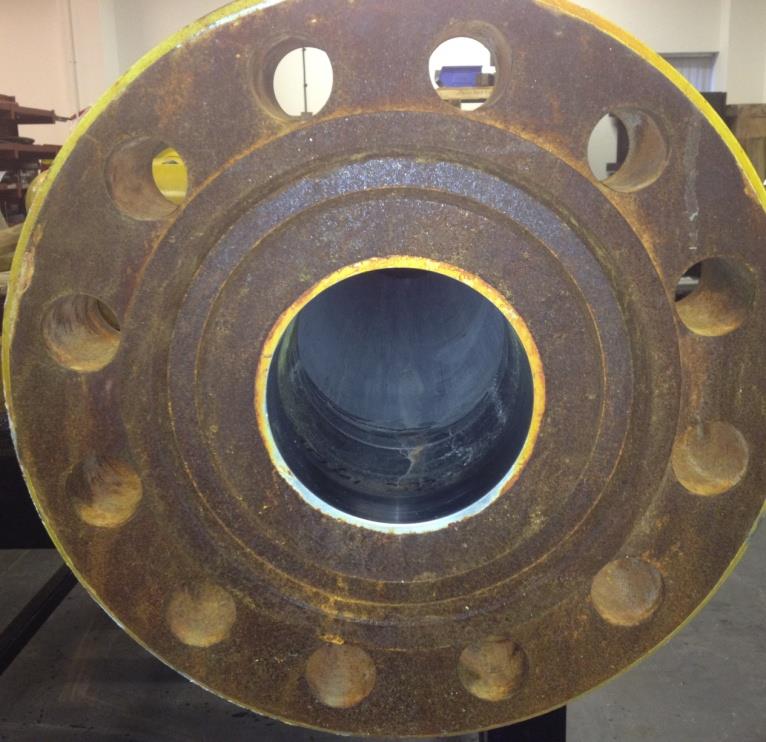
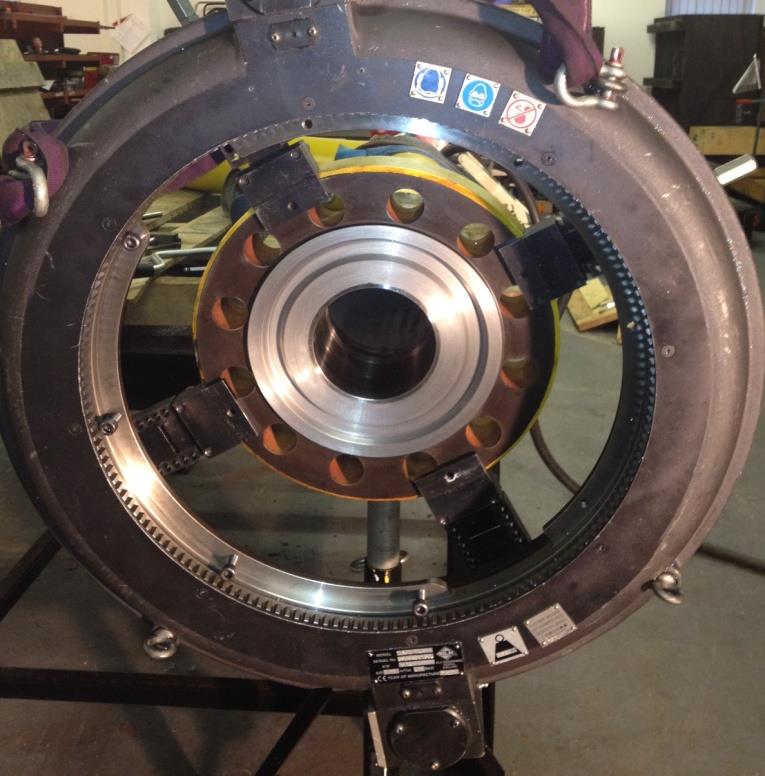
Client challenge
A shipbuilding company discovered that their pedestal crane flange was not level, coupled with a misalignment of bolt holes in the mating flange due to a different pitch circle diameter (PCD). This misalignment was causing significant delays in crucial shipyard operations and required a swift and efficient solution.
