Date: May 2023
Client: International independent E&P company
Location: Dutch North Sea
Client challenge
Our client is an international independent exploration and production (E&P) company operating in the Dutch North Sea. They approached our team with a critical structural repair project involving the repair of ten beams with complex geometries and required a solution that could achieve compression on corroded beams. The objective was to provide a long-term, cost-effective repair solution while ensuring the safe operation of the bridge link. The structural repair of the bridge link beams presented several challenges that needed to be addressed.
The complexity of the beams required a solution capable of forming around the unique geometry. Additionally, achieving compression on corroded beams was crucial to ensure adequate adhesion of the repaired elements. The repair was carried out without the need for fabrication, hot work, or heavy lifting to minimise downtime and associated costs. The chosen solution required a design life of 20 years to align with the remaining lifespan of the asset.
What we did
To meet the specific requirements of the structural repair, our team employed a combination of two advanced fabric systems:
- Technowrap™ SRS (Structural Repair System)
- Technowrap™ HPPRS (High-Pressure Pipe Repair System)
By combining these fabrics, we created a bespoke laminate solution tailored to the unique repair scenario of the bridge link beams.
The repair process involved the following steps:
Assessment and preparation: The bridge link beams were thoroughly assessed to identify the extent of corrosion and damage. The corroded areas were cleaned and prepared for the application of the composite repair system.
Fabric selection and laminate formation: Technowrap™ SRS and Technowrap™ HPPRS fabrics were selected based on their individual strengths and characteristics. A customised laminate was created, leveraging the unique properties of each fabric to achieve optimal strength in the correct load path.
Application: A supervisor and two technicians were deployed to carry out the repair. The laminate system was applied to the bridge link beams, ensuring full coverage and conformity to the complex geometries of the structures. The installation process required no fabrication, hot work, or heavy lifting, streamlining the repair and minimising downtime.
Quality assurance and longevity: Rigorous quality assurance measures were implemented to verify the effectiveness of the repair. The composite laminate solution was designed to provide a 20-year design life, aligning with the remaining asset life.
Results
The successful implementation of the composite repair solution for the bridge link beams provided several outcomes and benefits, providing a long-term solution designed to last the remaining 20-year life of the asset. This ensured the continued safe operation of the bridge link and minimised the need for future repairs or replacements. Additionally, the repair solution required no fabrication, hot work, or heavy lifting. This streamlined the installation process, reducing downtime and associated costs. In terms of cost, the composite repair solution offered a cost-effective alternative to full beam replacement, saving the client significant expenses while maintaining structural integrity.
The quick application of the repair solution ensured the safe future operation of the bridge link and the repaired beams were capable of withstanding the operational loads and environmental conditions in the Dutch North Sea.
The structural repair project for the bridge link beams showcased our team’s expertise in developing and implementing advanced composite solutions for complex geometries. By combining Technowrap™ SRS and Technowrap™ HPPRS fabrics, we successfully addressed the challenges posed by the client. The efficient, cost-effective, and reliable repair solution enabled the client to continue safe operations and provided longevity of the asset in the Dutch North Sea.
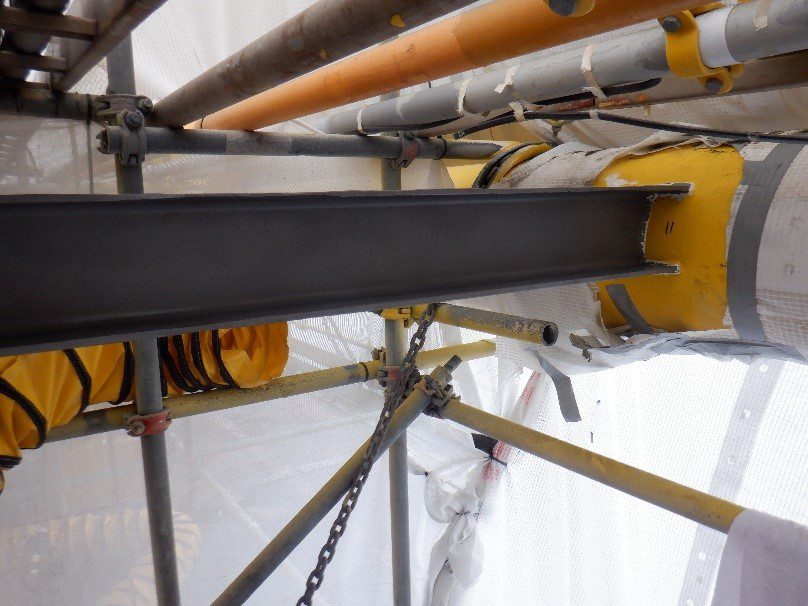
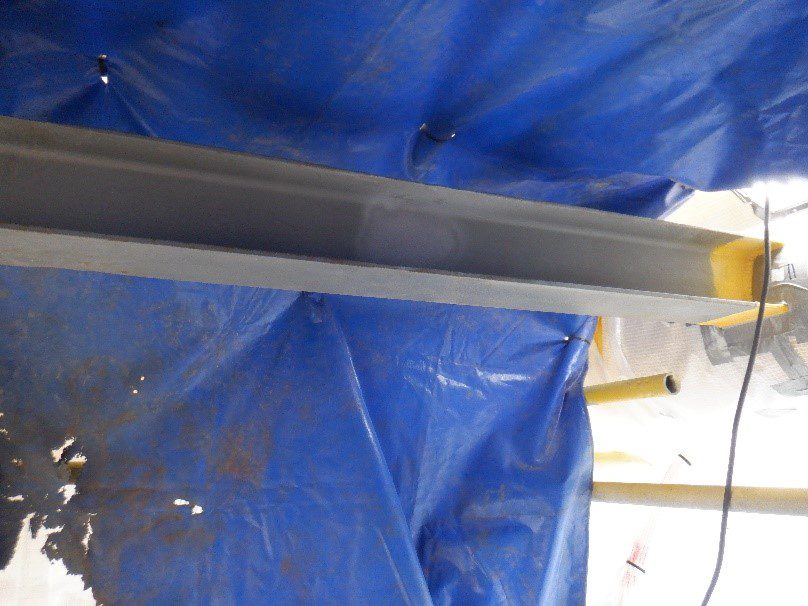