Client challenge
A global energy operator faced a critical challenge with the heli fuel storage and transfer skid on a platform, a crucial component of their operational needs. The skid, constructed from carbon steel was experiencing significant loss due to external corrosion. Our client urgently required a robust solution to address the corrosion issue and restore the integrity of the skid to ensure continued safe and efficient operations.
What we did
We devised a comprehensive strategy to mitigate the effects of corrosion and prolong the service life of the skid. To achieve the required cleanliness for appropriate adhesion levels, our technicians bristle blasted the landing areas to ST3 giving a minimum surface roughness of 40 microns, this was calculated and designed for within the engineering parameters. Our team formulated an engineered design calculation and sketch tailored to the specific requirements of the repair which was reviewed and approved by our client. Drawing upon our extensive experience in structural integrity, we developed a robust repair plan aimed at addressing 2 main areas of concern. The repair solution involved the application of 1 layer of 2K and 8 layers of SRS using ICRs low temperature resin, meticulously executed by our expert team.
As part of the scope of works, we had to fashion a composite mould to bring elements of the structure together in a suitable manner to apply the composite wrap. Our team used Technowrap 2K cloth to create the mould from an intact part of the skid to have the correct angles and dimensions to apply to the sections of concern. This proved paramount in the success of our Technowrap application and bringing back the structural integrity to the Heli-skid.
Results
This repair, achieved a design life of five years with a design temperature of 50 °C, ensuring prolonged serviceability and reliability. The composite repair is designed to withstand the full applied load and axial bending motions which have been calculated and adhered to ensuring the Technowrap engineered repair is compliance with ISO 24817.
Featured articles
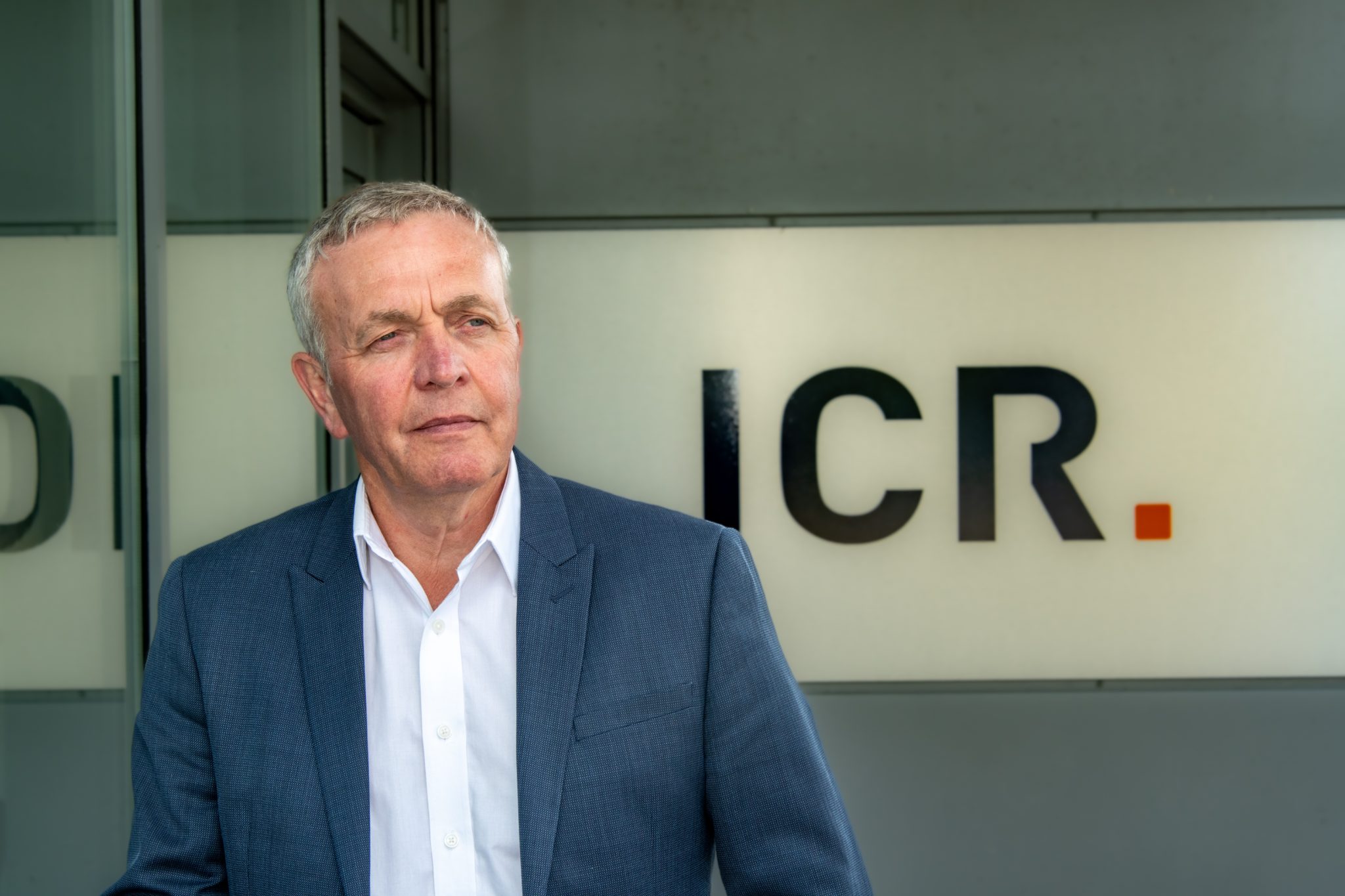
University of life stands Govan-raised engineer in good stead
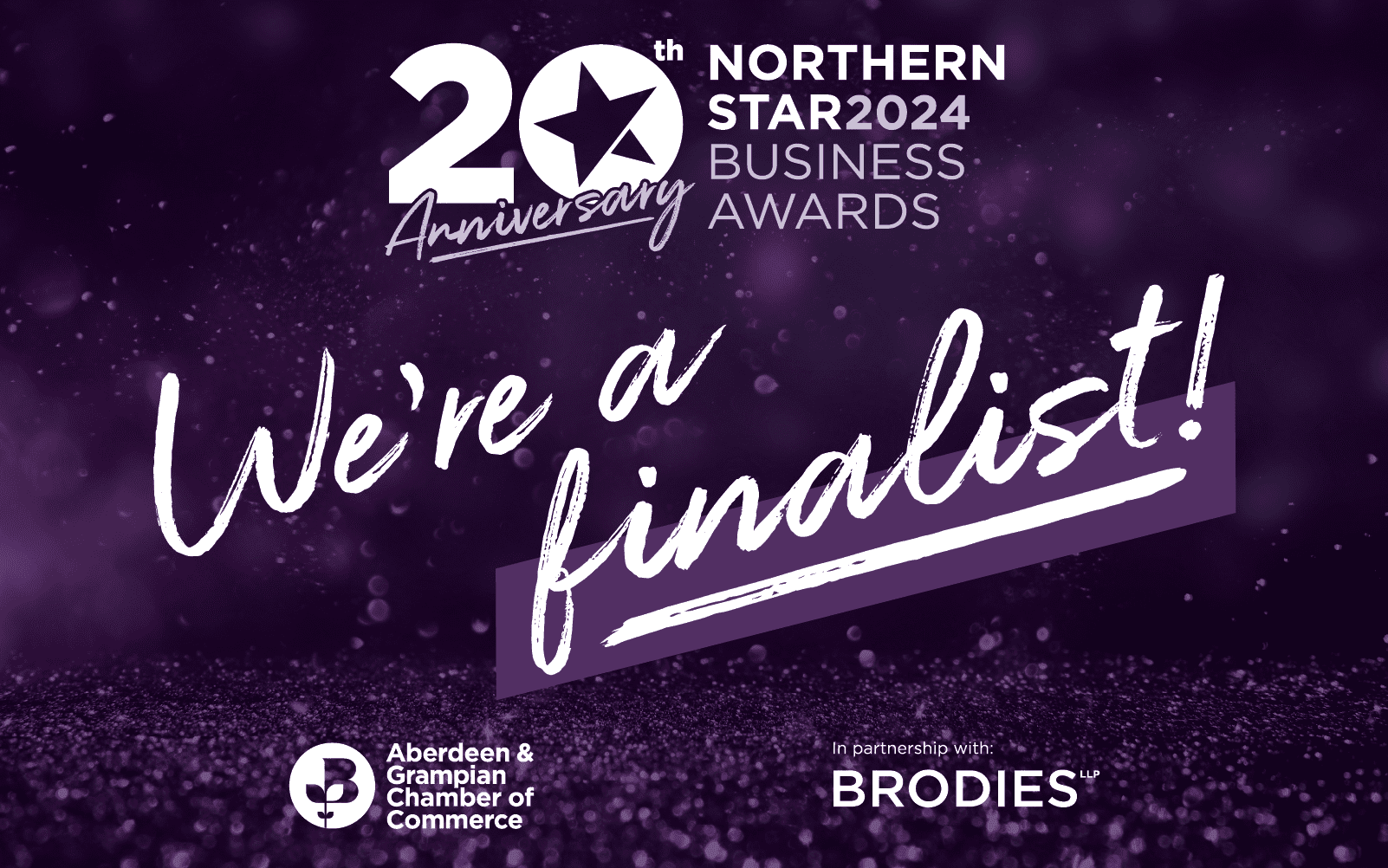
ICR Group shortlisted for Business of the Year
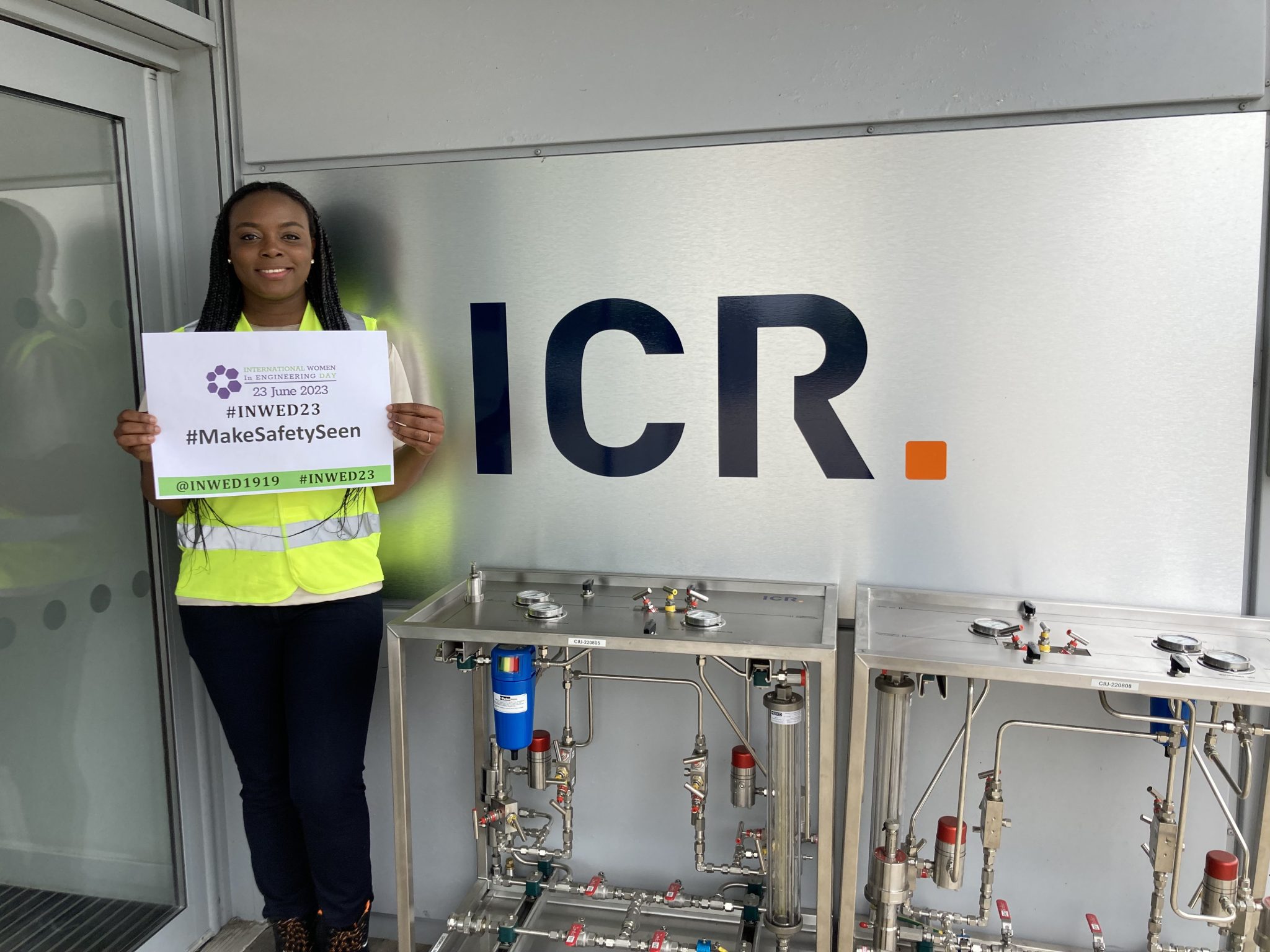