What we did
To address the misalignment issues of the pedestal crane flange, we devised a two-fold solution. Initially, the team utilised a portable flange facer to machine the surface, ensuring it adhered to the customer’s specifications. Subsequently, we designed and manufactured a customised jig plate. This plate is located precisely in the original misaligned bolt holes, enabling our team to re-drill new holes to the correct PCD, aligning the mating flanges accurately. The process required a rapid response to establish a methodology that would correct the PCD misalignment and guarantee precise results.
Results
The implementation of a portable flange facer enabled our team to precision-machine the pedestal crane flange, meeting exact customer specifications. Additionally, the utilisation of a meticulously designed jig plate streamlined the re-drilling of bolt holes to the correct PCD, guaranteeing precise alignment between mating flanges. This prompt intervention, coupled with our precision methodologies, averted the necessity of cutting off and replacing the flange. Not only did this save considerable time, but it also resulted in substantial cost savings for our client, showcasing the efficiency and cost-effectiveness of our approach.
This case study exemplifies our expertise in providing innovative and efficient solutions for precision alignment challenges in shipbuilding, ultimately minimising disruptions, reducing costs, and ensuring the timely progression of critical shipyard activities.
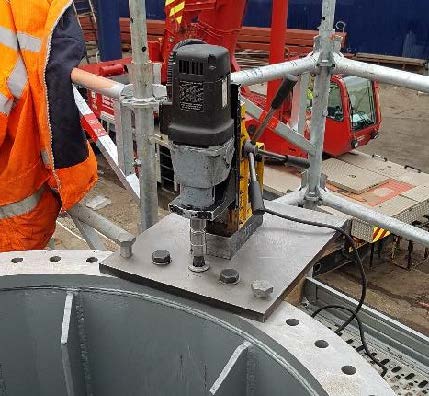
Date: March 2023
Client: TechnipFMC
Location: Dry Dock, North East England
Client challenge
Our team was commissioned by TechnipFMC – a global technology provider, during the final stages of a re-fit on one of their support and construction vessels. Our task was to provide a machining solution for both port and starboard aft thrusters. Upon inspection, it was discovered that the bores in the thruster mechanism had experienced operational wear and was out of tolerance, necessitating our intervention to machine out the bores. This enabled our client to install replacement sleeves, and our team carried out the final machining as per the specification.
What we did
Our team of expert machinists carefully assessed the condition of the thruster bores before devising a comprehensive solution to restore their functionality. Leveraging our cutting-edge technology, we employed our 150mm line boring, and 3m flange facing machines, to meticulously machine both the lower bores and upper faces of each thruster housing to the exact specifications and tolerance of 0.05mm. This precise and intricate machining work allowed us to successfully repair the damaged thrusters and ensure they functioned optimally, meeting the highest standards of quality and reliability.
Results
Thanks to our expert machining work and subsequent re-fit, the thruster housing will be able to operate for an additional 20+ years, without the need for cutting out the entire structure from the ship’s hull and fabricating replacement housings. This successful outcome not only saved our client significant time and money, but also ensured that the vessel could continue to operate with optimal efficiency and safety. Our team’s commitment to precision and excellence allowed us to deliver a long-lasting solution that exceeded our client’s expectations and cemented our reputation as a trusted and reliable partner for machining services.
