ICR has been awarded a long-term hire contract with TAQA Bratani Limited (TAQA), for the provision of its Quickflange™ weldless connections for TAQA’s UK-based operations. The contract is for two years with a two-year extension option.
Lindsay Anderson, Head of Sales – Quickflange™ at ICR, said:
“We are delighted to secure this contract with TAQA, who we have been working with for almost 10 years. Quickflange™ offers clients permanent repair options minimising downtime or the need for hot work permits, making it a cost effective and efficient way of performing repairs. The technology has a long-standing track record, particularly in the North Sea & Norway sectors, but we are now seeing a growing demand for solutions onshore, out with the traditional oil and gas sector as well as our international locations throughout the globe.”
For almost 20 years, ICR’s patented Quickflange™ technology has built up a proven track record as a leading provider in cold work solutions, offering clients permanent repair options for improving pipeline integrity and flow assurance whilst eliminating the need for welding or hot work with zero emissions generated. With an extensive range, Quickflange™ is a safe, cost-effective and efficient solution generating an 80% time saving over traditional welding – enabling the technology to be used as an emergency solution or for any planned maintenance and repair work.
OMNI Integrity, (an ICR company), is delighted to announce a 12-month contract award, with extension options, to provide full asset integrity lifecycle management software to support THREE60 Energy’s UKCS and International Duty Holder assets.
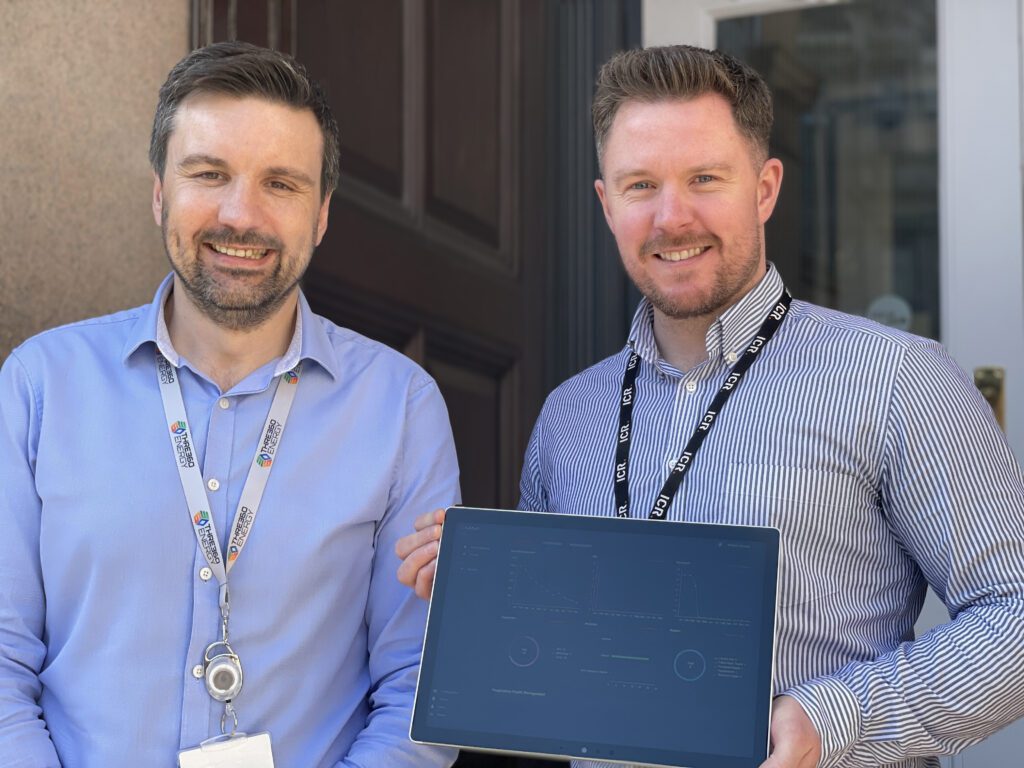
OMNI provides a complete 360 data-capture solution and can integrate with Internet of Things (IoT) sensors and mobile tablet technology to cover all inspection and condition monitoring methods.
