Date: April 2023
Client: National Oil and Gas producer
Location: UAE
Client challenge
Our client is a prominent energy operator based in the Middle East and approached our team with a critical repair project involving a de-ethaniser column. The objective was to address specific problem locations within the column, spread across six different vertical positions. The project required a reliable and efficient solution to mitigate the risk of further damage, while ensuring minimal revenue loss during the repair process.
What we did
The de-ethaniser column, measuring just over 7.5 metres in height with a diameter of 3.05 metres, had encountered structural issues and cracks that needed immediate attention. Traditional repair methods involving hot work were not feasible due to the potential for revenue loss, and safety concerns associated with the presence of flammable substances. In addition, the repair solution needed to consider the prevention of galvanic corrosion and provide pressure containment capabilities while limiting stress on the steel structure to prevent crack propagation.
Our team proposed an innovative repair solution utilising advanced composite materials, specifically glass fibre and carbon fibre, to address the unique challenges faced by our client. By employing this composite approach, we ensured a durable and efficient repair without resorting to hot work, minimising any potential revenue loss.
The repair process involved multiple steps:
Surface Preparation: The affected areas of the de-ethaniser column were thoroughly inspected, cleaned, and prepared for the application of composite materials.
Galvanic Corrosion Prevention: To safeguard against galvanic corrosion, a single layer of glass fibre was applied as a barrier between dissimilar metals present in the column.
Composite Application: A total of 20 layers of carbon fibre, employing various lay-up techniques, were strategically applied to the problem locations within the column. This composite configuration aimed to provide pressure containment, withstand axial loads, and limit stress on the steel structure to prevent further crack propagation.
Curing and Quality Assurance: The composite layers were allowed to cure under controlled conditions to ensure optimal bonding and structural integrity. Rigorous quality assurance tests were conducted to verify the effectiveness of the repair.
Results
The successful implementation of the composite repair solution resulted in several significant outcomes and benefits:
Enhanced structural integrity: The repaired de-ethaniser column demonstrated improved structural integrity, as the composite materials effectively contained pressure and limited stress on the steel structure.
Avoidance of galvanic corrosion: The glass fiber layer acted as an effective barrier, preventing galvanic corrosion and ensuring long-term durability of the repaired column.
Reduced loss of revenue: By avoiding hot work, our repair solution eliminated the need for significant downtime and revenue loss that would have occurred with traditional repair methods.
Extended service life: The repair solution was designed to provide a five-year lifetime, ensuring the longevity and reliability of the de-ethaniser column.
The de-ethaniser column repair project demonstrated our team’s ability to develop innovative solutions tailored to our client’s specific requirements. By leveraging our advanced composite materials, we successfully addressed the structural issues of the column, mitigated the risk of galvanic corrosion, and ensured the safe and efficient operation of the facility. Our client benefited from a cost-effective repair solution, minimal revenue loss, and an extended service life for their critical equipment.
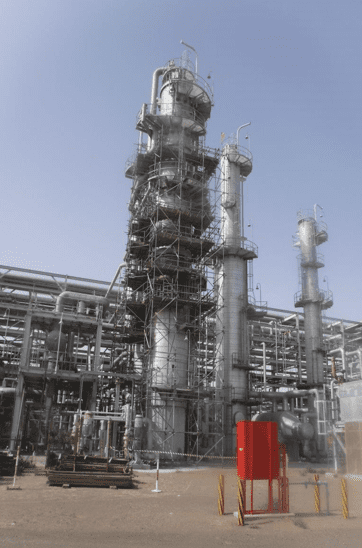
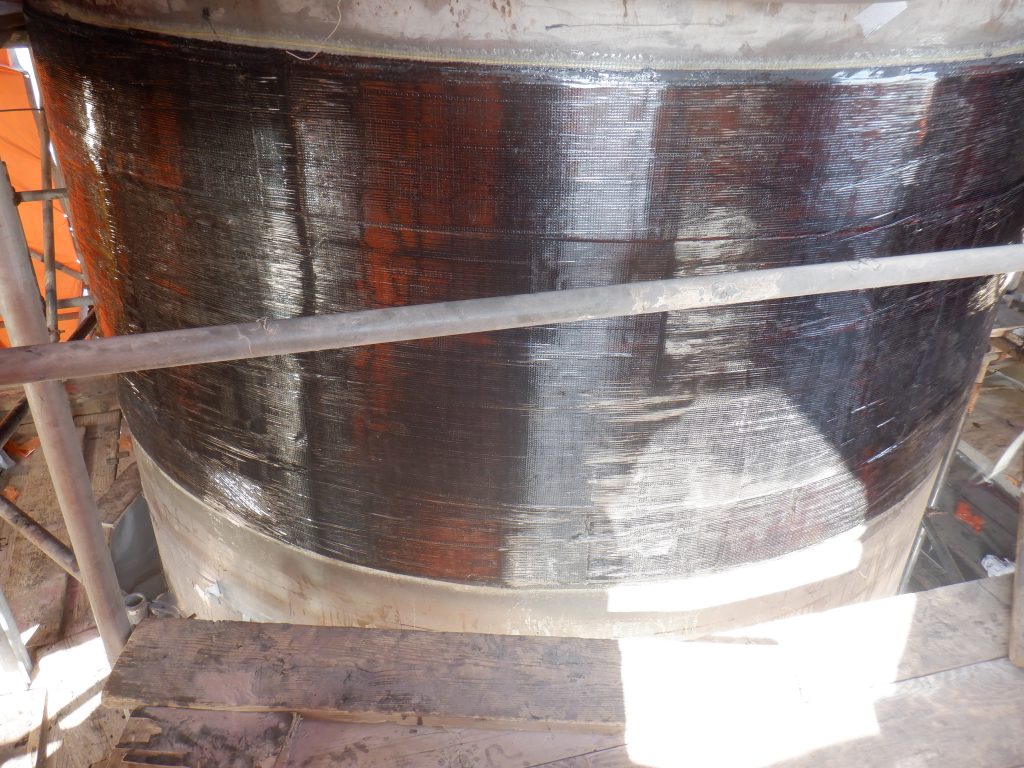
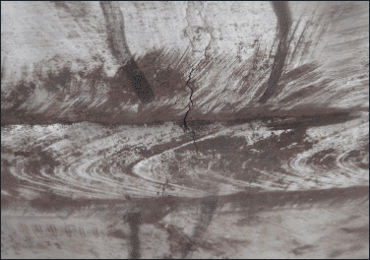
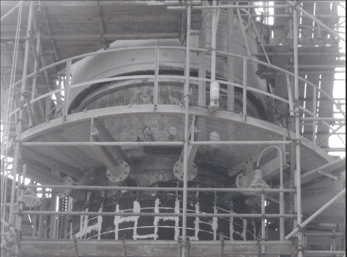