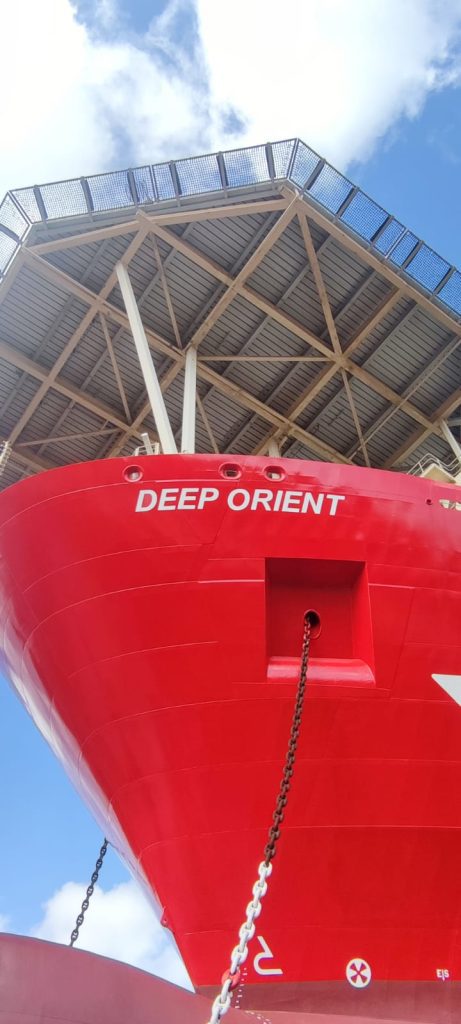
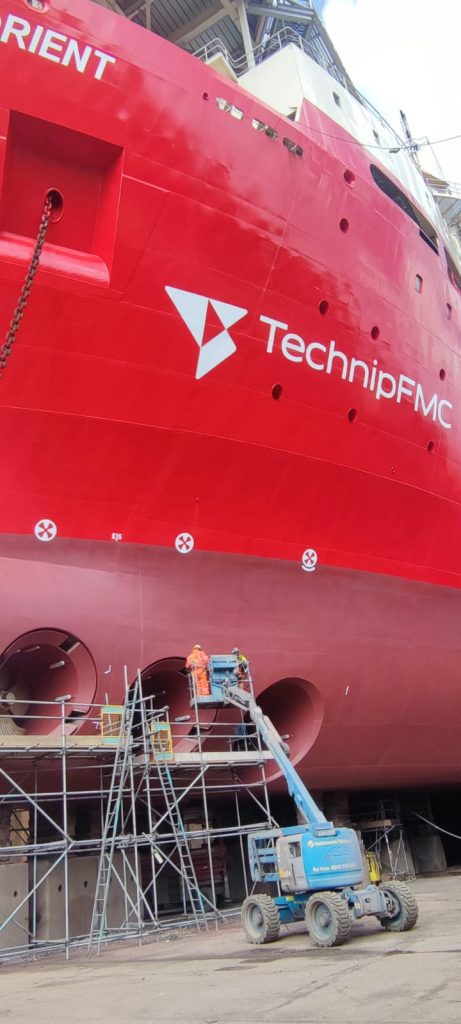
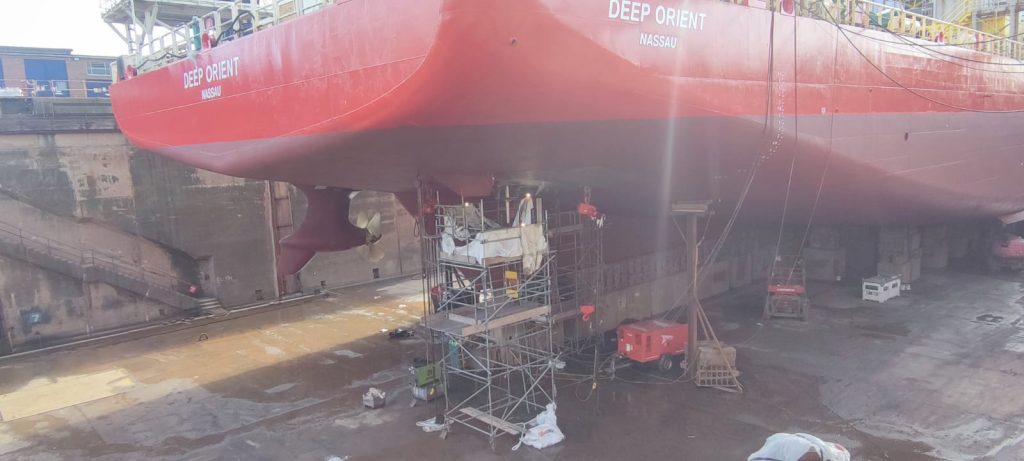
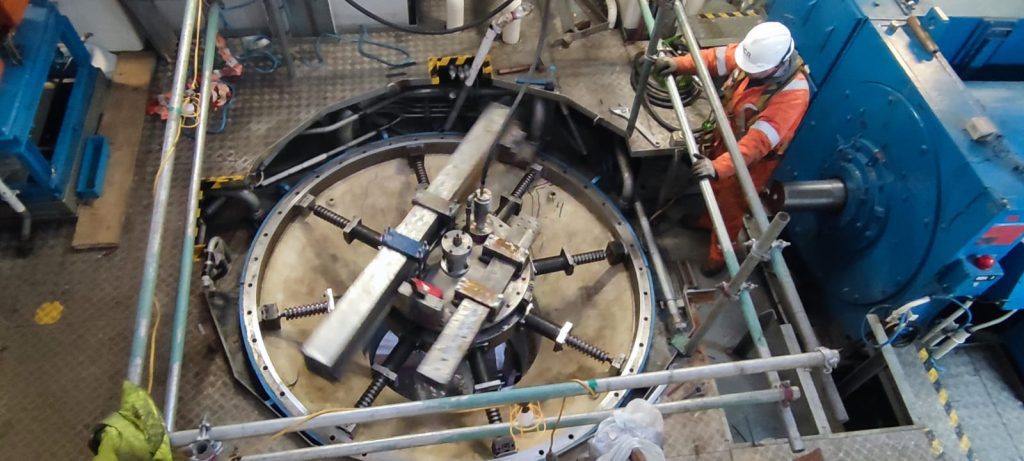
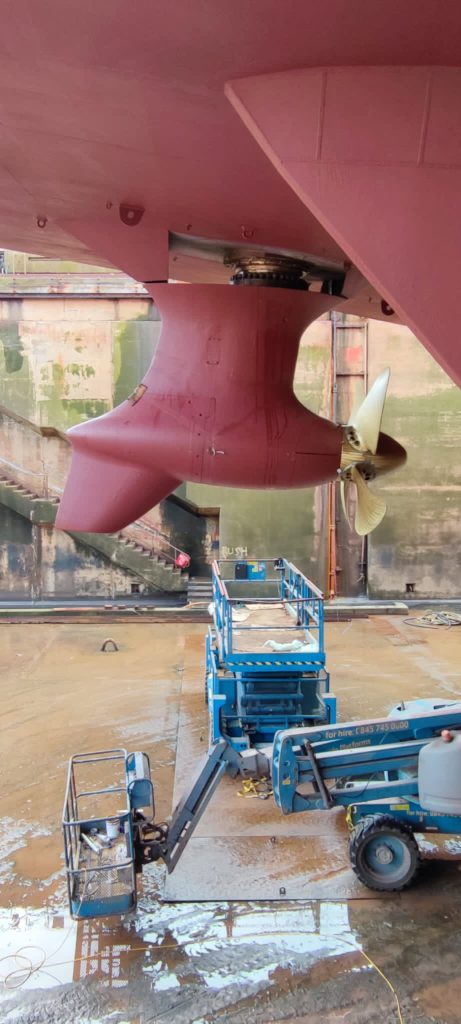
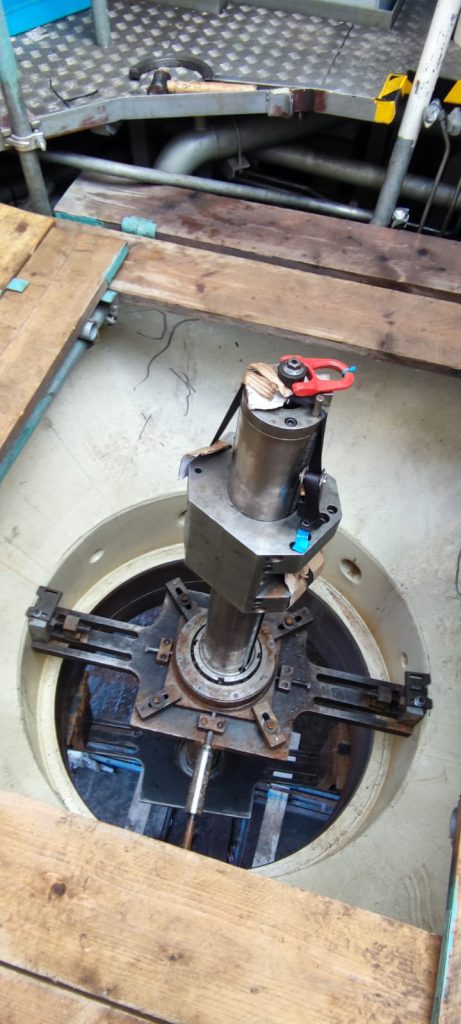
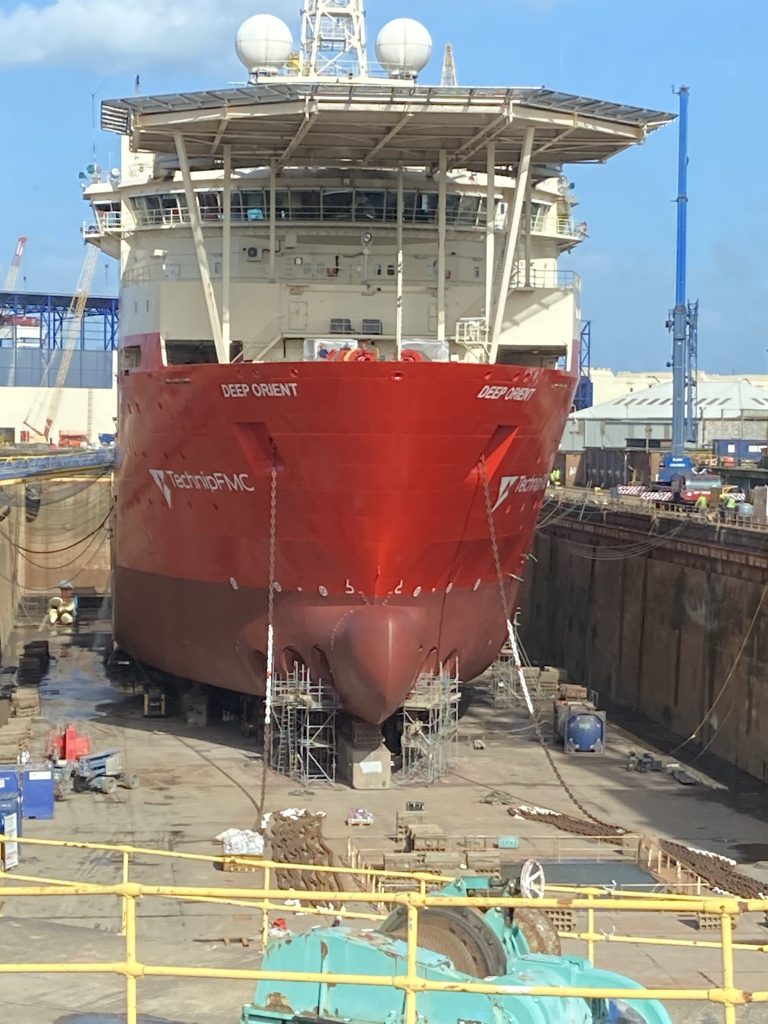
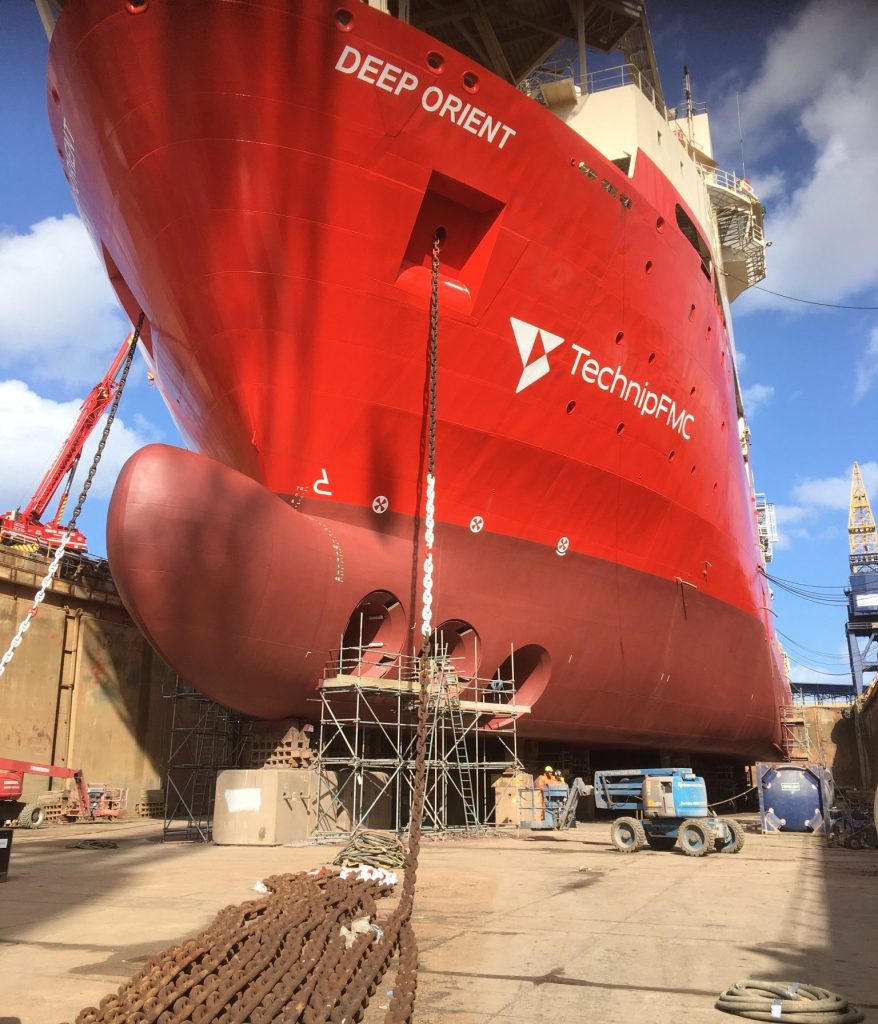
Scope
The power generation module contained three bearing pads welded to steel work and used to provide a level footprint for mounting the power generating unit within the module. The pads had been welded to the steelwork and were not level