William McLean, Director of OMNI, said:“We are delighted to support THREE60 Energy as a technology partner and enhance their robust digitalisation strategy. OMNI covers the entire integrity process, bringing a 40% time saving on manual integrity management methods. This will provide THREE60 Energy greater control over integrity data whilst providing a platform for integrating advanced inspection methods. We are really looking forward to working together on this collaborative journey.”
Stephen Diplock, Operations Director at THREE60 Energy said: “OMNI is a great digital fit for our business. We have a broad technology offering across our services and solutions and this enables and supports our shared vision of adding real value for our customers through the full asset lifecycle.”
For more information on OMNI, please visit – www.omni-integrity.com
ICR Integrity (ICR), a leading global provider of integrated maintenance and integrity solutions to the oil and gas, power, chemical and nuclear industries, has signed an Authorised Service Centre agreement with Milton Roy. The agreement is expected to be worth around £900,000 over three years.
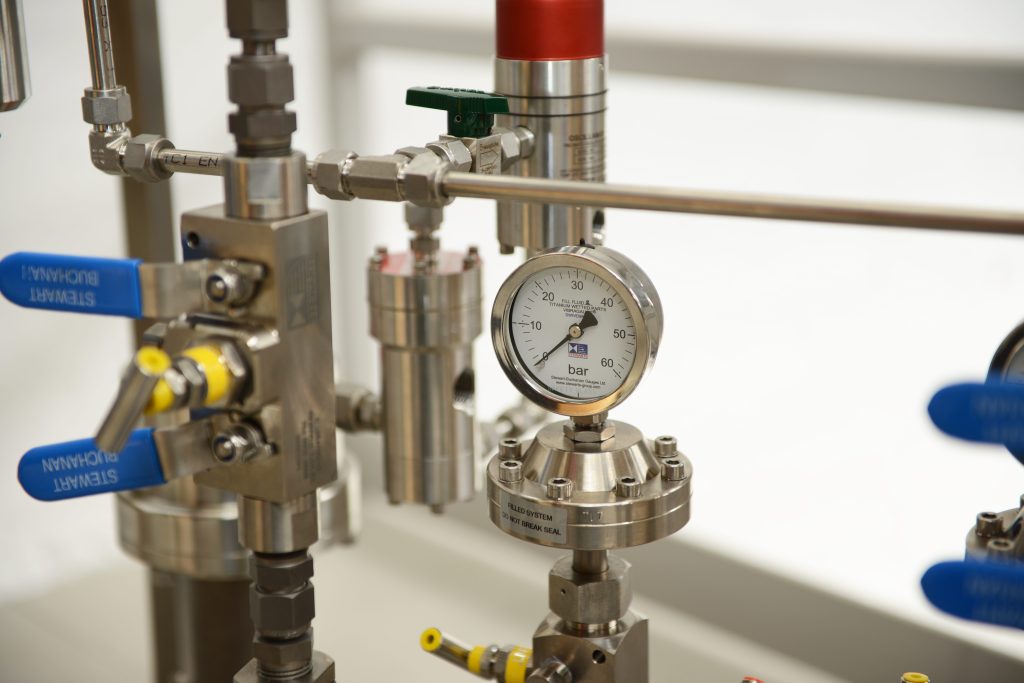
ICR’s Chemical Injection business (CIU) provides pneumatic and electric drive chemical injection pump services and has one of the largest rental fleets in Europe. The agreement will see ICR, and its personnel, deemed qualified to service and repair Milton Roy products, including cover under Milton Roy’s manufacturer warranty. The agreement covers oil and gas, oil refinery, petrochemical and water treatment services industries in the UK.
