Client challenge
Our client’s 32” produced water line, was exhibiting significant internal erosion and corrosion, leaving a minimum remaining wall thickness of just 4mm. The extensive scope of the repair encompassed approximately 550 meters of pipeline, including various saddle supports, some of which were welded. The client also stipulated the need for a qualification test for the proposed repair solution, to be conducted on-site before the actual repair implementation.
What we did
Our solution began by defining a comprehensive scope of work, which included engineering an innovative design to ensure a 20-year repair lifetime. This encompassed providing trained personnel and the necessary materials, specifically Technowrap™ 2K with Technowrap™ HP PRS, to execute the repair. The line’s design parameters included a pressure of 47 bar g and a temperature of 82ºC. We meticulously developed an installation procedure for the composite repair, which was thoroughly tested and approved by the client before on-site installation. To ensure complete encapsulation of the pipeline, we also devised a detailed lifting plan for the pipeline over the supports. This plan addressed additional requirements, including applying the repair in areas where the pipework rested on the pipe supports.
Results
The execution of the qualification test was a resounding success, meeting the client’s approval and verifying the effectiveness of the repair solution. The repair was installed, confidently meeting the design pressure of 47 bar g and operating within the specified temperature range of 82ºC. Our detailed lifting plan was meticulously executed, ensuring the complete encapsulation of the pipeline. This case study showcases our dedication to delivering reliable and enduring solutions, providing clients with the confidence to address complex challenges in maintaining critical infrastructure.
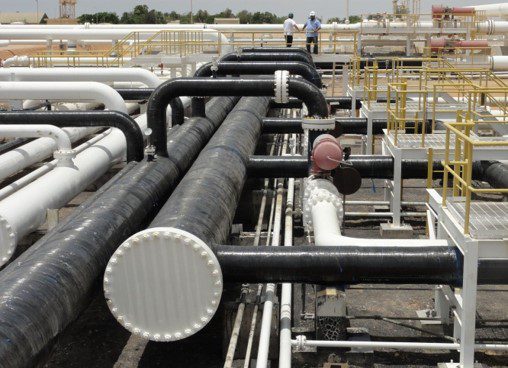
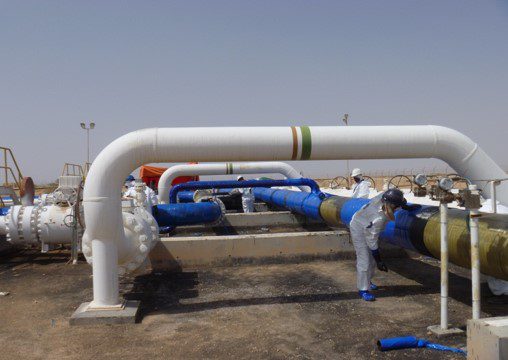
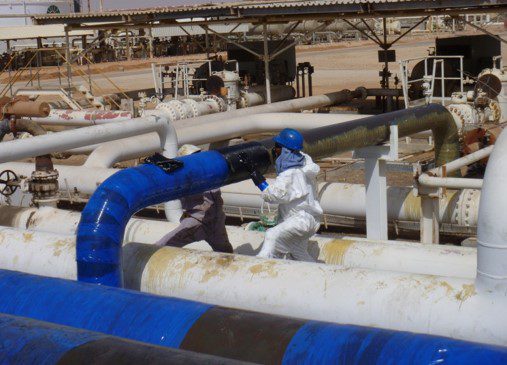