to either the module datum or each other. Surveying services had been used to provide flatness datums and material removal sizes for setting up the machining equipment. The machining equipment had to be able to span each plate and be clamped rather than welded to reduce requirement for hot work.
Solution
ICR technicians – together with a suitable size gantry mill – were mobilised to carry out this operation. The milling machine was set up to the survey datums and material was machined from the pads to bring them flat to the module datum and at the same level as each other.
Results & Benefits
- Following the machining operation an additional survey was carried out which confirmed that the pads were well within the required tolerance
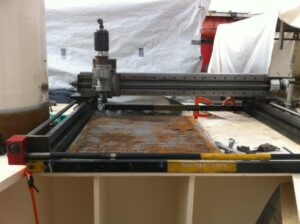
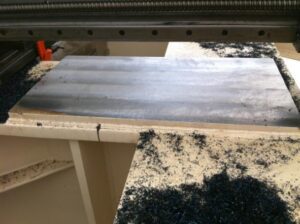
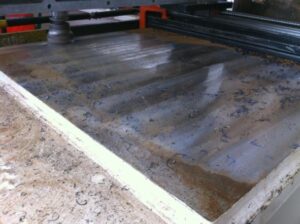
Scope
We were approached by a leading subsea contractor with regard to the machining of an auxiliary reel onboard an offshore vessel used for subsea pipe laying.
The auxiliary reel is used to provide pipe laying tension on smaller subsea pipes such as piggyback lines and umbilicals.
The 13m diameter auxiliary reel uses a pair of 22” diameter trunnions located within the bore of the reel to provide mounting support and a pivoting point.
On this application the trunnion locating bore had suffered considerable wear caused by weld failure resulting in the reel being placed out of action.
Solution
It was decided that the reel would be line bored to remove wear defects, machined to size and a replacement trunnion fitted to bring the reel back to service.
The work had to be scheduled for a period when the vessel was in port in Norway.