Neil Birnie, Key Account Manager – CIU, at ICR, said: “This agreement will play a significant part in the continued growth of the CIU business within ICR. We have an extensive track record, particularly in the North Sea and Europe, and the addition of the Authorised Service Centre agreement with Milton Roy will allow us to expand our offering to both new and existing clients.”
Milton Roy is a world-leading manufacturer of controlled-volume metering pumps that set the industry standard for performance, accuracy and durability. The company has an 85-year track record in the development and manufacture of equipment that accurately controls fluids ranging from water to high viscosity polymers, corrosive or abrasive chemicals, toxic substances and other difficult pumping elements. Milton Roy is a brand of Ingersoll Rand.
Maryam Baldwin, Business Development Manager UK and Northern Europe at Milton Roy, said: “With years of expertise, ICR will provide aftermarket services on Milton Roy equipment when and where you need it, in even the most challenging environments. This will ensure a cost-effective and prompt response when our clients need support on any maintenance or installation supervision for Milton Roy products.”
ICR Integrity Ltd (ICR) is a leading provider of integrated maintenance, repair and production solutions for industrial related services to the offshore oil & gas, power, chemical, nuclear and defence industries worldwide.
Following a competitive process, ICR Integrity (ICR), global provider of specialist maintenance, integrity and inspection solutions, has been selected for participation in the second Fit for Offshore Renewables (F4OR) North East Scotland programme, funded by the Energy Transition Zone (ETZ).
ICR has a proven track record in the offshore renewable energy sector, including experience using its Quickflange™ and Technowrap™ repair technologies at offshore wind substations. Both cold work technologies create zero emissions during installation and bring the benefit of cost and time reduction as well as resulting in less POB to renewables clients. The company’s drone inspection business unit, Sky-Futures™, has also delivered offshore wind turbine and substation inspections since 2014 within the UK, Belgium and Denmark for major clean energy companies. The F4OR programme will enable continued investment and focus on ICR’s ongoing strategic support for the energy transition.
The 12-18 month programme is governed by the Offshore Renewable Energy Catapult (OREC), working with a senior Industry Advisory Group, and follows a range of regional F4OR programmes, rolled out across the country since 2018. Reputable companies that have been selected, ranging from SMEs to Tier 1 contractors, work together in a cohort in order to improve and develop their corporate profile and competence in the sector, leveraging each other’s expertise.
Britney Houvet, Business Development Director, ICR, said: “We are entering 2022 with a really positive outlook and this fantastic news comes at a time when we continue to strengthen our focus on cleaner energy markets. We are building a pipeline of projects within these existing and emerging industries supporting our ongoing expansion globally and are excited to build on our track record. We have experience working in multiple clean energy industries including on-line leak sealing and specialist on-site machining in biomass with tier one contractors and Sky-Futures™ recently completed methane detection surveys on seven European biogas sites together with its partner SeekOps®.
ICR continues to invest in its international partner network and has successfully focused on environmental, social and governance (ESG) initiatives during 2021, including the launch of online training for international customers and partners to assist in the reduction of footfall on offshore assets and client sites. We are very much looking forward to working with Catapult and our cohort companies to get the company further prepared for work in offshore renewables, and we are excited to be exhibiting our solutions at the upcoming Scottish Renewables Offshore Wind conference in Glasgow on the 8th and 9th of March.”
ICR operates in global locations including Europe, MENA, Australia, ASEAN and North America.
In the realm of engineered composite repair solutions, we are able to propose Finite Element Analysis (FEA) to assess more complex scenarios
What is FEA?
Finite Element Analysis (FEA) is the process of simulating the behaviour of a part (or assembly) under given conditions. We use advanced computing to generate 3D models to simulate defects and potential repairs. Within these models are a number of parameters which are changeable allowing us to simulate the effect on the piece as these are varied. We can inspect the likely impact of changes to these parameters, modelling a range of external conditions on the effectiveness of our repair solution.