Due to the diameter and depth of machining required detailed pre engineering and machine adaption was required to ensure suitability. A 6” (150mm) diameter boring bar was required for this operation together with a hydraulic power pack to drive it and specially manufactured bearing mounts and support sections.
Two teams of Moss technicians were mobilised together with a hydraulically-driven line boring set up to provide 24 hour machining cover.
Results & Benefits
- As well as the line boring operation ICR technicians were able to support the trunnion removal operation and drilling of holes in and assembly of the trunnion support ring.
“We are very pleased with the ICR personnel and equipment, please extend my thanks to all involved.”
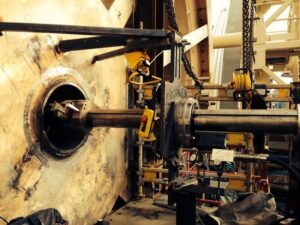
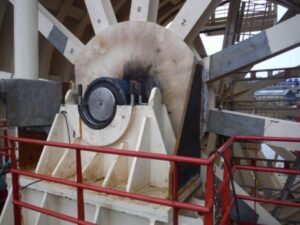
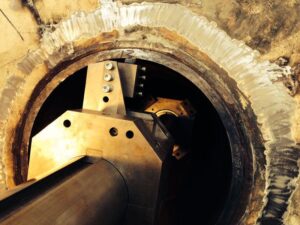
Date | Client | Location |
---|---|---|
April 2020 | Major Oil Refinery | North West England |
Scope
We were contracted at short notice to provide a large flange management team to support an emergent outage on a major UK refinery. ICR were required to supply fourteen bolting teams, all required equipment and an embedded management team for a six week planning, preparation and mechanical window. This was required to be on site seven days after call off to begin work. A full flange management package was requested by the customer to cover bolt ranges 7/8” up to 2 1/4” in a wide variety of joint sizes up to 120”. These scopes included a number of ‘special non standard joints’. Each job had individual job pack with required information to cover breakout and box-up with a suitable tagging operation.
Solution
Within five days we had sourced and mobilised all required manpower and equipment. Management were embedded into site and work packs were populated ready for day one of isolation operations. ICR supervision ensured that teams coming to site were brought on prior to work commencing to enable familiarisation of plant and scopes. All equipment was sited at key scopes to further increase efficiency once mechanical day one was started.
Results & Benefits
- Multi-skilled technicians supplied enabling reactive machining scopes to be completed at site
- Mobilisation at short notice of 16 additional machinists and equipment to site within one day of call off for a critical path emergent scope holding up the rebuild programme.
- The scope was completed safely and ahead of schedule, working closely with the site’s contracted welding team.
- We worked to the client’s required staggered shift requirements ensuring true 24hour coverage on critical path scopes.
- Where required, our technicians worked alongside fitting teams to further assist in the shutdown programme.
- The whole outage was completed safely, incident free and with a leak free start up.

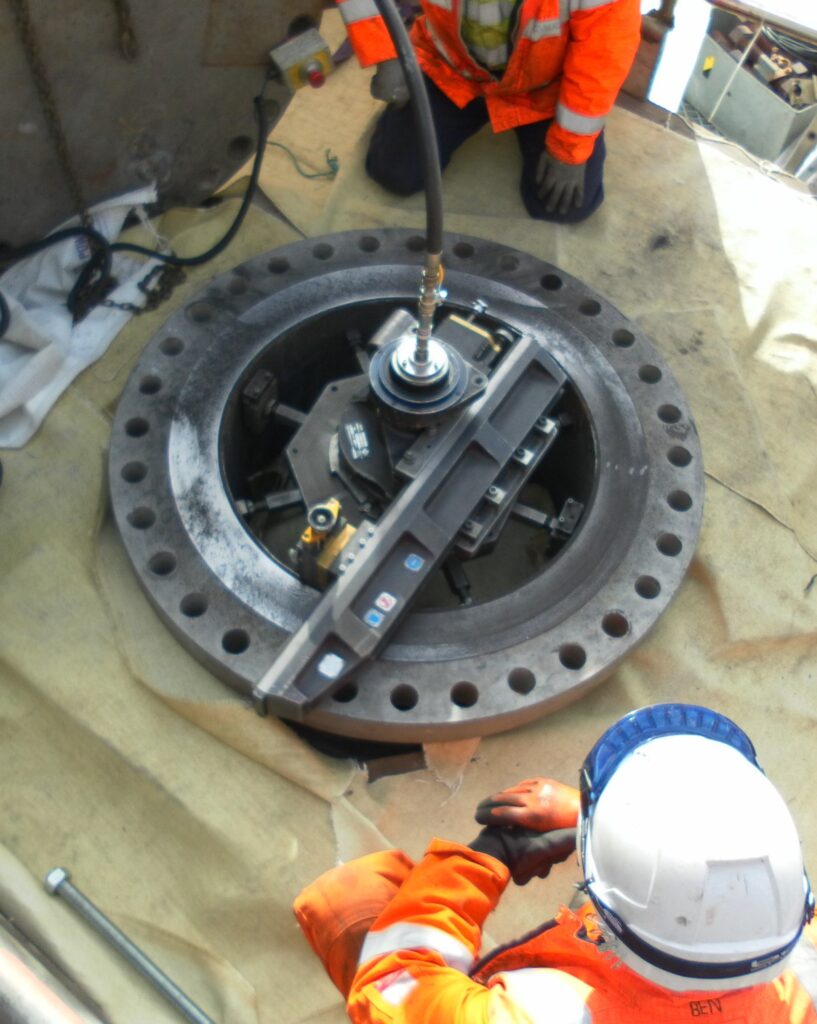
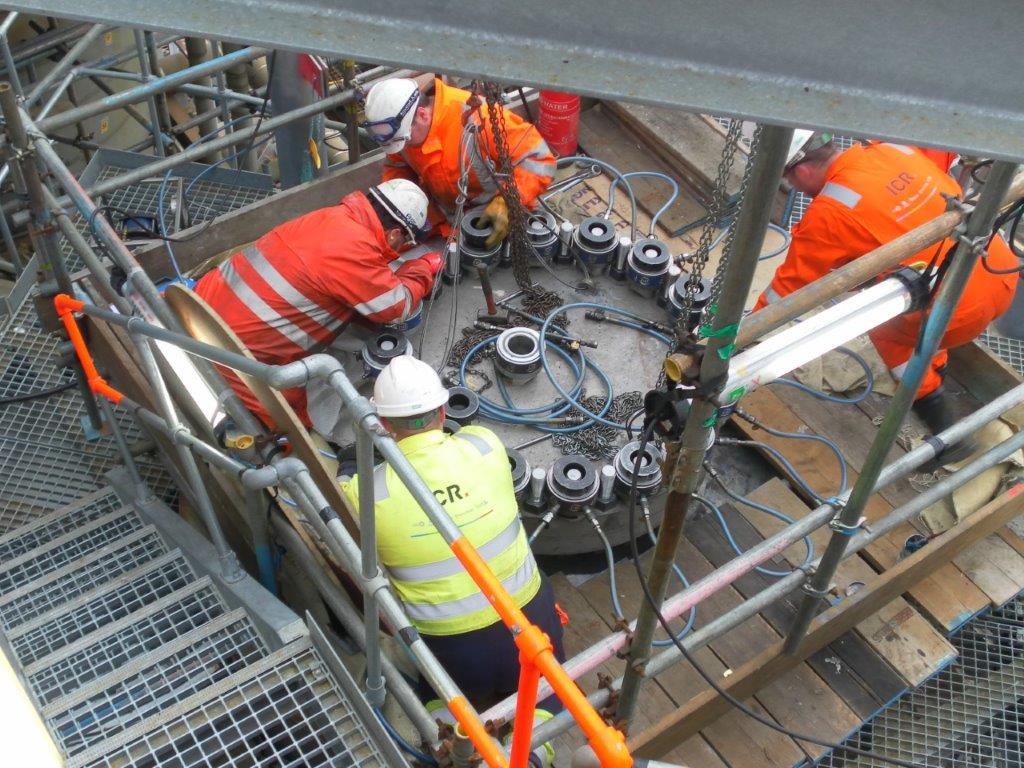