The process allows us to demonstrate the effects of differing forces, levels of repair (layers, area repaired etc.) in a simulated environment, qualifying and visualising the theoretical solution thus validating the benefits of our repair(s).
Particularly beneficial in instances of complex geometries, FEA allows clients and engineers to make various assessments of static load, vibration analysis and thermal analysis – allowing repairs to be modelled prior to installation and can give an overview of entire systems and critical areas, together with a better understanding of the structure deformation/stresses. These assessments allow us to understand the various stress/strain field in the different composite layers of the repair. This enables us to propose the most appropriate repair solution for complex structures.
What are the benefits of FEA?
Reduced physical testing scope:
FEA enables ICR to provide virtual prototyping capability to reduce and improve physical testing scope while increasing the confidence in the proposed repair solution.
Improved communication with clients and third party:
FEA allows clients to visualise ICR customised repair prior to application. This in turn allows ICR partners to notify more easily if additional loading should be assessed or/and if there is a need to further strengthen a specific location due to future development.
FEA will also strengthen the design package ICR share when third party design approval is required for a repair.
When would this service be used/valuable?
This service is most valuable if one of the following conditions is met:
- Large testing scope is envisaged
- FEA could help reduce the overall testing scope while increasing client and third-party confidence
- Complex loading scenario:
- Various loading can be modelled
- Vibration analyses can be performed
- Heat transfer can be assessed
- Complex structure
- Larger structure can be assessed
- The influence of a localised repair on the overall structure can be assessed
- Third party approval
- FEA analysis can strengthen the design package shared for third party approval which could in turn reduced the approval time.
ICR has significant experience in the field of composite engineering. This, coupled with our Finite Element Analysis (FEA) offering, means we are able to provide in-depth analysis and insight into a variety of complex loading scenarios for the use of composite repairs in both pipework and structures.
Over the last year Tristan Huet Ceng IoM3, ICR’s Structural FEA Engineer, has been developing the material models to use in performing analysis on complex composite repair scopes e.g structural walkways, high pressure pipes, pipe supports and crane boom rests. ICR are now in a position to offer our clients a comprehensive solution to verify the use of composite repairs in complex loading scenarios.
Click here to access our FAQ, or get in touch with Shona Mackenzie or Tristan Huet Ceng IoM3 if you are interested in hearing more about our capabilities.
We are delighted to announce that, after a competitive tender process, we have secured a Master Service Agreement for the provision of engineering repair services for all of TAQA Group’s northern and central North Sea assets.
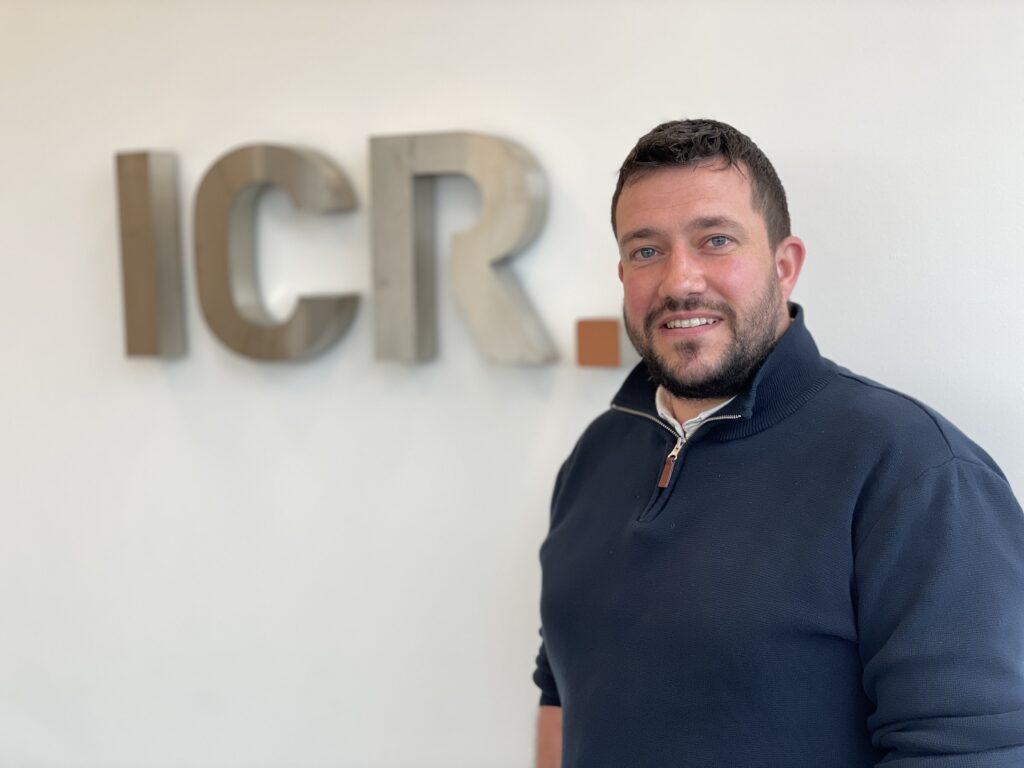
The initial contract is for five years with two 1-year extension options.
Ryan Crabb Technowrap™ Key Account Manager for TAQA said: “We are delighted to be continuing our ongoing relationship with TAQA. We have a long history of working with TAQA so this is great news for the team.”
ICR Integrity has been awarded a long-term hire contract with Aker Solutions for the provision of Quickflange™ weldless connections for bp’s offshore assets in Angola.
The award recognises ICR’s commitment to growing the business further in West Africa having appointed Petrowork as its local partner, with offices in Luanda, for repair and integrity services including both Quickflange™ and Technowrap™ engineered composite repairs. This allows the company to hold equipment in-country and have local, trained technicians on-hand to respond quickly to client requests.
Phil Paterson, Business Development Manager at ICR, said: “We are delighted to secure this contract which builds on our existing long-term relationship with Aker Solutions. ICR is committed to supporting our global clients and we continue to invest in key regions to ensure a dedicated offering is always delivered. This contract follows on from the ongoing rental agreement and demonstrates the relationship we have with Aker Solutions as well the internationally recognised quality of the products and services we offer. Quickflange™ is qualified and approved to several international type standards and is proven in improving pipeline integrity which is imperative to our clients.”
Fred Nordheim, Supply Chain Manager Aker Solutions, added “We are very active in the region and the Quickflange™ technology has proven to be a safe and effective solution for us on our brownfield modifications and maintenance project. It’s great to continue working with ICR in Angola.”
Headquartered in Aberdeen, ICR operates in global locations with operational bases in the UK, Norway, Abu Dhabi, USA and Australia as well as partners in over 25 countries worldwide.
By Frankie Suarez, Business Manager, ICR’s Sky-Futures™
As the industry looks towards a zero emissions future, technology will play a vital role in supporting this transition. At Sky-Futures™, we are proving how advancements in UAS (Unmanned Aircraft System) and sensor technology can support many sectors both on and offshore in the drive to achieve Net Zero Targets.
Our recent partnership with SeekOps Inc provides end-to-end asset level methane emissions quantification, including data capture, analysis and reporting. By utilising the SeekIR® sensor mounted to a UAS, the technology can provide methane Leak Detection and Quantification (LDAQ) of an impressive 1SCFH from 100m. The technology was originally designed by the co-founders of SeekOps for use by NASA on the Curiosity Rover sent to Mars and has now been adapted for utilisation in many other industries, with Sky-Futures™ being a global service delivery partner. The SeekOps training team have delivered bespoke training to our highly experienced Inspection Engineers and Remote Pilots. This has enabled Sky-Futures™ to deliver methane emission quantification operations on and offshore in recent months.
The agile and accurate technology allows operators to increase their health, safety and environmental performance in a very cost effective and efficient manner. The comprehensive emissions inspection service is also completed in a fraction of the time of traditional surveys. As discussions continue to guide further regulation in this area, especially in the oil and gas sector, operators are required to understand and mitigate methane emissions. By providing quantified, actionable data, operators will be able to find solutions or mitigations in an efficient manner, whilst also showing positive accountability to the regulators.
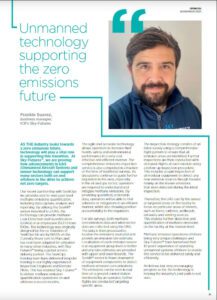
For site surveys, both methane concentration data and wind vector data are collected using the UAS. The data is then processed to localise the emissions source(s) and provide an emission rate estimate. Localisation of each emission source is at equipment group level or better and any rate estimates are provided with upper and lower bounds. The SeekIR® sensor is flown downwind of equipment components to detect methane emission concentrations. The emissions can be seen in real-time on a ground control station monitored by an operator, further flights are conducted targeting specific areas.
The inspection strategy consists of an initial survey using a comprehensive flight pattern to ensure that all emission areas are identified. Further inspections are then conducted with all repeat flights at each module using a follow-up inspection procedure. This includes a rapid inspection of all modular equipment to detect any new emission sources though focuses mainly on the known emissions that were detected during the initial inspection.
Thereafter, the UAS can fly the sensor at targeted zones on the facility to focus on particular areas of interest, such as flares, turbines, well heads, exhausts and venting sources. This enables further detection and quantification of methane emissions on the facility, at the module level.
Methane emission operations offshore bring very unique challenges and Sky-Futures™ have harnessed their 10 years’ experience of operating unmanned systems offshore to enable this service to be delivered safely and efficiently.
Ambitious but very encouraging progress so far, the technology is helping the industry’s joint path to Net Zero.
Read Frankie’s article in the AGCC Business Bulletin (November, 2021) here
Sky-Futures™, an ICR Integrity company who provide drone based inspection services, has delivered a successful trial for its methane detection technology, SeekIR®, for its client Equinor.
Sky-Futures™ partnered with Texas based SeekOps® earlier this year to provide clients with an end-to-end service on its Unmanned Aerial Vehicles (UAVs) both onshore and offshore – this includes data capture, data analysis and reporting with the addition of its methane quantification technology to help clients locate leak sources. Equinor has already been successfully using the technology as they trial methane detection equipment.
XX, XX from Equinor, added: “As we look to a zero emissions future, we have been investing in trials of different methane detection technologies at our Kollsnes Gas Plant near Bergen in Norway and the most successful products will be utilised across Equinor going forward. The Sky-Futures™ team surveyed the entire gas plant for methane emissions and also performed a series of controlled release measurements. We have been impressed with how agile and accurate the technology has been and look forward to working with ICR and SeekOps® in the future.”
The methane detection sensor on The SeekIR® sensor can provide methane Leak Detection and Quantification (LDAQ) of an impressive 1SCFH from 100m.
Suzanne Donald, Head of Sales (Oil & Gas) at Sky-Futures™, said: “It’s exciting to be able to bring this technology to our clients in different industries helping them to achieve their best health, safety and environmental performance whilst enabling cost-effective, comprehensive emissions inspection in a fraction of the time required by traditional surveys. This results in significant cost savings for our clients. We are now completing methane quantification surveys for our clients onshore and offshore in the UK, Scandinavia and Europe making meeting Net Zero emissions all the more achievable.”
The technology was originally designed by the co-founders of SeekOps® for use by NASA on the Curiosity Rover sent to Mars and has now been adapted for utilisation in other industries, onshore and offshore, with Sky-Futures™ being a global service delivery partner. The team can then also further assist clients in meeting their Net Zero emissions targets by utilising ICR’s leak sealing solutions.
For further information on our Sky-Futures™ and SeekOps® methane detection contact Suzanne Donald on +44 (0) 7903 857988 or email Suzanne.Donald@ICR-world.com